引言
燃料组件是核反应堆的核心释热部件,由燃料棒以及上管座、骨架等部分构成。骨架部分,类似于建筑物中的框架结构,为整个燃料组件提供了稳定的支撑。骨架的主要组成材料是锆,包括定位格架和导向管等关键部件,这些部件的连接主要通过焊接实现。
然而,焊接锆棒、锆管等锆合金并非易事,其焊接性能受多个工艺参数影响,本文先介绍了电阻点焊工艺的概念和特点,并从焊接压力、焊接时间和焊接电流三个方面分析了焊接工艺参数对锆合金焊接性能的影响。
1、电阻点焊
骨架焊接是采用电阻点焊的方式将定位格架和导向管焊接为成型骨架的一种工艺。电阻点焊(ResistanceSpotWelding,RSW)是电阻焊的一种,简称点焊。电阻点焊是将被焊零件装配成搭接接头并压紧在两电极之间,利用电流流经零件本身和其接触面间产生的电阻热,将其接触面的局部加热到熔化状态,在电极压力下,形成冶金连接的一种电阻焊接方法[1]。
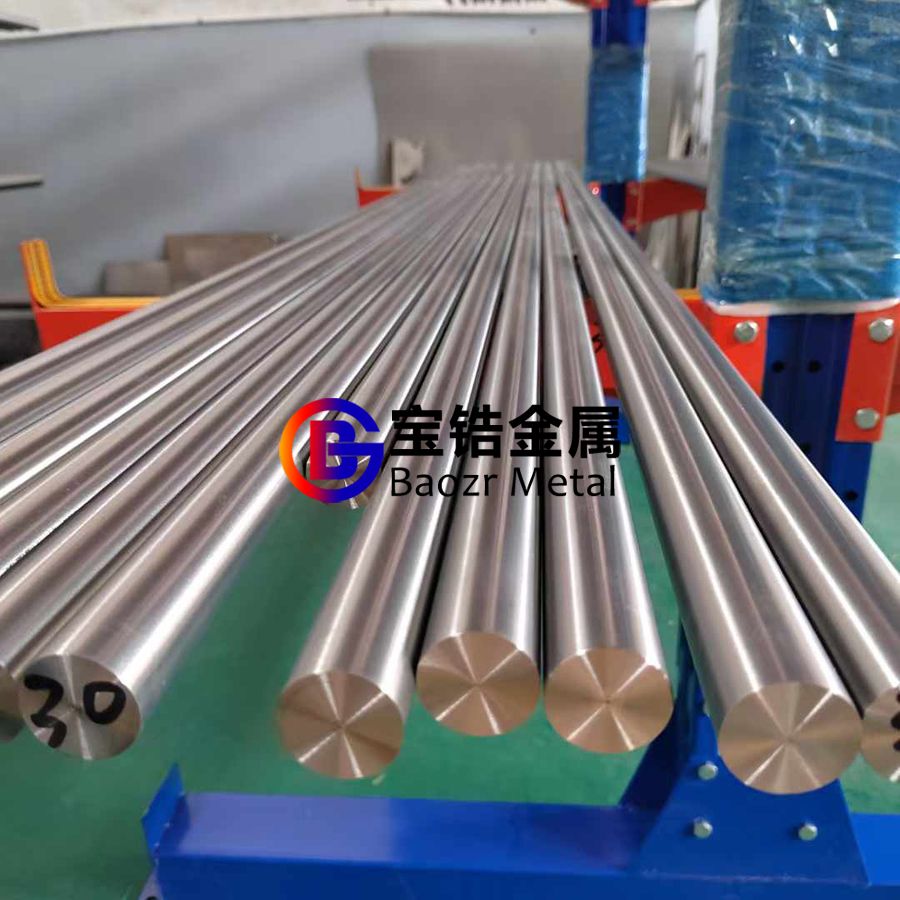
点焊的主要焊接参数是焊接电流、焊接(通电)时间、电极压力和电极尺寸等。焊接电流是指焊接时流经焊接回路的电流。
Q=I2Rt.
