锆合金具有较低的热中子吸收截面、优异的耐腐蚀性和良好的力学性能与加工性能,被广泛应用作核反应堆的包壳材料和结构材料[1-3]。锆合金在室温下为hcp结构的α-Zr,其结构对称性较低,独立滑移系较少,塑性变形过程中通常需要滑移和孪生协同开启[4,5]。其中,柱面滑移的临界剪切应力(CRSS)相对其他滑移系最小,是锆合金变形过程中最容易开启的滑移系[6],锥面滑移和基面滑移开启以协调变形[7,8]。当晶体取向不利于滑移时,孪晶开启并使晶粒产生固定角度的取向改变[8,9]。锆合金带材在加工过程中易形成织构,导致材料各向异性,进而引起室温冲制过程发生开裂。因此,研究锆合金在冲制过程中的织构演变,分析冲制过程中的应变路径和变形机制之间的关系,对揭示冲制过程中影响开裂的关键机制、明确开裂敏感的晶粒取向具有重要的理论意义和应用价值。定位格架由锆合金带材冲制而成,冲制过程中的应变路径与成形零件的几何形貌、成形过程中的工艺条件以及材料性质等多种因素有关。Lei等[10]设计了近似U形的锆合金刚凸结构件,发现冲制后在刚凸的边缘发生开裂,破裂位置的应变路径为近平面应变路径。邓振鹏等[11]模拟了锆合金带材冲制过程,发现增大凸凹模间隙、减小摩擦系数,可有效降低带材冲制后的极限应变,利于成形。锆合金的各向异性使其在塑性变形过程中应变路径发生偏转,随着材料屈服表面指数的下降,成形过程中的应变路径从线性变为非线性,并向平面应变路径发生偏转[12]。此外还有学者[13-14]采用多工步冲制工艺,改变应变路径消除定位格架冲制开裂的问题。然而这些研究主要讨论冲制过程中的宏观应变路径,对应变路径与织构演变及微观变形机制的内在关系尚不明确。目前,针对锆合金微观变形机制及织构演化的研究多集中于简单加载条件(如单向拉伸和轧制)。其中,Deng等[15]通过单向拉伸实验结合粘塑性自洽(visco-plasticself-consistent,VPSC)模型解释了Zr-4合金的各向异性屈服行为主要源于不同方向加载时柱面滑移的开启量不同。Liu等[16]发现基面滑移和孪生开启量的差异导致了Zr-4合金板材单向拉伸时的各向异性硬化。Luan等[17,18]研究了Zr-1.0Sn-0.3Nb板材压缩和轧制过程中的微观组织及织构演变。Knezevic等[19]发现大应变变形时,Zr的典型轧制织构的形成依赖于基面滑移的开启。Cao等[20]研究了Zr-Nb-Mo合金在冷轧过程中的变形机制,结果表明锥面滑移是轧制到大变形量条件下协调厚度方向变形的主要滑移机制。冲制过程在不同位置的应变路径较复杂,针对这一复杂加载条件下的微观机理研究目前尚不多见。
本工作采用自研冲制模具开展Zr-4合金带材的冲制实验,采用电子背散射衍射(EBSD)方法测试了冲制深度为1.16mm的冲制元件在凹模圆角、斜壁和凸模圆角3个位置的织构变化,并利用晶内取向差转轴法(IGMA)明确了不同位置开启的变形机制差异。通过宏观有限元(FEM)-粘塑性自洽(VPSC)间接耦合模型,分析应变路径对冲制过程中的织构演变及变形机理的影响,揭示影响冲制开裂的关键机制,这对深入理解锆合金带材冲制过程的织构形成机理、降低冲制开裂趋势具有重要的理论意义和工程应用价值。
1、实验方法
1.1实验材料
本实验采用某公司生产的0.457mm厚退火态Zr-4合金带材,主要化学成分为Zr-1.2Sn-0.2Fe-0.1Cr(质量分数,%)。将带材切割成小样品,尺寸为30mm20mm0.457mm(RD-TD-ND,其中RD代表带材的轧制方向,TD代表带材的宽度方向,ND代表带材的法向方向)。退火态Zr-4合金初始带材为无孪晶的再结晶等轴晶组织,晶粒尺寸约为5.0µm(图1a)。初始织构为基面的双峰织构,c轴与ND方向成约20倾斜,织构强度为4.0mud。一般用Kearns系数[21](Kearnsfactor)表征材料内部晶粒的取向分布状态,定义为极轴沿特定方向排列的晶粒的有效百分数,它代表了试样内部晶粒基轴沿不同方向分布的几率,由下式计算:

