随着世界工业化进程的加快,工业生产规模越来越大,对能源的消耗也与日俱增。为有效应对过度能源消耗导致的众多全球化问题,《中国制造 2025》以及十四五“双碳”目标提出持续推进制造业转型和能源结构调整并争取早日实现。在众多工业生产模式中,锻造生产一直以高能耗著称,其能耗约占机械制造行业总能耗的 25%[1]。因此,我国作为世界第一制造大国,锻造行业节能降耗工作的开展迫在眉睫,其不仅符合国家节约能源的发展方针,还直接影响国家的经济利益。
飞机和航空发动机结构的主要承力部件都采用铝合金及高强钢的模锻件,如飞机机体承力框、主梁、起落架,发动机的涡轮盘、涡轮轴、叶片等,其制造水平对飞机所能达到的最高性能水平、可靠性、寿命和技术经济效益有重大影响[2-4]。因此,航空航天领域对大型金属锻件的质量要求极高,但目前企业在达到锻件质量标准的同时,也存在能耗管控粗放的问题。而现有的研究大多数都着眼于通过调整生产过程中的工艺参数或工艺方法来实现对铝合金等金属大型锻件质量的控制。Mao 等[5]提出了一种控制环三维机械性能的新方法来调控 2219 铝合金大规格锻环内部 Al2Cu 粗大第二相(CSPPs)严重偏析和力学性能不均匀的问题;王富强等[6]基于 DEFORM 数值模拟软件,对某型机 7B04 铝合金接头锻造过程进行研究,采用优化工艺试制的锻件的抗拉强度、屈服强度有明显提升,均满足产品性能指标;Xu 等[7]提出了箱形锻件等温反挤压过程中的预成形件设计方法,通过有限元模拟揭示了等厚坯料金属流动规律,模拟结果成功地预测了基体锻件底部折叠和盖件锻件侧壁填充不足的缺陷;Zhao 等[8]改进了传统的锻造工艺:预热、热锻、固溶热处理(SHT)和人工时效,将 SHT 和热锻集成到一个操作中,提出新型固溶锻造一体化工艺,在工业化条件下成功制造了 6082 铝合金锻件;Zhao 等[9]研究了 300M 钢在大应变下的变形行为,模拟了大型锻件的锻造过程,发现流变应力的变化受变形参数和加工硬化与动态软化相互作用的影响,以此提出了一种新的本构模型来预测不同变形参数下的流变应力。