即点焊产生的热量Q与电流I的平方、电阻R和通电时间t成正比。
焊接接头的质量最终反映在接头的剪切强度上,而接头的剪切强度主要取决于焊点的尺寸以及焊点表面和内部的质量[2]。
表面质量是指焊件表面电极压痕深度大小,有无表面飞溅、烧伤、裂纹、粘连电极、翘曲变形及表面抗腐蚀性能的变化等。内部质量则指熔核的几何尺寸、形状,有无超标的裂纹、缩孔等内部缺陷,以及热影响区金属的组织与力学性能有无明显的变化。
2、锆合金焊舌与导向管试样焊接
焊舌与导向管试样是模拟产品实际焊接状态的试样。焊舌呈片状,上有与导向管贴合的焊接区;导向管直径为Φ11.5mm,内部有扩张芯轴起到支撑与导电的作用。焊接的状态如图1所示。
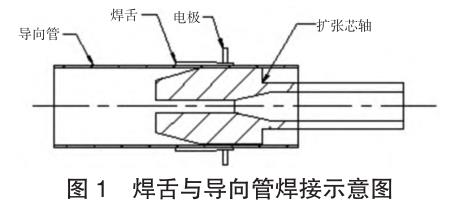
焊点的形成有以下四个阶段:
1)预压阶段,通电前电极压在零件上施加预压力。
2)焊接阶段,通电加热形成熔池。
3)维持阶段,维持压力,断电冷却。
4)休止阶段,电极抬起,准备下一次焊接。
2.1电极压力
电极压力是指在焊接过程中,电极与被焊材料之间所施加的力。电极压力对焊接熔核尺寸有很大的影响,这是因为尽管体电阻率与压力无关,但接触电阻对压力的分布及接触界面的表面条件都很敏感[3]。而电极压力不仅影响电极与母材之间接触面积的大小,也影响接触电阻的值。
首先,压力的大小会直接影响电极与母材之间的接触面积—压力越大,接触面积越大,从而使得电流更为均匀地传递到母材,有利于形成较大的熔核。其次,电极压力的大小也会影响到电极与母材之间的接触电阻—压力越大,接触电阻越小,因为电阻降低,导致电流的损失降低,使得电流能更有效地转化为焊接热量,有助于生成更大的熔核。但是,这只是在一定范围内有效。
当电极压力超过某一阈值后,虽然接触电阻进一步降低,但增大压力会引发两个主要问题:一个是造成过大的散热,导致热量不能集中在焊点,结果是熔核尺寸可能变小;另一个可能会引发电极过度磨损,影响焊接质量。而且,电极压力对焊接过程中的接触界面的表面条件也十分敏感。这是由于表面条件决定了电阻的状态,当接触界面光滑、无氧化物覆盖时,接触电阻就会较小,反之,则会增大接触电阻。电极压力可通过改变接触界面的表面条件,进而影响接触电阻的大小,从而影响焊接效果。