式中,F为Kearns系数,φ为晶粒的c轴与特定方向的夹角,Iφ为倾斜角度φ时的平均强度。初始带材的Kearns系数为Fr=0.084,Ft=0.188,Fn=0.728。其中,Fr、Ft和Fn分别表示带材沿轧向、宽向和法向的Kearns系数。
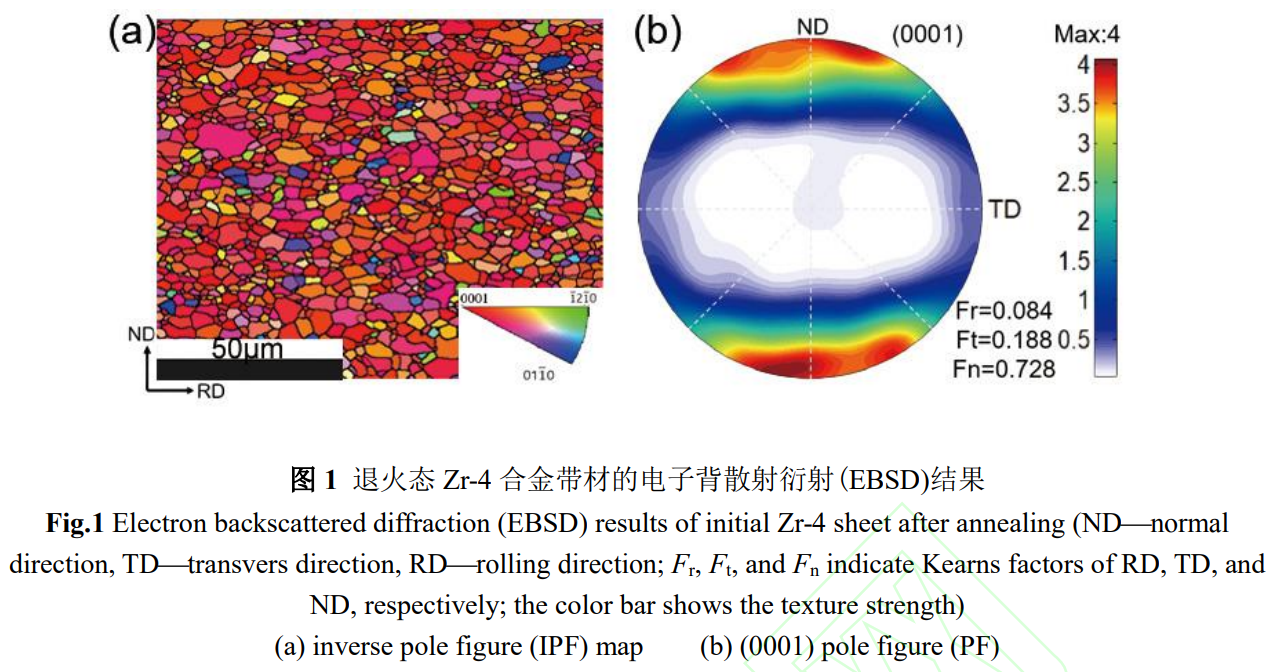
1.2Zr-4合金冲制实验
图2所示为冲制实验模具示意图及模具关键参数。将冲制模具(图2a)安装在冲压机床上,样品放置在凹模上进行冲制。冲制模具尺寸如图2b所示,冲头尺寸为长10.3mm,宽3.8mm,凹模为长12.1mm,宽5.4mm,深度1.62mm,冲头圆角半径Rp=0.15mm,凹模圆角半径Rd=0.6mm。进行冲制深度为1.16mm的冲制实验,分析冲制后样件在不同位置的织构变化。
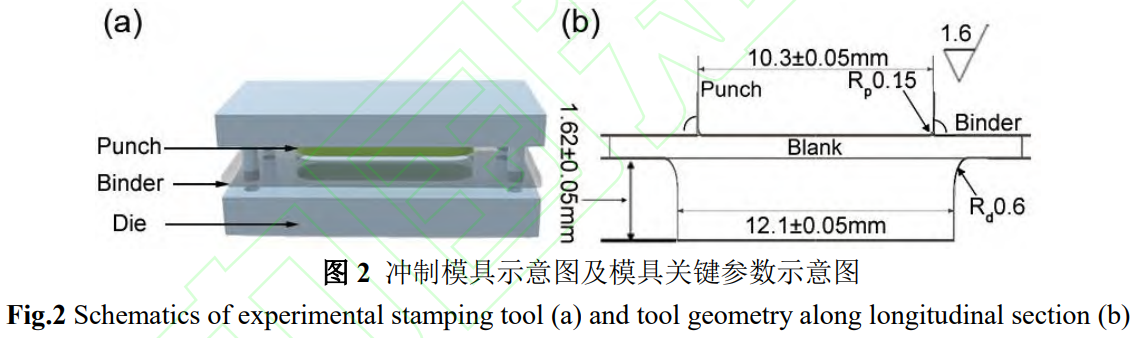
1.3冲制样件典型位置EBSD及成形深度测试
冲制后样件沿着轧制方向切开,在纵截面选取3个区域(A、B、C)进行EBSD观测,如图3所示。A、B、C分别位于凹模圆角区、斜壁区及凸模圆角区,x、y、z方向分别为带材的轧制方向、宽度方向和法线方向,图中红色区域为实验的观测面(RD-ND面)。EBSD样品采用机械抛光+电解抛光方法制备,电解抛光液中乙醇和高氯酸的体积比为9:1,电解温度-40℃,工作电压30V,电解时间3min。利用Mira3XMU场发射扫描电镜(SEM)对变形前后的样品进行EBSD观测,步长0.2μm,使用Aztec软件进行数据采集,实验数据通过HKLChannel5软件进行分析处理。
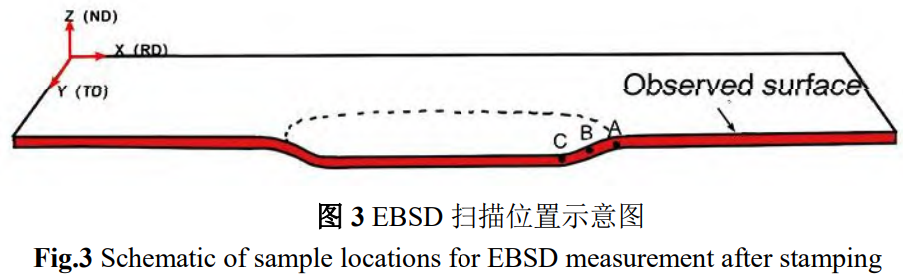
为有限元模拟提供准确的边界条件,选用白光干涉实验测量冲制样件的深度。白光干涉仪是以白光干涉技术为原理,对器件表面进行非接触式扫描并建立表面3D图像,从而实现器件表面形貌测量的光学检测仪器[22]。本实验采用MicroXAM3D白光干涉仪,通过MicroXAM操作软件和Qport数据分析软件进行结果处理。
1.4Zr-4合金冲制有限元模型建立
根据实际工件尺寸建立有限元模型,模型包括凸模、压边圈、带材和凹模,如图4所示。带材单元采用Belytschko-Tsay壳单元网格,网格尺寸为0.18mm,共计96941个单元。模具定义为刚体,冲压过程分为压边阶段与成形阶段。压边阶段设置压边圈的速率为150mm/s,下行直至将板料压到凹模上为止;成形阶段为了与实际生产的成形过程保持一致,设置凸模的速率为150mm/s,为了保证压边圈对板料的压边作用,设置压边圈的压力为3kN。模型中接触类型设置为contact_forming_one_way_surface_to_surface,带材与模具之间的摩擦系数均设置为μ=0.125。
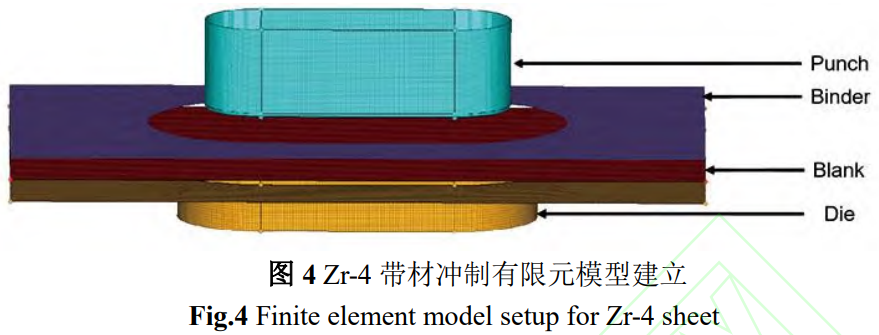
Zr-4合金带材的屈服模型选用Barlat89屈服准则(36*MAT_3-PARAMETER_BARLAT)。之前的研究工作[16]已经测试了Zr-4合金带材的各向异性,因而采用Zr-4合金带材的不同加载方向的力学曲线作为此模型的输入。屈服强度、抗拉强度、n值和r值如表1[16]所示。其中,n为应变硬化指数(strainhardeningexponent),r为各向异性系数(Lankfordcoefficient)。当加载方向从RD转变到TD时,屈服强度从406.98MPa增加到432.09MPa,抗拉强度从564.55MPa降低到525.62MPa。沿RD方向的n值最大为0.107,r值最小为4.74。TD方向的硬化能力最差,n值最小为0.072。冲制过程的有限元模拟通过控制凸模移动的位移来完成。