虽然有少部分文献提及能源管控的重要性,但其研究均在起步阶段,且没有形成连续完整的体系,故本文就航空航天大型铝合金等金属锻件的缺陷、锻件质量的检测方法进行归纳总结,提出一些针对锻造生产企业能耗检测方法应用的思考与探索,有助于改善航空航天锻造生产制造领域能耗管控粗放的行业现状,在锻造行业高质低耗生产转型发展过程中具有一定的指导意义。
1 、大型锻件缺陷
铝合金、高强钢等高强度金属是锻造用的主要原材料,其形式大致为轧材、挤材和锻坯,是由铸锭分别经过轧制、挤压及锻造加工而成的半成品。在一般情况下,铸锭本身存在表面缺陷和内部缺陷,会造成锻件在后续工序中含有缺陷,影响锻件的性能[10-11]。锻造成形过程中工艺和操作不当,同样会引起锻件出现缺陷,甚至报废。下面按照锻件生产过程说明一些主要缺陷的特征、产生原因及可能引起的不良后果。
1.1 原材料产生的缺陷
尽管原材料在入厂前会由专业检查人员进行检查,但有些缺陷既分散又隐蔽,存在没有被发现的可能,原材料导致的锻件缺陷可以分为表面裂纹、折叠、非金属夹杂、铝合金氧化膜、白点、粗晶环等,其缺陷相应的主要特征、产生原因及影响如表 1 所示。
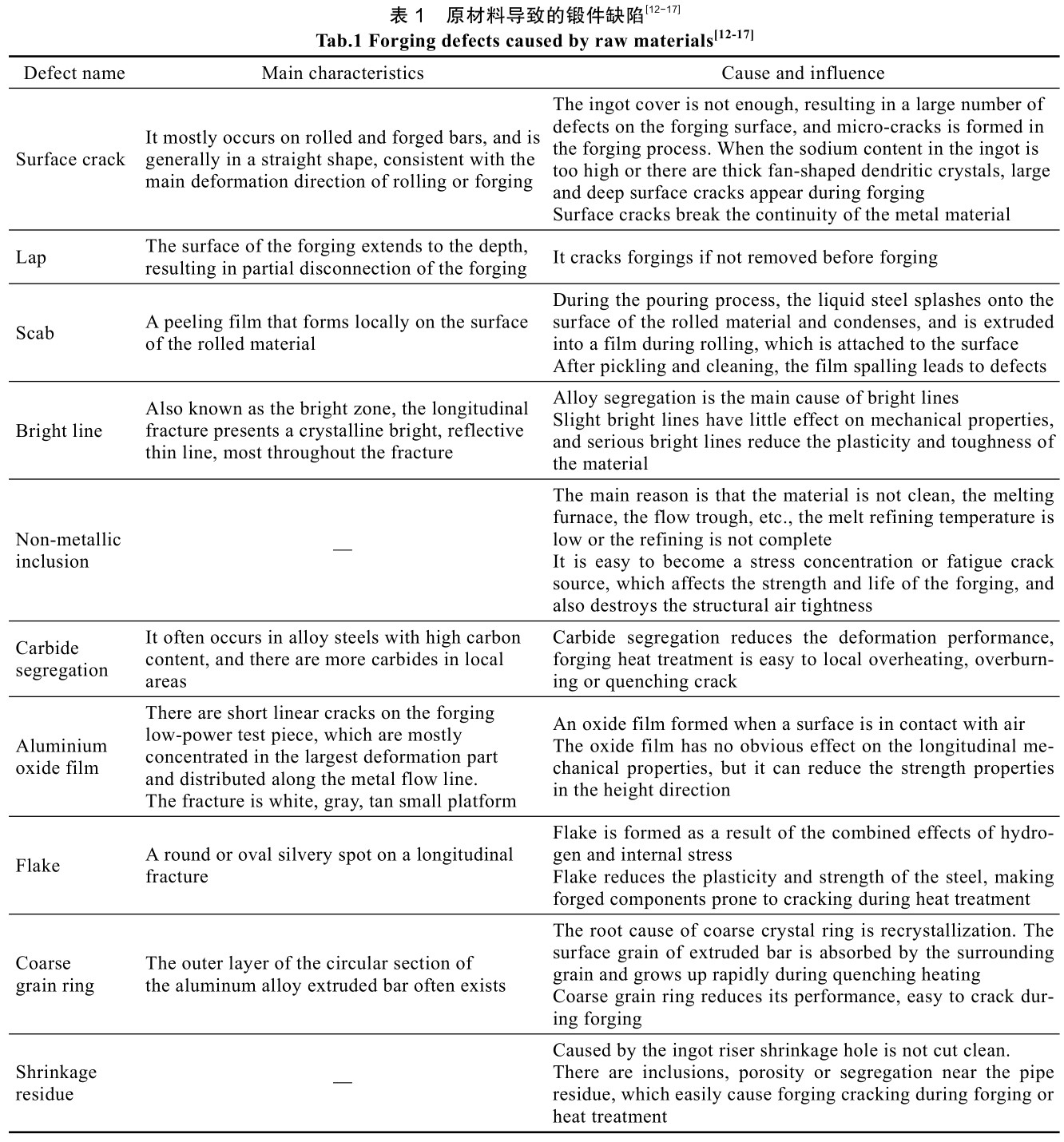
1.2 备料产生的缺陷
在备料过程中,机床内留有金属碎屑或操作不当通常会导致锻件产生较为严重的缺陷,产生的主要缺陷包括切斜、端面弯曲、端面凹陷、端面裂纹等,其缺陷相应的主要特征、产生原因及影响如表 2 所示。
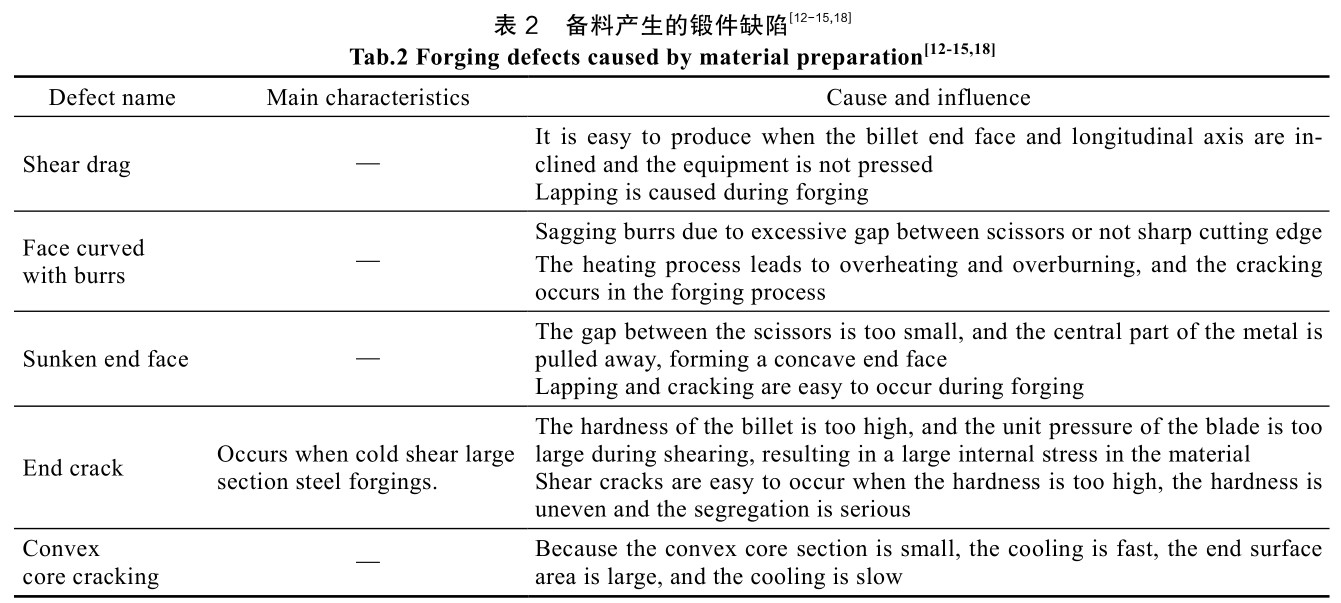
1.3 加热时产生的缺陷
铝合金等金属在加热时产生缺陷的原因大致可分为 3 种:1)介质影响使坯料外层组织化学状态变化而引起的缺陷,如氧化、脱碳、增碳、渗硫和渗铜等;2)由内部组织结构的异常变化引起的缺陷,如过热、过烧和未热透等;3)由于温度在坯料内部分布不均引起内应力(如温度应力、组织应力)过大而产生的缺陷,如开裂等[19]。下面介绍几种较为常见的缺陷,见表 3。
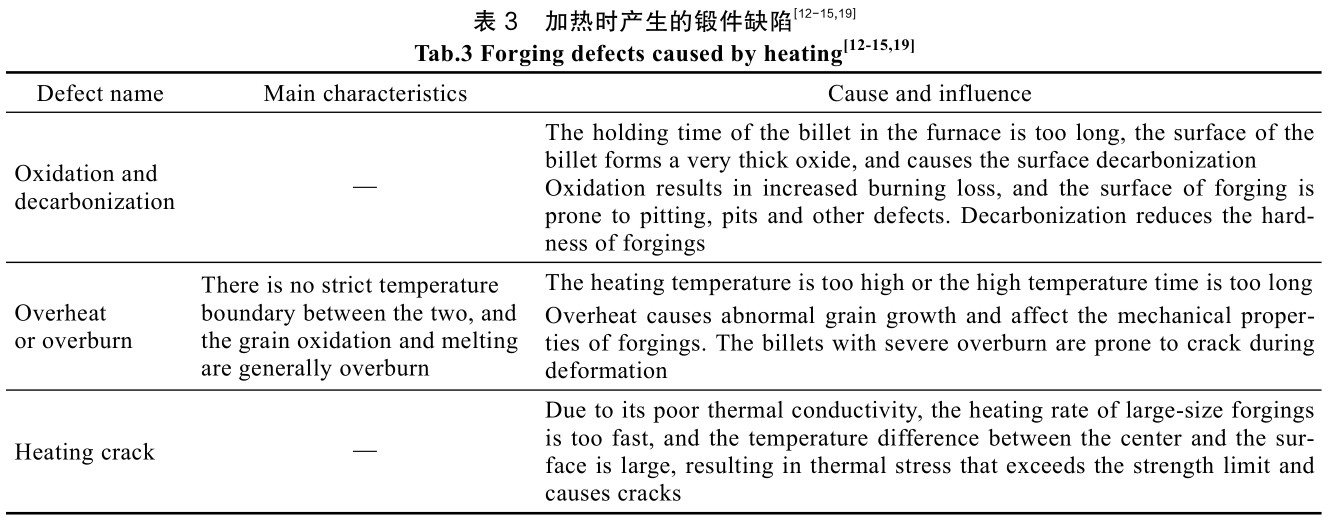
1.4 锻压过程中产生的缺陷