当电极压力增大时,接触电阻会降低,这意味着焊接过程中的散热会增加,总的热量就会相应减少。
由于这个原因,焊点的熔核尺寸会变小,因此电极压力不宜过大。
另一方面,如果电极压力过小,母材的接触就会不良,导致接触电阻不稳定。这将导致熔核的尺寸产生较大波动。过小的电极压力也可能引发严重的焊点喷溅,这在焊接过程中是需要尽量避免的问题。因此,必须确保电极压力达到适当的值,从而保证焊件接触的稳定性。
对于锆合金焊舌与导向管试样焊接,采用焊接电流2.4kA进行实验,结果如表1所示。
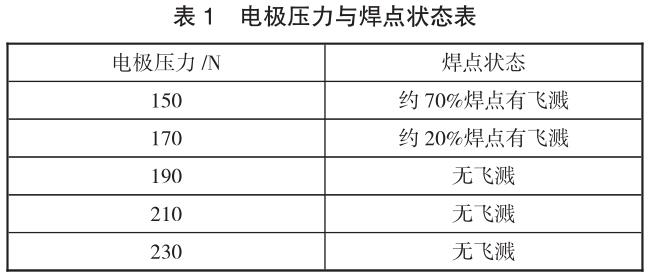
考虑到压力可能出现波动,可根据焊接实际情况,选择210N及以上作为电极压力,可保证接触电阻稳定且不会产生喷溅。
2.2焊接时间
焊接时间如果很短,焊接区由于热量不足无法形成熔核,焊接时间增加达到临界点后,焊点将形成熔核,之后随着时间增加,焊点熔核逐渐增大,焊点剪切力也随之增加,直到最后产生喷溅。根据实验结果,最终选择20ms作为焊接时间。
2.3焊接电流
由于电阻点焊产生的热量与电流的平方成正比,所以焊接电流对焊点的力学性能影响最大。
采用厚度0.4mm焊舌和壁厚0.5mm的Φ11.5mm的导向管的薄壁试样进行焊接实验。母材材质为Zr-4合金,压力采用210N。
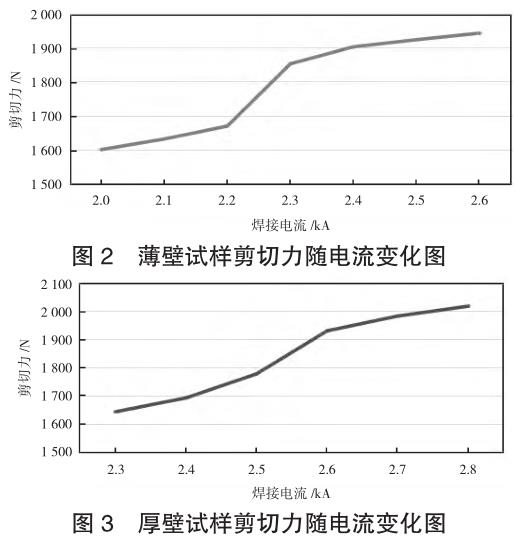
如图2、图3所示,随着焊接电流增加,焊点剪切力逐渐上升,折线的尾端斜率逐渐降低,说明其增长速度逐渐缓慢。若继续增加焊接电流,温度场将进入准稳定状态,可能导致金属过热造成喷溅等缺陷,从而威胁焊接质量。
而当焊接电流过小时,尽管电极压力适中但焊接区却无法达到足够的温度以形成熔核。此时,必须提高焊接电流至一定阈值,才能确保焊点成功形成并达到所需的剪切力,使焊接过程能够正常进行。
图2和图3中的所有试样都能满足当前的剪切力要求,后续可根据不同要求,确定焊接电流参数。
2.4工艺参数相互影响
根据不同的焊接电流与焊接时间可形成两种规范:硬规范和软规范。它们的核心区别在于所采用的电流大小及其与焊接时间的配合。硬规范指的是使用大电流进行短时间的焊接,它的优点在于能够快速产生高温,使得金属瞬间达到融化状态,从而短时间内完成焊接,大大提升了生产效率。然而,大电流焊接对设备的稳定性要求较高,稍有不慎便会引发喷溅等问题。