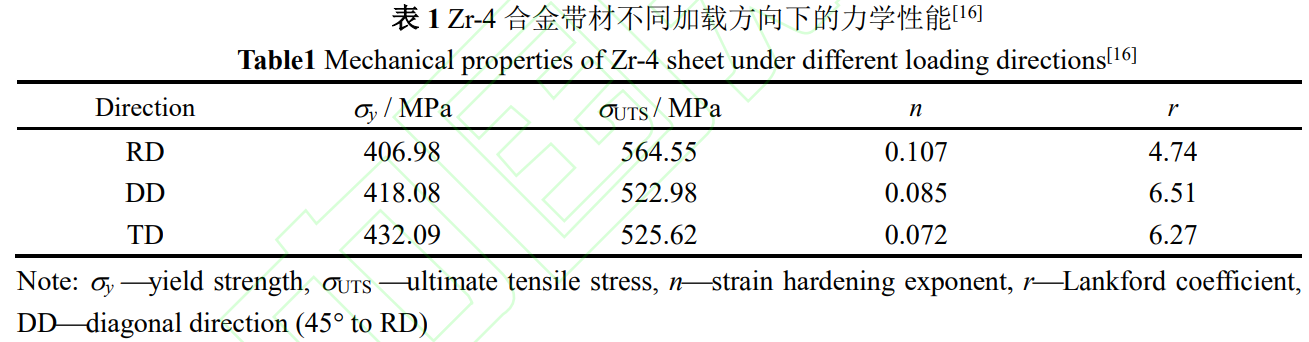
1.5Zr-4合金晶体塑性模型建立α-Zr中最优先开启的滑移系为柱面滑移。Akhtar等[23,24]认为,柱面滑移的临界剪切应力相对其他滑移系最小,这是柱面滑移系主导变形的最重要的原因。此外,基面滑移、锥面滑移及{101̅2}<1̅011>拉伸孪生是协调变形而开启的变形机制。因此在VPSC模型中选用上述4种变形机制,通过拟合不同单向加载方向的真实应力-应变曲线,对比拉伸后的实验织构与预测织构,确定适合Zr-4合金单向拉伸条件下的VPSC模型硬化参数,结果如表2所示[16]。该组模型参数可很好地表征各向异性的力学行为,预测的变形机制开启准确,因而本工作中也选用此组模型参数来预测冲制过程的织构演变和变形机制。
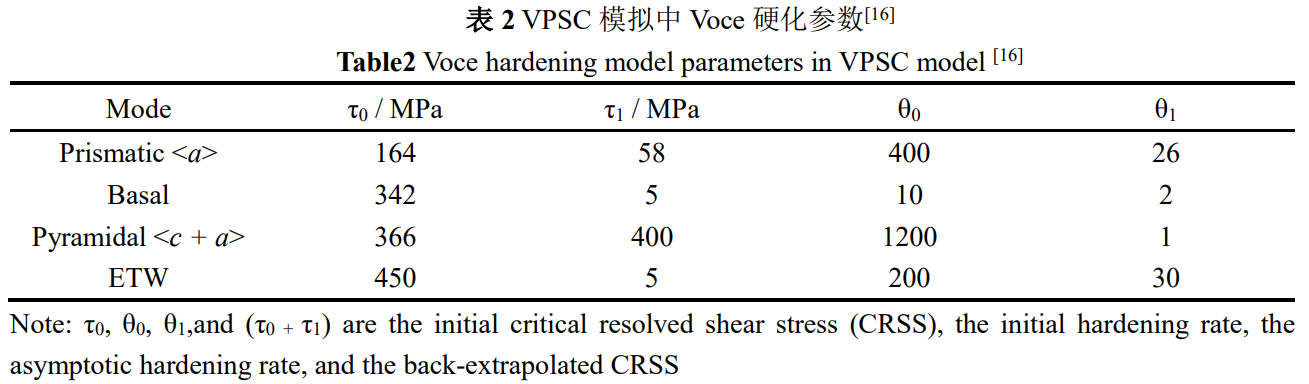
2、实验与模拟结果
2.1冲制实验结果
对Zr-4合金带材进行冲制实验,控制冲头位移1.16mm,图5a所示为冲制样件。冲制后在凸模圆角位置发生开裂,表面产生了明显的裂纹。为了准确测量冲制样件的深度,为有限元模拟提供准确的边界条件,进行了白光干涉实验,实验结果如图5b所示,沿纵截面3个位置A1~A3的深度分别为1.167、1.127和1.147mm,沿横截面3个位置B1~B3的深度分别为1.177、1.157和1.177mm,取6个位置的平均值,经计算所对应的成形深度为1.159mm。
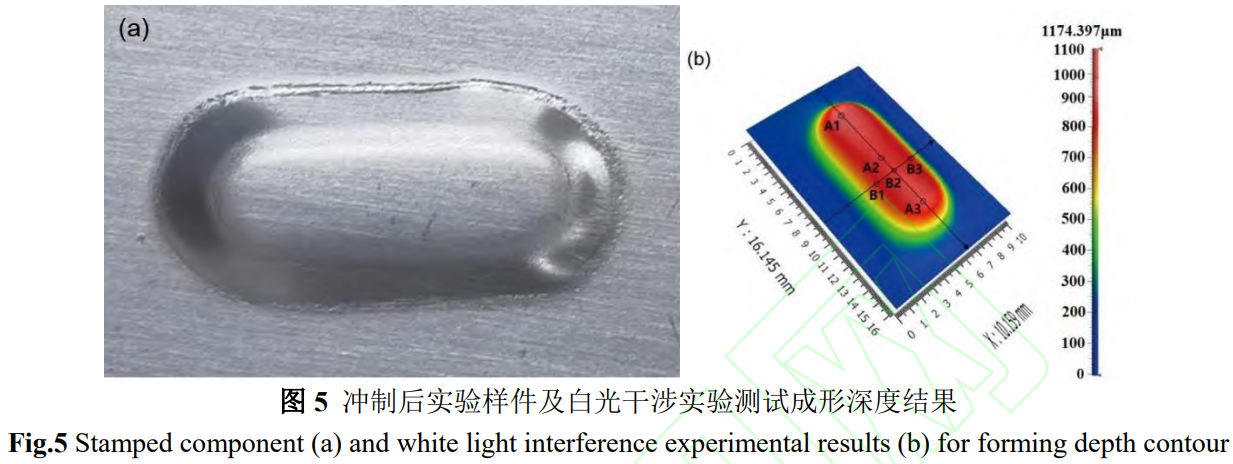
2.2Zr-4合金冲制后组织和织构的变化
图6为冲压后3个位置(A:凹模圆角;B:斜壁;C:凸模圆角)的EBSD结果。图6a为凹模圆角处的晶粒取向图,晶粒沿着冲制后的伸长方向被拉长,晶粒取向以<0001>//ND方向为主(红色晶粒),晶内出现少量其他颜色(蓝色和绿色)透镜状的新取向。经过图6d孪晶界标定结果可知,孪晶为{101̅2}(1̅011)拉伸孪晶(ETW),结合ImageJ软件测量得ETW相对面积分数为1.896%。相应地,由于ETW的产生,板材的初始织构发生偏转,形成了在RD方向上的强度集中,如图6g所示。Fr由于孪晶的生成从初始的0.084增加到了0.088。
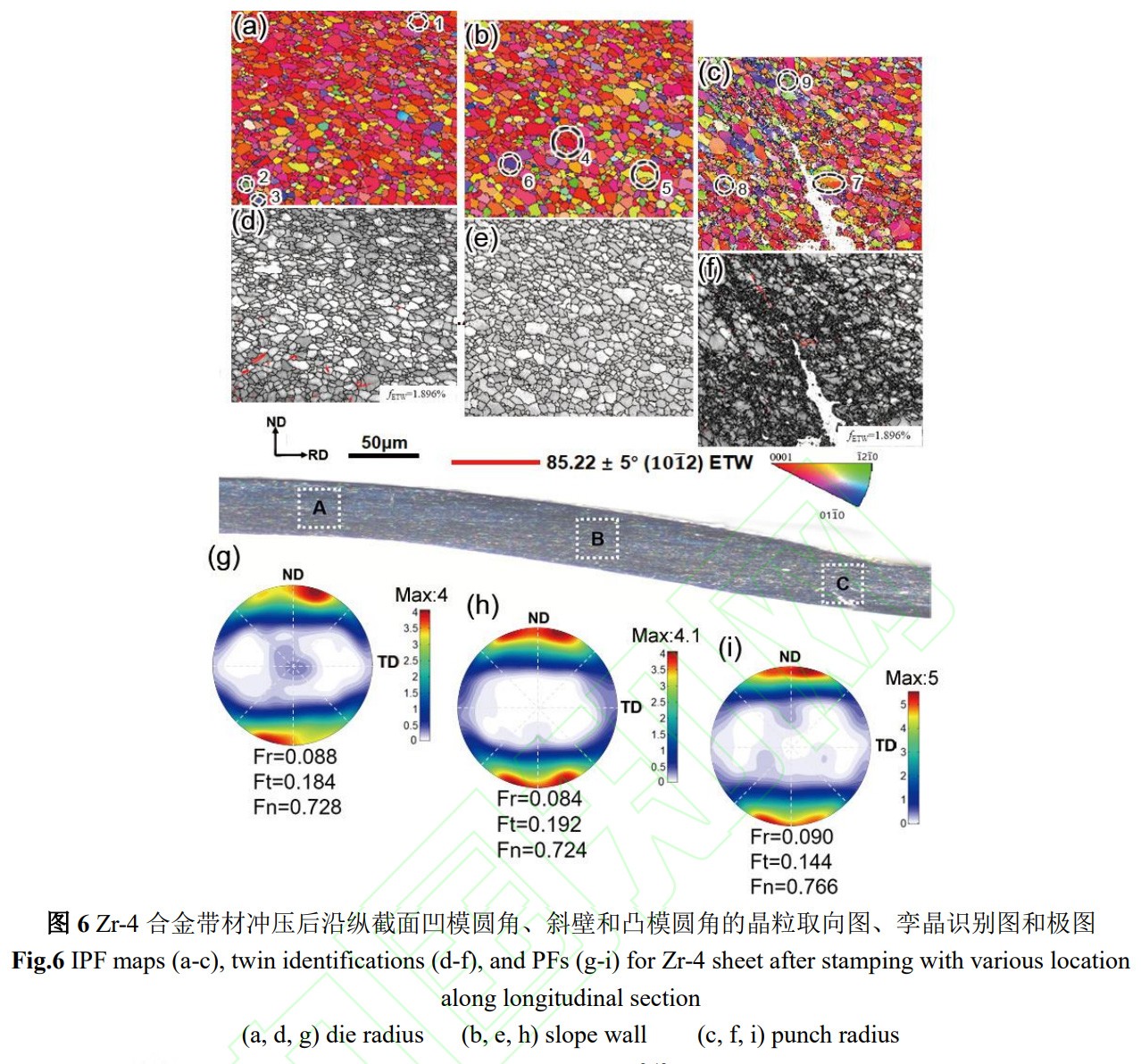
斜壁段的晶粒取向图如图6b所示,晶粒被拉长,晶粒取向以<0001>//ND方向为主(红色晶粒),但相对于初始织构,蓝色和绿色取向的晶粒分数稍微增加。从图6e中看出,斜壁段没有孪晶生成。织构类型仍保持双峰织构,Ft由0.188增加到了0.191,Fn由0.730降低到0.726。晶粒c轴从ND向TD略微倾转,但几乎与初始织构一致。
图6c是凸模圆角破裂位置的晶粒取向图,可以看出晶粒在冲制破裂位置处发生明显的碎化,内部出现了较多的小角度晶界。晶粒取向仍以<0001>//ND方向为主(红色晶粒),并能观察到有少量孪晶生成,经标定,仍为{101̅2}(1̅011)拉伸孪晶,孪晶分数小于凹模圆角处,约为0.689%(图6f)。图6i所示基面织构显著增强,发生了更为明显的向法向的集中,Fn明显增加,从0.730增加到0.766;Ft发生明显降低,从0.188降低到0.151。表明变形晶粒的c轴从TD向ND发生偏转。
2.3有限元模拟结果