锻压过程中由于工艺不当会导致大量锻件缺陷的产生,如粗大晶粒、晶粒不均匀、冷硬现象、裂纹、折叠、穿流、欠压等,会导致锻件的使役性能降低。下面简要说明几种对锻件影响较大的缺陷,以及缺陷相应的主要特征、产生原因和影响,如表 4 所示。
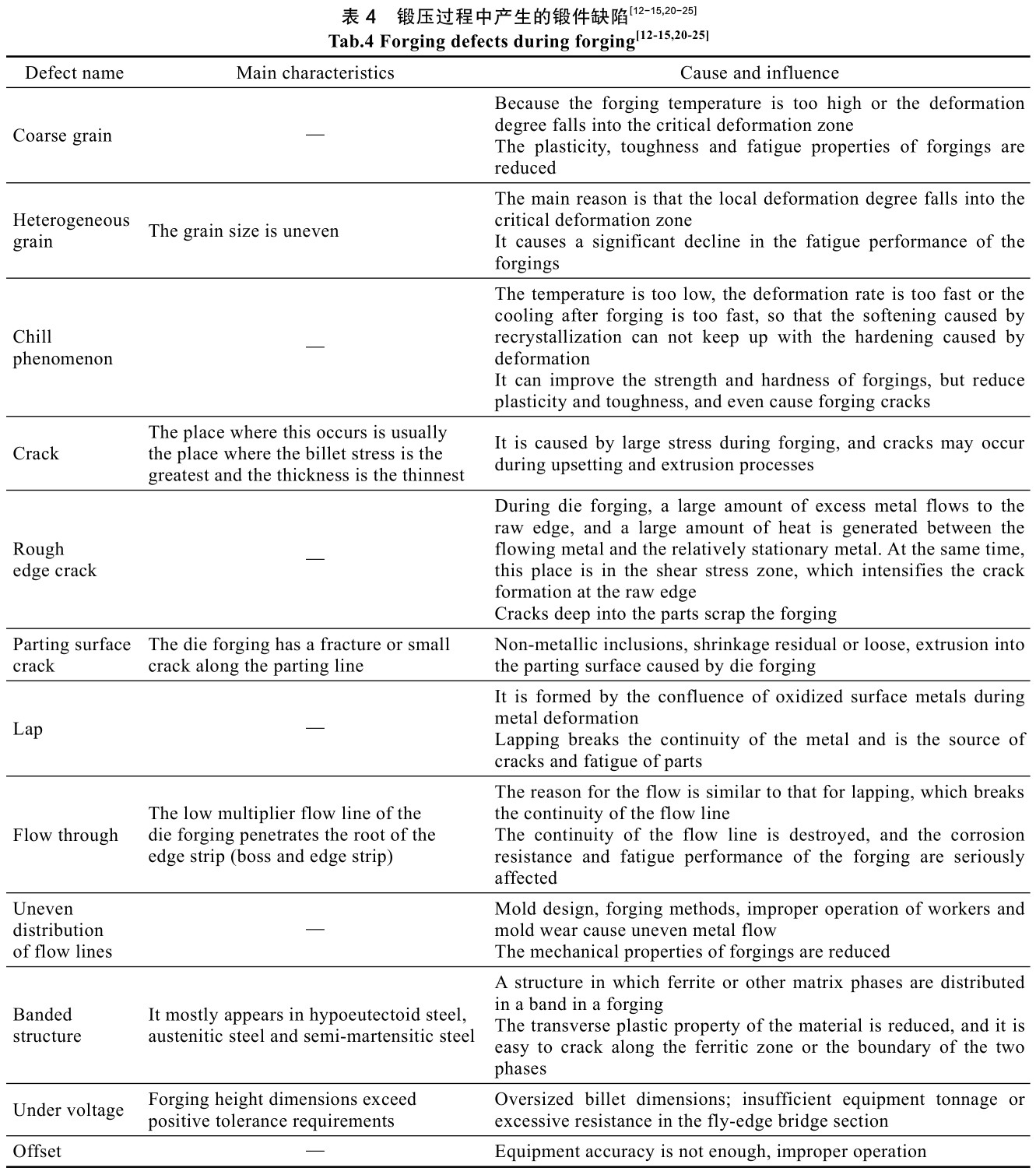
1.5 锻后热处理中产生的缺陷
锻后热处理在生产过程中通常起到细化晶粒、调整组织的作用,使锻件具有所需的使役性能,在这一过程中产生的缺陷主要可以归纳为冷却裂纹、网状碳化物、硬度过高或硬度不够,其缺陷相应的主要特征、产生原因及影响如表 5 所示。
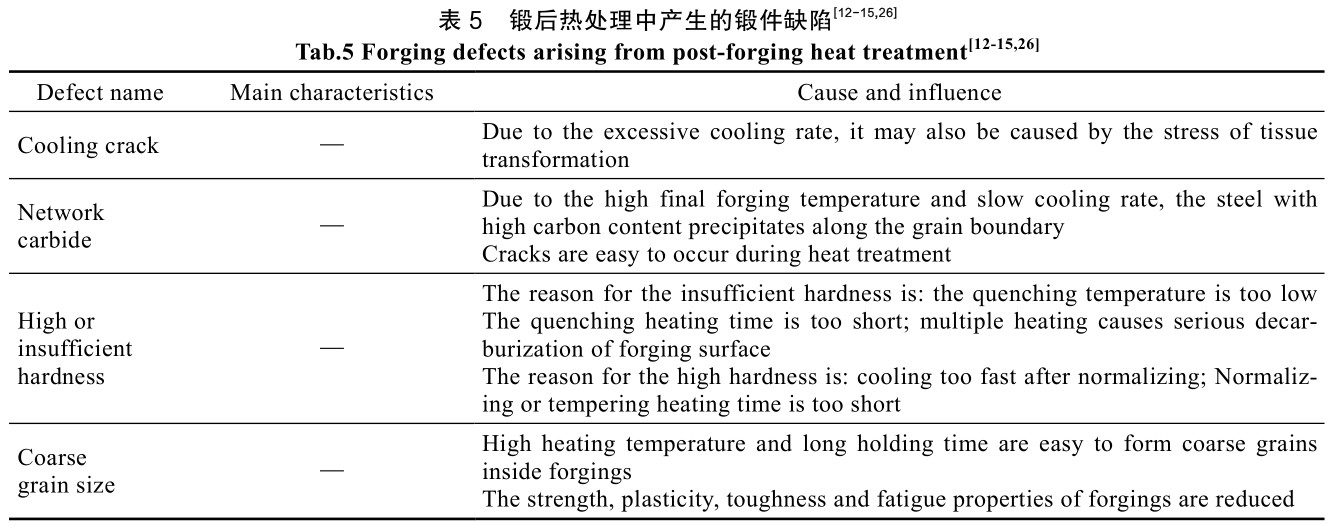
2、 质量检测
在大多数航空航天锻件产品制造企业中,锻件成形需要经过多个工序过程,因此,以铝合金为代表的大型锻件质量的影响因素是多方面的,应当进行多项质量检测评价以确保锻件质量达到出厂要求。锻件质量包括外观质量、力学性能、晶粒度/平均晶粒尺寸、断裂韧性、残余应力、抗腐蚀能力等方面,其中外观质量又包含锻件的几何尺寸、形状精度、表面质量 3个项目。
大型金属锻件的质量,必须满足 3 个方面的要求:一是消除材料内部的冶金缺陷,二是要获得大小均匀的细晶粒组织,三是实现锻件力学性能的定向定量分布[27]。
2.1 外观质量检测
在锻造过程中,需要对大型锻件的主要尺寸进行测量以判别其是否达到工艺文件的要求。目前,工程测量铝合金等金属锻件尺寸的方法分为接触式测量法和非接触式测量法。接触式测量法,也就是直接测量法,其中用大型卡钳直接测量和“量杆”法最为常见,这类方法的优点是简单、无需特殊工具、可直接读取数据[28]。但由于大型锻件不便于搬运、在锻压时温度高达 800~1 200 ℃,并且会发出高亮的红光、现场环境恶劣苛刻等条件限制,非接触式测量法逐渐发展成为主流的尺寸形状测量方法。