相对于硬规范,软规范则是使用小电流进行长时间的焊接。这种方式虽然焊接时间更长,但由于电流较小,因此对设备的稳定性要求较低,也更不易出现喷溅等缺陷。此外,软规范能够保证金属在焊接过程中均匀加热,避免了因局部过热而产生的金属结构变形,因此其焊接质量通常更高。
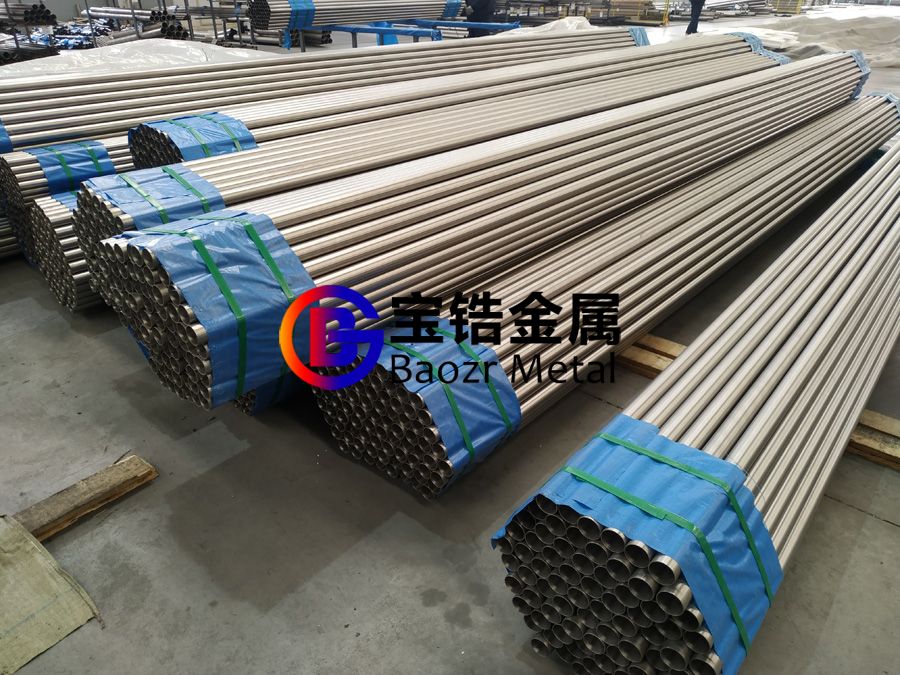
在实际生产中,选择硬规范还是软规范,需要根据具体的产品特性、生产设备以及生产效率的要求来决定。两者之间需要找到一个平衡点,才能达到最佳的焊接效果。
3、结论
适当的焊接工艺参数(包括电极压力、焊接时间和焊接电流等)对于确定锆合金焊舌与导向管的焊接质量至关重要。本文的分析理论与实践充分证明,通过合理的设置和调整焊接参数,可以有效地提高焊接的质量,同时也能有效地避免因为参数设置不当而出现的问题,比如焊点飞溅或焊点性能不合格等。
以当前工艺要求对锆合金焊舌与导向管进行焊接时,焊接压力应控制在210N以上,避免出现飞溅;焊接时间可控制在20ms;焊接电流根据不同工艺要求,厚壁选择2.3~2.8kA,薄壁选择2.0~2.6kA。的增加而增加,对各车间粉尘的特性进行了研究并对工艺进行改进后,粉尘浓度得到有效控制。
1)对钢铁企业的生产设施情况及生产规模、工艺进行分析。
2)对企业烧结、炼铁、炼钢以及轧钢车间16个采样点的粉尘浓度进行了实验研究,并根据实验结果对其特性进行了分析。
3)针对烧结、炼铁、炼钢车间的除尘控制工艺进行研究与改进,根据结果分析可知粉尘污染控制技术有较好效果,为后续钢铁车间粉尘浓度控制研究提供了实践基础。
参考文献
[1]纪树东.机械加工车间环境影响分析及粉尘特性研究[J].科技致富向导,2014(11):148.
[2]房金乐,张朝晖,王建鹏.钢铁企业粉尘综合利用技术研究[J].山西冶金,2016,39(5):53-55.
[3]程茉莉,肖莹,隋鸿志.钢铁行业烟粉尘排放状况及控制措施趋势探讨[J].能源与环境,2016(2):57-60.
[4]贺利清.钢铁厂车间环境粉尘污染控制技术分析[J].山西冶金,2023,46(4):66-67.
相关链接