图7所示为冲制后的Zr-4样件沿纵截面的实际测量厚度与模拟厚度的对比。图7a所示为有限元预测的壁厚分布云图,壁厚最小的位置与实际破裂位置一致,均位于凸模圆角底部。随着位置由凹模圆角变化到斜壁,壁厚呈先降低再升高的趋势,减薄主要发生在近凹模圆角位置。随着斜壁处到凸模圆角处,壁厚一直减小。为了更直观的对比纵截面方向的厚度分布情况,沿纵截面选取了10个点测量厚度,10个点的具体位置与板材厚度变化的数值模拟对比如图7b所示。结果表明,在凸模圆角处厚度减薄最明显,减薄最大的位置实测厚度为0.406mm,预测厚度为0.410mm。凹模圆角的厚度为0.445mm,数值模拟厚度0.449mm,数值模拟结果与实验测量结果吻合得较好,也验证了采用的本构模型的准确性。Zr-4合金带材在冲制变形后,凸模圆角处应变大,造成了应力集中,使得减薄严重,造成了冲制破裂。
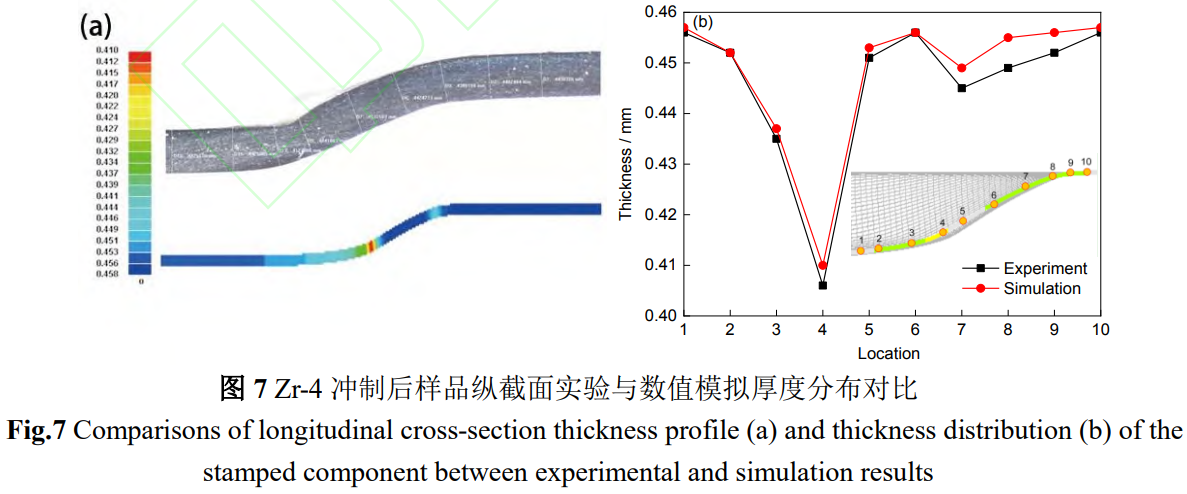
图8所示为选取不同位置处有限单元的正应变分量演化及应变状态。图8a中,随着材料流入模腔内,凸模圆角的变形应变沿着带材轧制方向与沿厚度方向的应变大小相等,方向相反,宽度方向应变分量εyy近似为0,正应变εxx=0.15和εzz=-0.15,其中,εxx、εyy、εzz分别为沿着RD、TD、ND方向的正应变。凹模圆角位置处的受力状态如图8b所示,εxx0,εyy<0、εzz<0,最后时刻沿RD的正应变约0.09(图8a),说明凹模圆角位置沿轧制方向伸长,宽度方向和厚度方向收缩。斜壁段的应变状态与凹模圆角相似,轧制方向应变分量为正,宽度方向和厚度方向为负,且由于变形量非常小,应变分量值也较小。
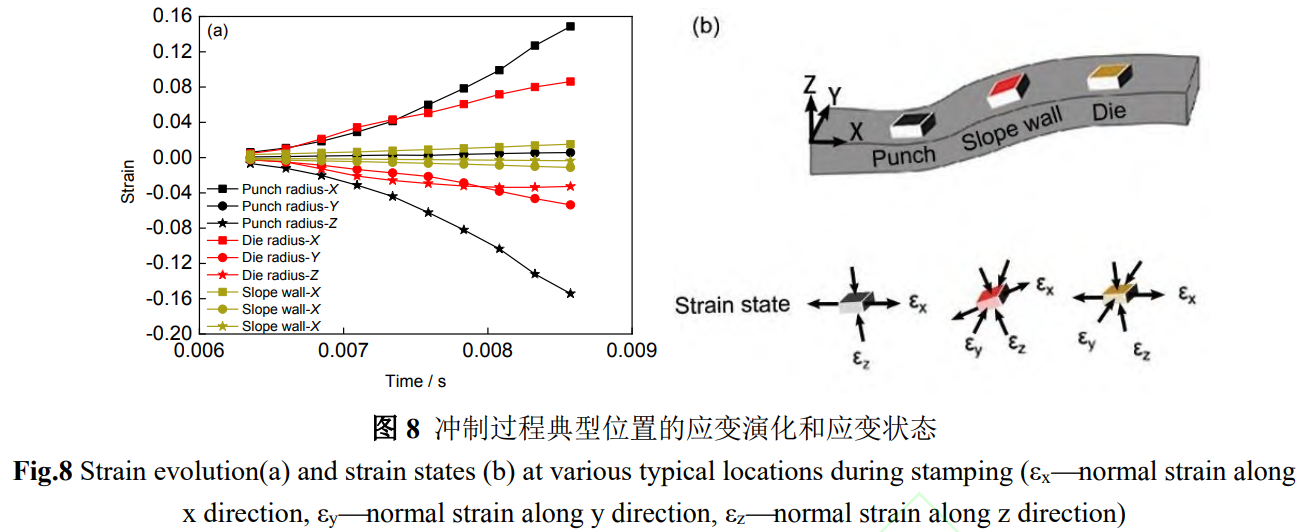
在成形过程中,典型位置A、B和C的应变路径及3个位置的主应变分布云图如图9所示。实际样件开裂位置(凸模圆角C)的应变路径为近平面应变,最大主应变高于A和B位置,说明变形后减薄最严重的区域发生的应变路径为平面应变。斜壁段B位置的应变路径为单向拉伸,主应变1为正,次应变2为负。凹模圆角A位置的应变路径为单向拉伸路径,最大主应变约为0.1,相较于斜壁,应变更大,路径更偏向于平面应变。综上,冲制样件的凸模圆角位置的受力状态为平面应变状态,路径为平面应变路径,应变值最大,极易超过成形极限曲线的平面应变特征点(FLD0),进而发生样件的冲制开裂。
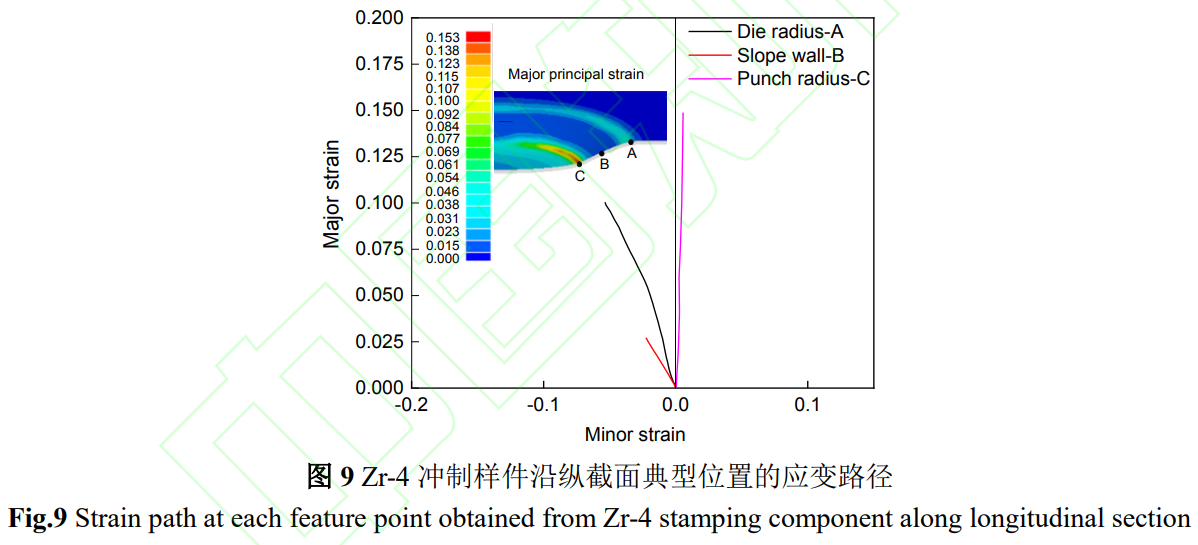
3、分析讨论
3.1应变路径对冲制过程变形机制的影响(IGMA分析)
IGMA是确定材料变形过程中滑移系开启的一种方法[25],基于IGMA分析可以获得Zr-4合金冲制过程中变形机制的开启情况。从图6中选取3个典型位置(凹模圆角、斜壁和凸模圆角),每个位置选取3种典型取向,共9个晶粒分别标记为G1~G9(红色-G1/G4/G7;绿色-G2/G5/G8;蓝色-G3/G6/G9),然后对其进行IGMA分布特征的分析,如图10所示。其中,凹模圆角中红色晶粒G1取向为近基极取向,IGMA分布的旋转轴主要集中在<0001>轴,说明其以柱面滑移为主;随着c轴向TD方向偏转,以绿色(G2)和蓝色(G3)为代表的非基极取向晶粒的IGMA强度极点出现在了<138̅5̅3>轴和<61̅5̅3>轴附近,说明此时在单向拉伸的应变路径条件下,Zr-4合金变形以柱面滑移系为主,锥面滑移系为辅,同时也发现存在极点集中在<1̅21̅0>,表明少量基面滑移会开启,并结合前面少量的孪晶生成,可知协调厚度方向变形的变形机制主要是锥面滑移,基面滑移和孪生次之。与凹模圆角类似,当斜壁位置处晶粒的c轴与法线方向平行时(G4),其IGMA分布的旋转轴主要集中在<0001>轴,而对于c轴近似垂直于ND的TD取向晶粒(G5和G6),晶粒的IGMA分布特征落在内扇形上,说明仍是以柱面滑移主导,锥面滑移协调变形的机制。凸模圆角处的红色取向晶粒(G7)的IGMA强度极点分布出现了发散的迹象,不只在<0001>轴集中,同时向扇形边缘处发生扩散,G8和G9晶粒的IGMA的强度极点也出现发散的迹象,并且主要弥散分布于扇形边缘处,沿着的分布强度逐渐升高,说明基面滑移开启被促进,柱面滑移的开启受到了抑制,而此位置主要开启基面滑移以协调厚度方向上的变形,与凹模圆角和斜壁不同。平面应变路径促进了基面滑移系的开启,而基面滑移的开启使得c轴从TD方向偏转到ND方向,逐渐从基面的双峰织构向基面发生织构集中,进而导致凸模圆角位置最终发生冲制开裂。