非接触式测量表现出测量精度高、范围大、信息量丰富、处理速度快和重复性好等优点,包括投影光栅法、干涉测量法、飞行时间法(Time of Flight,TOF)、近景摄影测量法、结构光法和双目立体视觉测量法等[29-31]。非接触式测量法根据研究方向的不同可以分为激光测量技术和计算机视觉技术,其中激光测量技术又分为激光束投射法和激光扫描测距法[32-35]。激光束投射法操作简单、读数直观,一般用于测量锻件的长度尺寸,但存在装置略显复杂、有随机误差、激光斑在锻件上不易辨识等缺点。激光扫描测距法根据原理可分为相位雷达法和脉冲雷达法[30,36-37]。相位雷达法测量相对距离精度较高,测量绝对距离精度不高,不适合远距离、大范围测量。脉冲雷达法,也被称为飞行时间法,原理是计时器测定激光束发射到接收的时间,乘以光速,就可计算出观测位置到目标的距离。
由于大型锻件高温重载环境下激光器的测量精度会受到影响,因此各国在脉冲雷达测量技术的基础上采取 一 些 措 施 以 保 证 测 量 精 度 , 比 如 德 国 研 发 的LaCam-Forge 系统(如图 1 所示)[32];Bokhabrine 等[38]采用 2 台商用 TOF 激光测距仪来保证测量精度(图 2为 TOF 相机距离测量的不确定性来源);上海交通大学徐要刚等[39]通过二自由度的并联机构带动激光测距传感器运动,使用坐标变换得出三维外形进行尺寸测量。
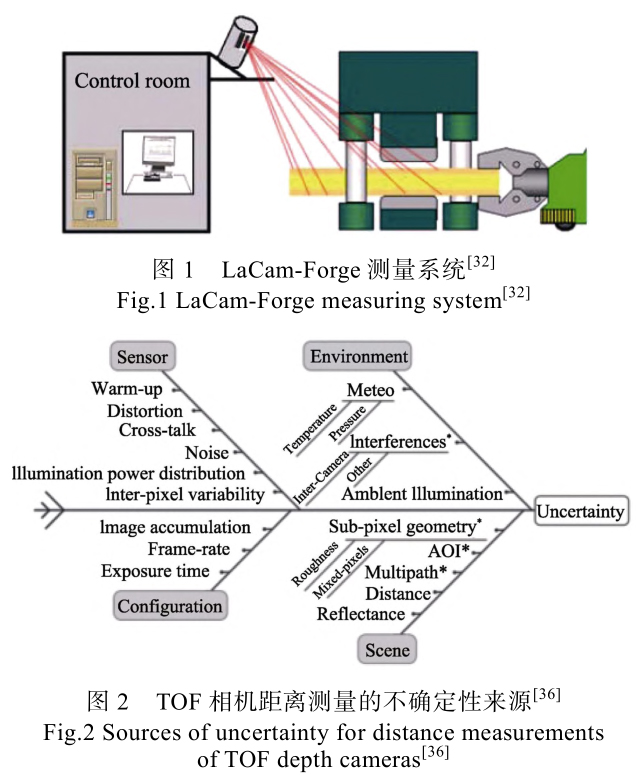
计算机视觉技术具有动态响应快、大量程、全自动等优点,符合目前向智能化工业发展的趋势,可分为基于双目立体视觉的被动视觉测量和基于结构光的主动视觉测量[40-44]。双目立体视觉是指通过立体匹配,根据视差来重建物体的深度信息,如图 3 所示。
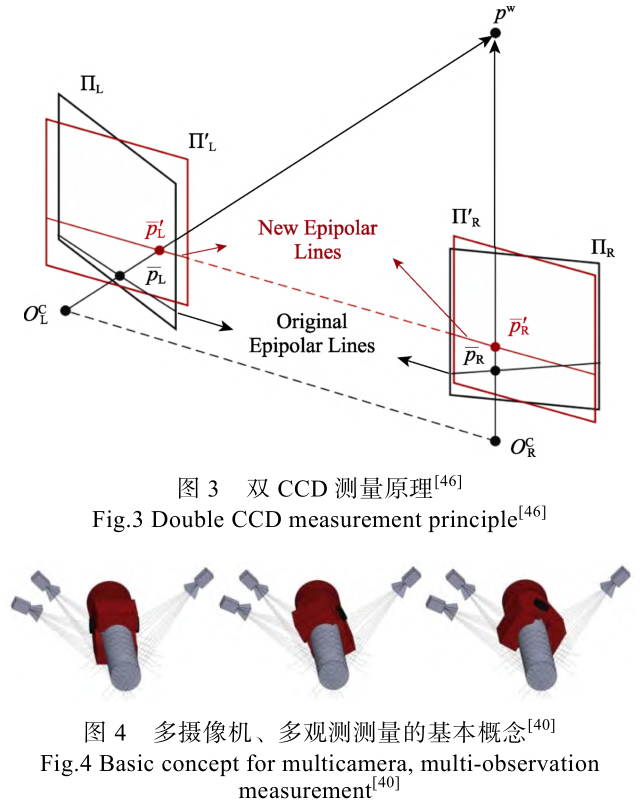
单 CCD 成像测量由于成像景深较浅,不能远距离、大范围测量,无法得到三维外形,所以应用受到限制。日本学者 Okamoto 等[45]研制出了基于双 CCD 成像的大型锻件测量系统,实现了高温锻件的高稳定测量。然而,立体匹配是双目立体视觉存在的一个难以克服的问题,为了避免立体匹配,Zhang 等[31]提出了基于线结构光的结构光视觉测量系统。该测量系统可以完成规则和不规则锻件的尺寸测量,但由于其采用的是导轨机构,导轨的尺寸易受到应用空间的限制,需事先设置扫描路径,且该测量系统采用的是平面网格的