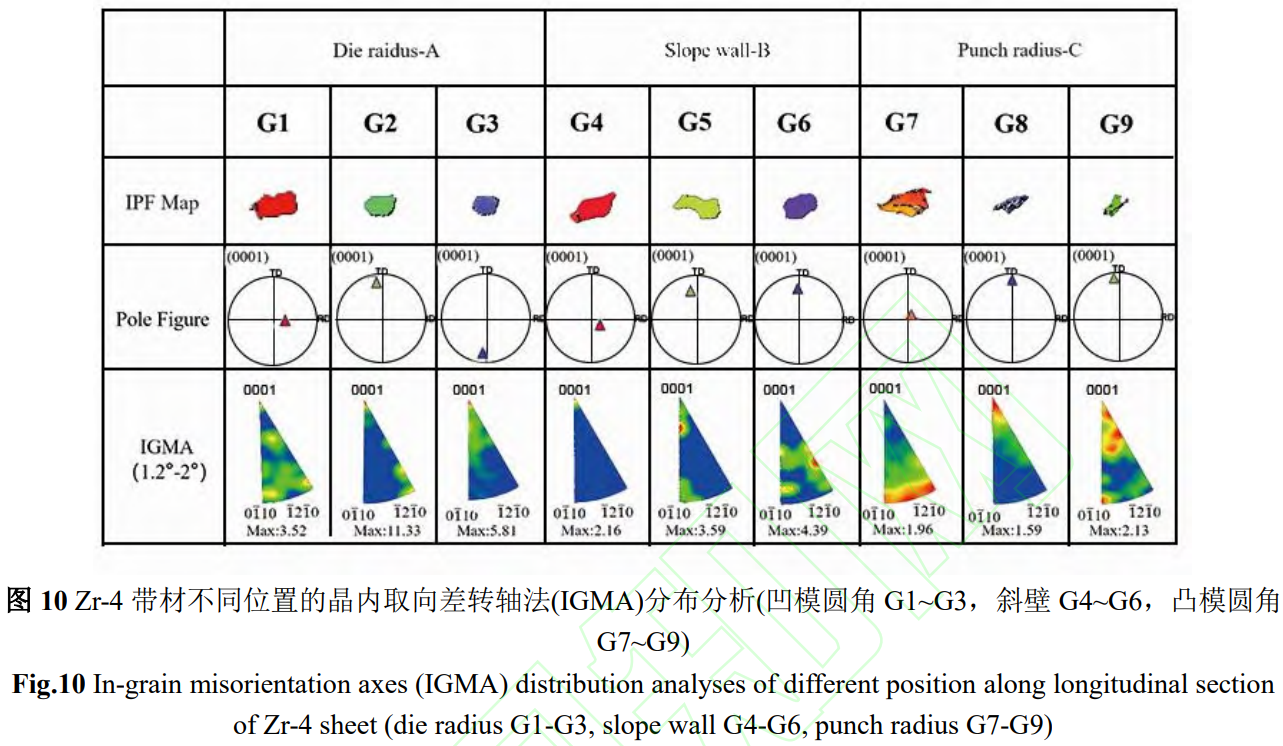
3.2基于VPSC预测冲制过程中变形机制
利用VPSC模型预测了冲制过程中织构的演变和滑移系开启的变化规律,选取图1所示的织构作为变形前的初始织构,采用有限元中提取的随时间变化的正应变结果作为变形边界条件。实验与VPSC预测的(0001)织构及Kearns系数结果对比如图11所示。VPSC模拟结果很好地捕获了实验结果中的织构特征,验证了模型的准确性。如图11a和b所示,当位于凹模圆角时,织构发生了轻微的变化。其中,实验的孪晶产生量为1.896%,VPSC预测的孪晶激活分数为1.66%。无论是实验结果还是预测结果,织构的变化趋势相似,均是近基极取向的母晶产生孪晶,使Fr略微增大,产生了新的织构类型。斜壁位置预测的织构和实验织构均由于应变太小,没有发生明显的变化,变形后的织构保持了典型的轧制双峰织构(图11c和d)。与初始织构相比,凸模圆角位置Fn的实验值和VPSC预测值均增大,Ft降低,Fr略微增大。表明晶粒取向从TD向ND偏转,使得变形后织构发生了集中,进而造成了织构强度的增大。
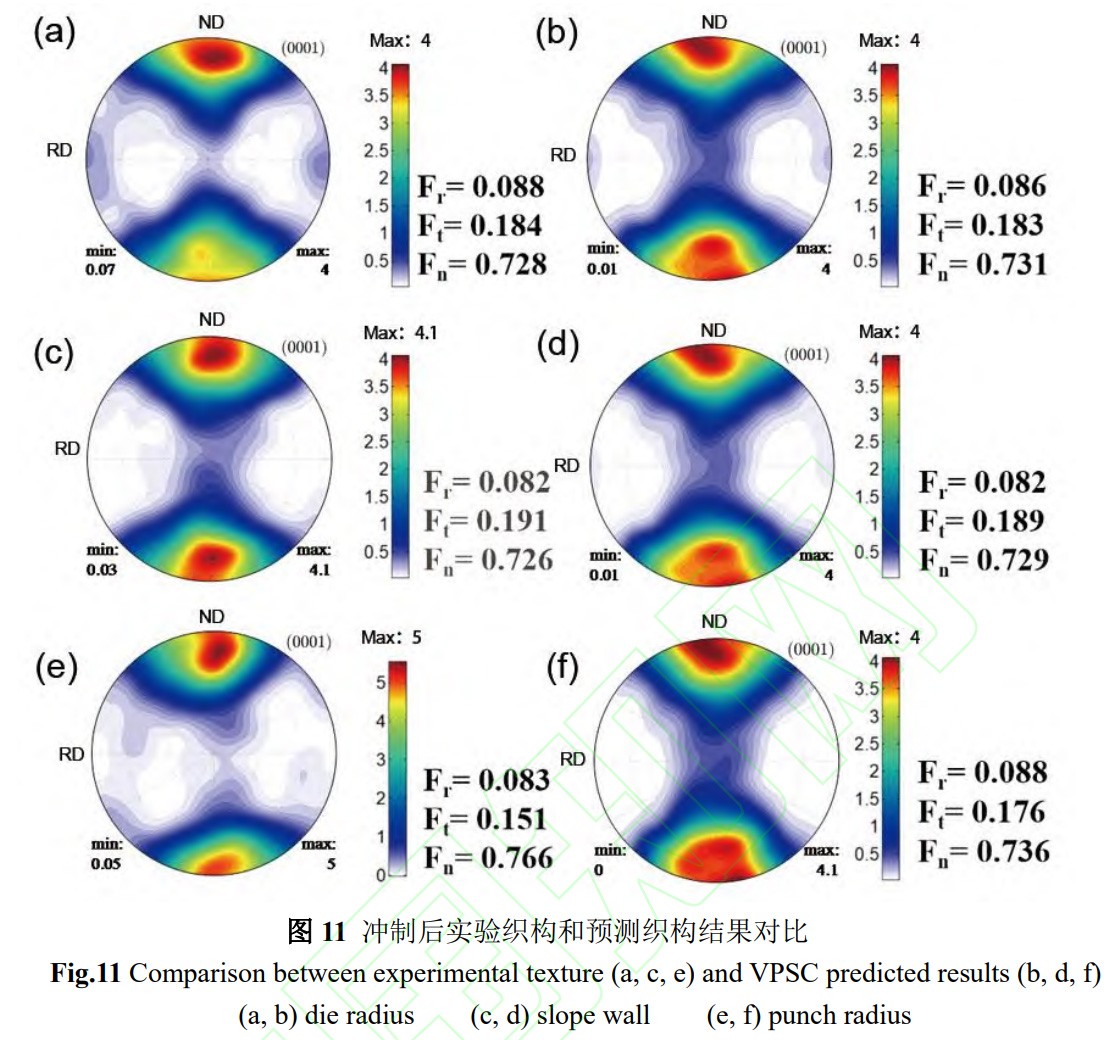
图12所示为冲制过程VPSC预测的变形机制开启情况。如图12a所示,凹模圆角位置的柱面滑移最容易开启,锥面滑移作为协调厚度方向上变形的主要辅助滑移系,这一结果与IGMA分析结果相同。随着应变的增大,柱面滑移和锥面滑移开启降低,基面滑移开启增大,但开启量不会超过锥面滑移。此外,预测的ETW开启量为1.66%,这与实验中统计的孪晶生成量吻合得很好。
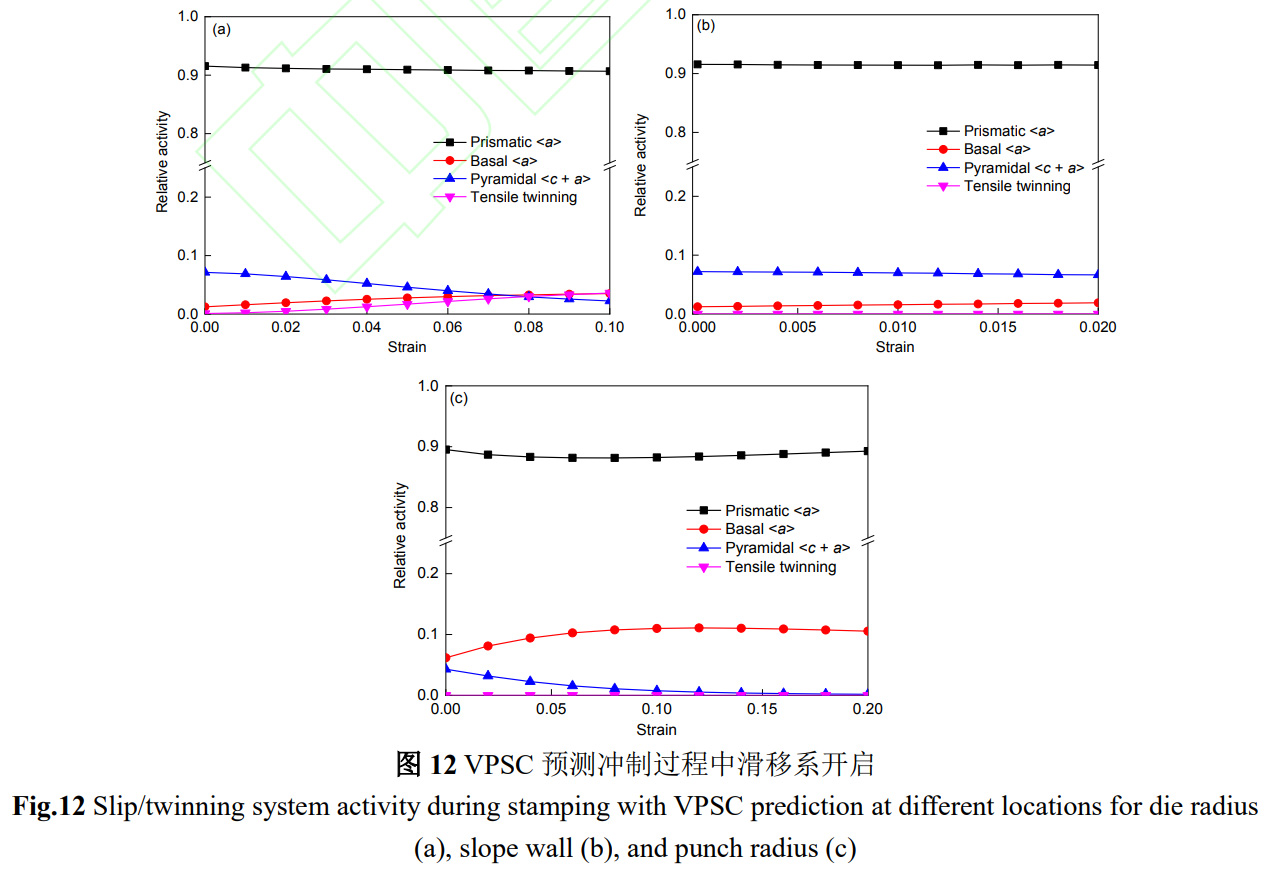
斜壁段的变形机制以柱面滑移为主,锥面滑移为辅(图12b)。通过对比可知,柱面滑移的相对开启量最高,由于锥面滑移在此变形条件下激活量更高,所以基面滑移几乎不开启,孪生也不开启。与单向拉伸变形的织构演变类似,在柱面滑移与锥面滑移配合开启的条件下,变形织构与初始织构相似,不会产生明显的织构变化。凸模圆角位置的Kearns系数Fr几乎没有变化,Ft减小,Fn增大,说明c轴从TD方向继续向ND方向偏转。通过VPSC对变形机制激活量的预测可知,受到平面应变路径的影响,柱面滑移受到抑制,低于凹模圆角和斜壁,基面滑移的开启量高于锥面滑移,成为了该路径下协调厚度变形的滑移系。随着冲制过程的进行,应变的增大,基面滑移系开启不断增加,锥面滑移系不断降低,只产生了微量的孪晶。说明基面滑移随着变形程度的增加成为了唯一协调厚度方向变形的滑移,其开启量的增大使得初始的双峰织构转为近基面织构,织构强度不断升高,当基面滑移的开启量达到临界值时,厚度方向协调变形困难,进而发生破裂,也就是说,凸模圆角处发生破裂是由于基面滑移系大量开启导致。
4、结论
(1)针对Zr-4合金带材(0.457mm)进行冲制实验,当凸模圆角R=0.15mm,Zr-4合金带材冲制变形深度为1.16mm时,带材发生破裂,破裂位置位于凸模圆角处。
(2)冲制后沿纵截面3个位置的织构实验结果表明,相较于初始织构,凹模圆角位置由于ETW产生了沿RD方向的新织构,使得Fr增大,Ft降低;斜壁位置的变形织构与初始织构相似;凸模圆角位置从双峰织构转为近基面织构,Fn增大,Fr增大,而Ft降低。