标定方法,标定过程复杂。目前计算机视觉的应用日益广泛,多相机视觉系统的需求也越来越多,如图 4所示是多摄像机、多观测测量的基本概念。
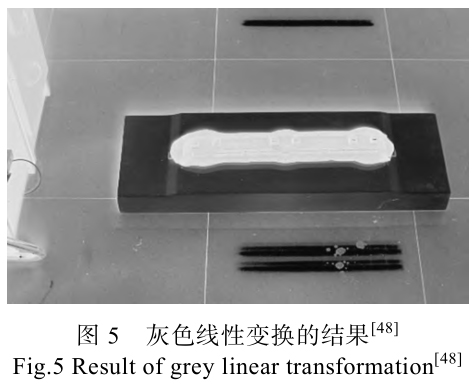
在测量大型锻件外形尺寸的同时,锻件表面是否存在裂纹、折叠、凹坑等缺陷也是评定锻件质量的一项重要指标。锻件表面检测方法包括传统检测法、自动检测法以及机器视觉检测法 3 类。传统检测法是人工目视检测和频闪光检测法,后者用频闪光源与专用摄像机替代了人眼,图 5 为闪光灰度线性变换的结果,但检测可信度和自动化程度仍然较低,无法满足大型锻件的生产[47-49]。自动检测法主要有涡流检测法、红外线检测法和漏磁检测法。涡流检测法是通过涡流的大小反应表面缺陷形态的无损检测方法,对于检测裂纹、刮伤、夹杂物、凹坑等灵敏度高,但缺点是必须充分加热,因此限制了检测速度,见图 6。红外线检测法常用于离线、小范围的测量,通过检测表面温度的上升值,可以确定缺陷的位置和深度。漏磁检测法的原理是:锻件被磁化后,表面缺陷处会形成漏磁场,分析漏磁通的密度从而确定缺陷的深度、宽度等特征。漏磁检测法除了能检测表面缺陷外,还能检测内部缺陷,检测精度也较高,但对缺陷的分类识别能力较差,且不能检测表面粗糙度。机器视觉检测法是光学、电子学、软件工程等学科的交叉和融合,已经成为当前各方研究的热点,分为基于激光和基于CCD 成像的检测系统,这一点与上文尺寸精度检测中激光检测和计算机视觉检测的原理相似。
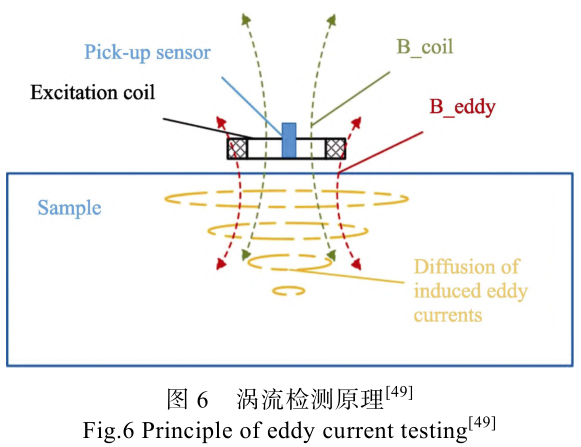
2.2 力学性能检测
在锻造生产过程中,除了必须保证大型锻件所要求的外形尺寸和表面质量外,还必须满足锻件在使用过程中的力学性能要求。大型锻件受力情况复杂,其力学性能的好坏直接关系到锻件能否达到质量检测标准和使用寿命要求。
力学性能的检测包括拉伸试验、冲击试验、硬度试验等测试。由于锻件的力学性能与其纤维方向成一定的关系,取样的位置也要具有代表性,对性能要求较高的铝合金等金属大型锻件,从 3 个方向(纵向、切线及横向)合理取样进行力学性能测试为最佳[50-51]。
按照 GB/T 228.1《金属材料拉伸试验第 1 部分:室温试验方法》等国家标准制备试样,并采用拉力试验机、冲击试验机等仪器设备进行力学性能数值的测定。图7 为不同应变速率下实验流变应力与新提出的本构模型预测流变应力的比较。
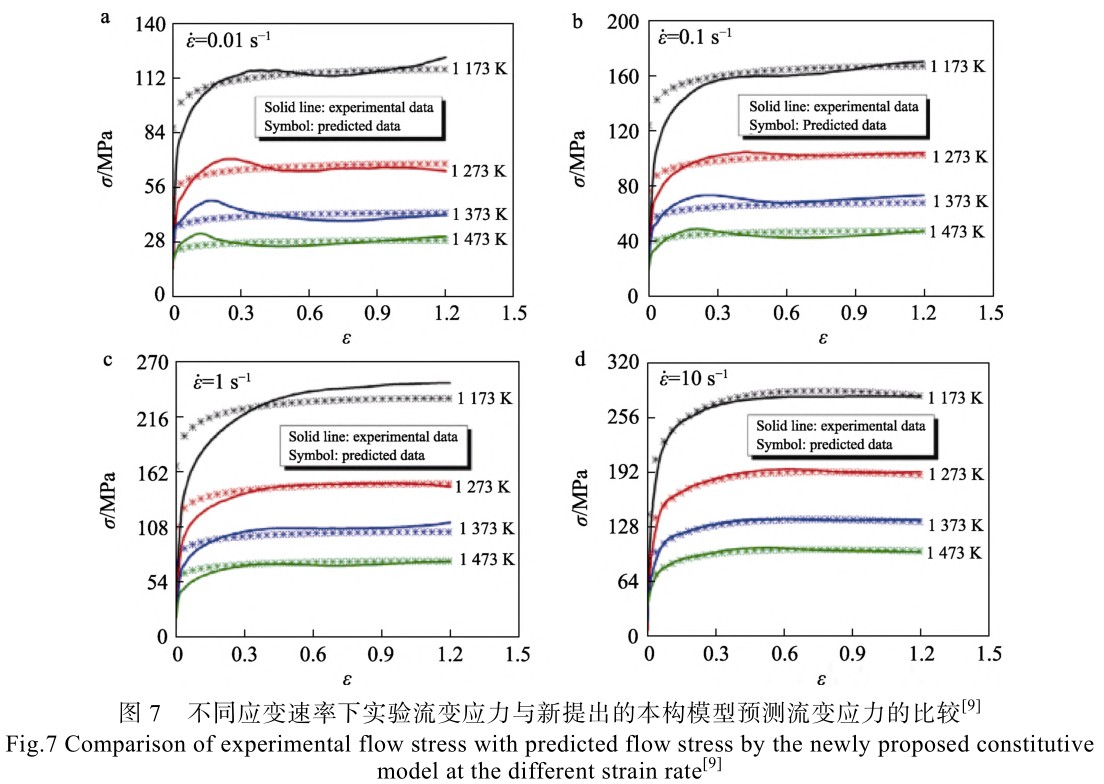
2.3 晶粒度/平均晶粒尺寸检测
锻件的微观组织对其性能有着决定性的作用,当锻件内部存在不正常组织时,不仅严重影响锻件的性能,还会提高锻件的废品率。在工业上通常将内部晶粒的尺寸大小视为重要的技术标准,比如铝合金的平均晶粒尺寸、高强钢的晶粒度。晶粒度/平均晶粒尺寸是衡量晶粒大小的尺度,可以用晶粒的平均直径或者平均面积表示,工业上通常使用晶粒度级数或者长度、面积、体积等评定或测量晶粒大小。
测量铝合金等金属晶粒度/平均晶粒尺寸的方法有很多,例如:金相分析法、电子显微镜法(SEM/EBSD)、超声波法、氦吸附小比表面法、X 射线衍射法等,其中金相分析法在国内外被广泛应用[52-54]。金相分析法通过测量和计算二维层次上薄膜的金相显微组织或者合金的金相试样磨面以确定合金组织在三位空间中的状态形貌,以此来建立合金组织、成分以及性能之间的定量关系。图 8 为采用新型锻造工艺处理的铝合金构件内部的 EBSD 结果。
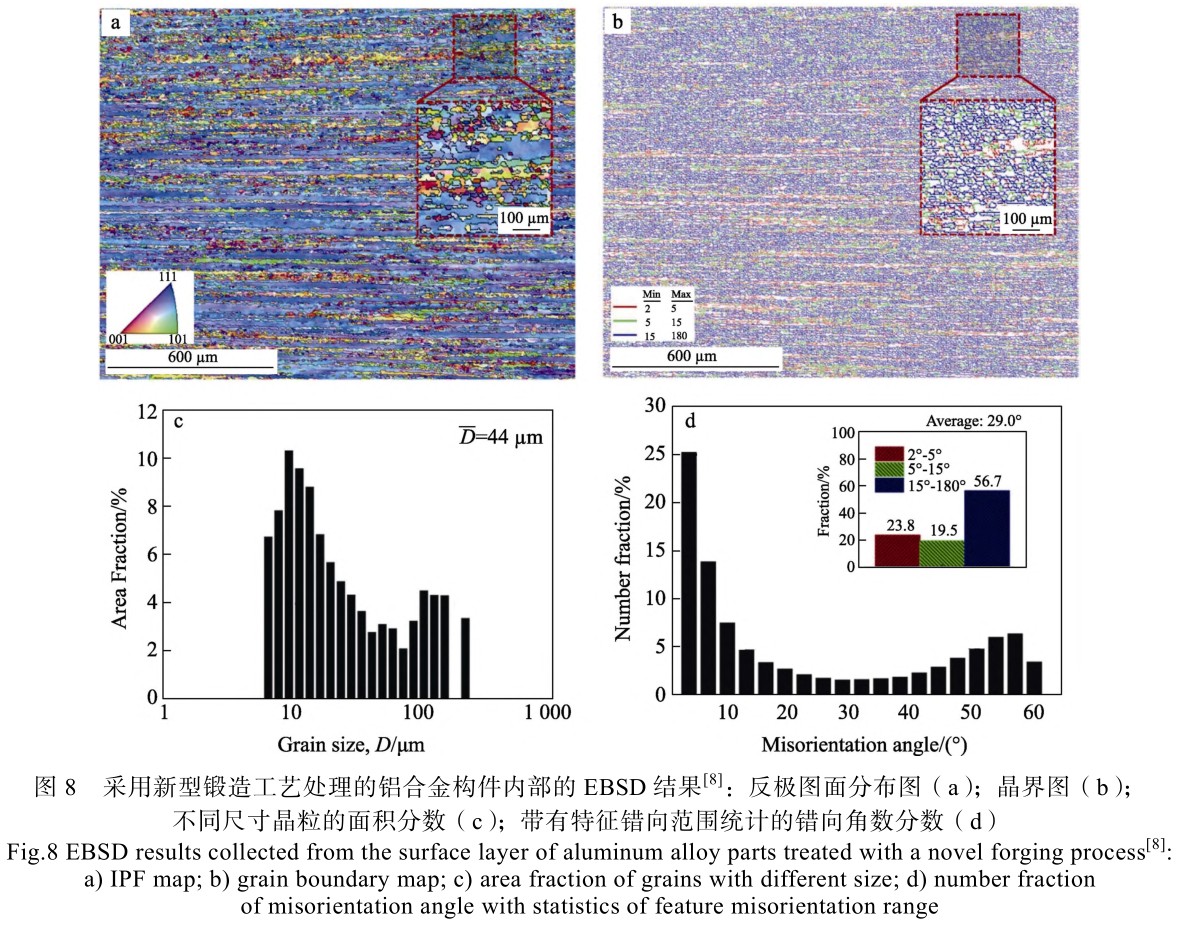
2.4 断裂韧性检测
铝合金等金属材料在使用过程中会发生各种失效,断裂是其中最为严重的一种失效形式,锻件会在承载远低于设计载荷的情况下发生断裂。材料发生断裂主要与锻件内部存在的微观裂纹有关,微观裂纹是在锻件的生产和加工过程中产生的,当锻件受到外部载荷作用时,裂纹会发生扩展造成锻件断裂。断裂韧性主要通过表征裂纹尖端应力应变的参量对金属材料的断裂进行定量分析,应力场强度因子 KIC、J 积分、裂纹尖端张开位移(Crack Tip Opening Displa-cement , CTOD ) 和 裂 纹 尖 端 张 开 角 ( Crack TipOpening Angle,CTOA)是目前在断裂韧性评价方法中应用较为广泛的几个参量[55-62]。