(3)采用FEM预测冲制变形时,斜壁和凹模圆角位置的应变路径为单向拉伸,凸模圆角位置为平面应变路径。
(4)在斜壁位置的单向拉伸应变路径,变形机制以柱面滑移开启为主,锥面滑移为辅,由于变形较小,织构没有发生明显的变化;凹模圆角位置处,变形机制仍然以柱面滑移主导,锥面滑移和ETW共同协调变形,使得织构产生了从ND向RD方向偏转的新织构类型。
(5)平面应变路径抑制了柱面滑移和锥面滑移的开启,促进了基面滑移协调变形,基面滑移的开启使织构从双峰织构转变为近基面织构。随着应变的增大,基面滑移成为了唯一协调厚度变形的滑移系,当其开启量达到临界时,厚度方向难以协调变形,冲制发生开裂。可见,基面滑移是影响冲制开裂的关键变形机制。
参考文献
[1] Han E H. Research trends on micro and nano-scale materials degradation in nuclear power plant [J]. Acta Metall. Sin., 2011, 47: 769
(韩恩厚. 核电站关键材料在微纳米尺度上的环境损伤行为研究——进展与趋势 [J]. 金属学报, 2011, 47: 769)
[2] Murty K L, Charit I. Texture development and anisotropic deformation of zircaloys [J]. Prog. Nucl. Energy, 2006, 48: 325
[3] Ren Q Y, Chen J, Zhao R R, et al. Mechanical performance of newly developed supporting structure of spacer grid [J]. At. Energy Sci. Technol., 2020, 54: 2411
(任全耀, 陈 杰, 赵瑞瑞等. 新型定位格架夹持结构的力学特性研究 [J]. 原子能科学技术, 2020, 54: 2411)
[4] Akhtar A, Teghtsoonian A. Plastic deformation of zirconium single crystals [J]. Acta Metall., 1971, 19: 655
[5] McCabe R J, Cerreta E K, Misra A, et al. Effects of texture, temperature and strain on the deformation modes of zirconium [J]. Philos. Mag., 2006, 86A: 3595
[6] Akhtar A. Prismatic slip in zirconium single crystals at elevated temperatures [J]. Metall. Trans., 1975, 6A: 1217
[7] Li Y, Po G, Cui Y N, et al. Prismatic-to-basal plastic slip transition in zirconium [J]. Acta Mater., 2023, 242: 118451
[8] Knezevic M, Zecevic M, Beyerlein I J, et al. Strain rate and temperature effects on the selection of primary and secondary slip and twinning systems in HCP Zr [J]. Acta Mater., 2015, 88: 55