金属材料平面应变断裂韧性 KIC 是在裂纹尖端区域的应力处于平面应变状态且裂纹尖端塑性变形受到约束时,材料在缓慢加载条件下的裂纹扩展抗力。J 积分表征弹塑性材料中裂纹扩展所需的能量值,临界值 JIC 可以定量描述裂纹尖端应力场强度。CTOD 是指理想弹塑性材料受到加载时,在裂纹尖端处张开的相对距离,利用 CTOD准则测算裂纹失稳扩展时,裂纹尖端开口的临界值为δc。上述几种不同的断裂韧度指标都有各自的适用领域和局限性,其中金属材料平面应变断裂韧性 KIC 在线弹性断裂力学领域具有成熟完善的理论基础,且其测试方法相对较为简便,在工程上的用途更为广泛。
动态断裂试验有很多不同的试验装置,实验方法和加载速率也是不同的,常用的实验装置包括电液伺服万能材料试验机、摆锤冲击试验机、落锤试验机、Hopkinson 拉/压杆。图 9 为阿什比图,显示出各种材料的塑性区大小取决于断裂韧性和屈服强度[61]。
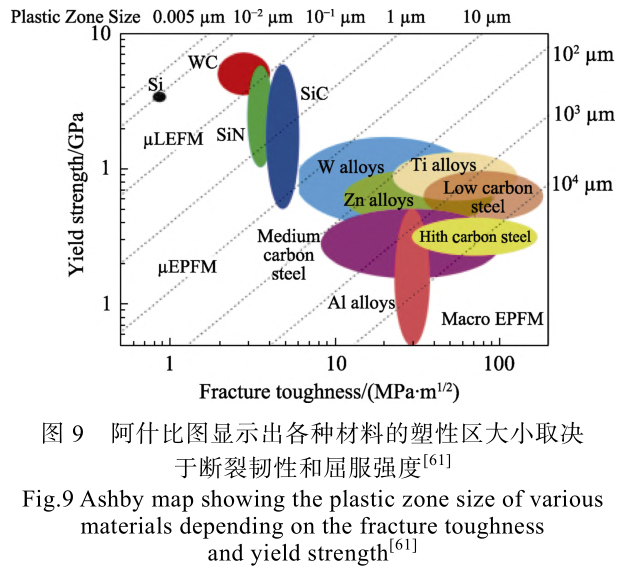
2.5 残余应力检测
铝合金等工程材料及其锻件在成形、热处理、机械加工以及装配等工艺过程中,都会不同程度地产生残余应力。残余应力对铝合金等金属大型锻件的强度、疲劳寿命、抗腐蚀能力和结构尺寸稳定性有很大影响,可以根据产生条件的不同将残余应力分为不均匀塑性变形产生的残余应力、热处理产生的残余应力和化学变化产生的残余应力[63]。目前残余应力的检测方法根据其对锻件的破坏程度可分为全破坏检测法、半破坏检测法和无损检测法 3 类[64-70],如图 10 所示。
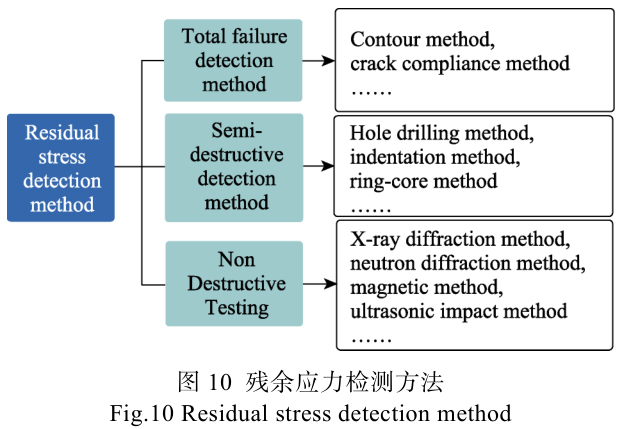
全破坏检测法包括轮廓法和裂纹柔度法;半破坏检测法包括钻孔法、压痕法、环芯法和剖面法;无损检测法包括 X 射线衍射法、中子衍射法、同步衍射法、磁测法和超声波检测法,超声无损检测如图 11 所示。残余应力的测试方法众多,各有优劣,应根据行业生产模式不同、企业现场情况不同、锻件形状尺寸不同等具体情况选用适合的测试方法,依照 GB/T 31310—2014《金属材料残余应力测定钻孔应变法》、GB/T7704—2017《无损检测 X 射线应力测定方法》等国家标准进行测验。