[9] McCabe R J, Proust G, Cerreta E K, et al. Quantitative analysis of deformation twinning in zirconium [J]. Int. J. Plast., 2009, 25: 454
[10] Lei C Y, Mao J Z, Zhou D W, et al. Effects of annealing treatments on forming performance of zirconium alloys [J]. Trans. Nonferrous Met. Soc. China, 2022, 32: 2908
[11] Deng Z P, Zhou D W, Jiang P S, et al. Optimization on stamping process parameters for zirconium alloy sheet strip based on orthogonal experiment [J]. Forg. Stamping Technol., 2019, 44(9): 12
(邓振鹏, 周惦武, 蒋朋松等. 基于正交试验的锆合金薄板带材冲压工艺参数优化 [J]. 锻压技术, 2019, 44(9): 12)
[12] Lei C Y, Mao J Z, Zhang X M, et al. A comparison study of the yield surface exponent of the Barlat yield function on the forming limit curve prediction of zirconium alloys with M-K method [J]. Int. J. Mater. Form., 2021, 14: 467
[13] Kim M, Bang S, Lee H, et al. Enhancement of dimple formability in sheet metals by 2-step forming [J]. Mater. Des. (1980-2015), 2014, 54: 121
[14] Marimuthu K P, Choi W, Kim N, et al. Numerical investigations on the effect of pit on two-step dimple forming of atomic fuel spacer grid [J]. Int. J. Adv. Manuf. Technol., 2018, 94: 293
[15] Deng S Y, Song H W, Liu H, et al. Effect of uniaxial loading direction on mechanical responses and texture evolution in cold pilgered Zircaloy-4 tube: experiments and modeling [J]. Int. J. Solids Struct., 2021, 213: 63
[16] Liu H, Deng S Y, Chen S F, et al. Correlation of the anisotropic hardening behavior and texture features of cold rolled Zr-4 sheet under uniaxial tension [J]. J. Mater. Sci. Technol., 2022, 119: 111
[17] Luan B F, Gao S S, Chai L J, et al. Compression deformation behavior of Zr–1Sn–0.3Nb alloy with different initial orientations at 650 °C [J]. Mater. Des. (1980-2015), 2013, 52: 1065
[18] Chen J W, Luan B F, Chai L J, et al. Heterogeneous microstructure and texture evolution during fabrication of Zr-Sn-Nb zirconium alloy sheets [J]. Acta Metall. Sin., 2012, 48: 393
(陈建伟, 栾佰峰, 柴林江等. Zr-Sn-Nb 新型锆合金板材加工过程中不均匀组织与织构演变 [J]. 金属学报, 2012, 48: 393)
[19] Knezevic M, Beyerlein I J, Nizolek T, et al. Anomalous basal slip activity in zirconium under high-strain deformation [J]. Mater. Res. Lett., 2013, 1: 133
[20] Cao Y C, Chen D, Xia L, et al. Effects of primary α grains on rolling reductions and deformation modes in Zr alloys: Experiments and modeling [J]. Mech. Mater., 2024, 19: 104957
[21] Kearns J J. On the relationship among ‘f’ texture factors for the principal planes of zirconium, hafnium and titanium alloys [J]. J. Nucl. Mater., 2001, 299: 171
[22] Su R, Liu J Y, Qiao X Y, et al. Advances in scanning white light interferometry for surface topography measurement [J]. Laser Optoelectron. Prog., 2023, 60: 0312005
(苏 榕, 刘嘉宇, 乔潇悦等. 用于表面形貌测量的扫描白光干涉技术进展 [J]. 激光与光电子学进展, 2023, 60: 0312005)
[23] Akhtar A. Compression of zirconium single crystals parallel to the c- axis [J]. J. Nucl. Mater., 1973, 47: 79
[24] Akhtar A. Basal slip in zirconium [J]. Acta Metall., 1973, 21: 1
[25] Chun Y B, Battaini M, Davies C H J, et al. Distribution characteristics of in-grain misorientation axes in cold-rolled commercially pure titanium and their correlation with active slip modes [J]. Metall. Mater. Trans., 2010, 41A: 3473
相关链接