对于铝合金锻件,工程上应用较多的残余应力检测方法是小孔法、环芯法和 X 射线衍射法。钻孔法又被称为小孔法或盲孔法,由于其具有对锻件破坏性小、测量精度较高、设备轻便且便宜等特点而得到广泛应用。环芯法也被称为圆环法或切槽法,其破坏性比钻孔法大,但它的应变释放率高于钻孔法,可测量近表面一定深度范围内的残余应力分布,且测试精度比钻孔法高。X 射线衍射法是残余应力测定技术中的无损检测方法之一,是研究最为广泛深入且成熟的应力测定方法,缺点是 X 射线的穿透能力有限,仅能测量表面的残余应力。
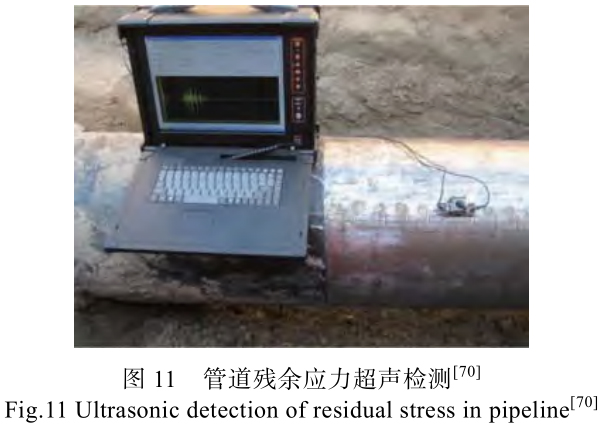
2.6 抗腐蚀能力检测
解析不同环境条件下铝合金等金属材料的腐蚀规律、评估金属耐蚀性能,并对试验环境气候条件的腐蚀性严酷度进行准确评级,通常需要根据实际服役条件针对性地进行腐蚀试验、检测分析试验结果并深入研究[71],各种腐蚀检测方法见表 6。其中应力腐蚀破裂作为危害较大的腐蚀形态之一在工业领域备受关注,当锻件处在特定的环境介质中时,同时承受一定的应力,就可能产生突发的、不可预知的应力腐蚀滞后开裂[72]。应力腐蚀开裂机理最广为人知的是阳极溶解和氢脆理论,而根据实验目的的不同,应力腐蚀测试方法可分为电化学法、恒应变法、恒载荷法、预制裂纹法、慢应变速率拉伸法,以及针对 7xxx 系列铝合金的电导率检测法,其中电化学法包括电化学阻抗谱和电化学噪声等[73-77]。另外,应力腐蚀检测手段还包括声发射技术(Acoustic Emission,AE)、长焦距 显 微 镜 、 数字图像相关技术 ( Digital ImageCorrelation,DIC)及形貌表征方法等原位检测手段。
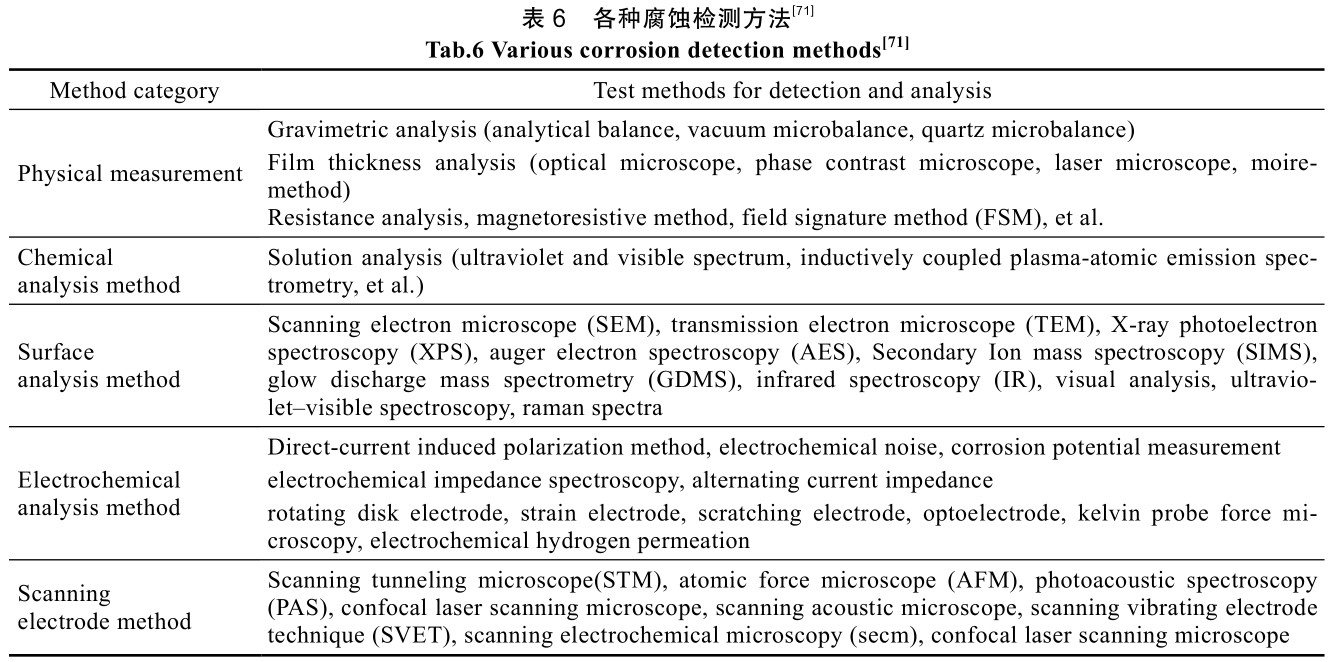
对于铝合金的抗应力腐蚀性能检测,无论是慢应变速率拉伸还是恒载荷法,均需要较长的检测时间,为了缩短检测时间、提高检测的经济性,在实际加工过程中,通常采用电导率在线检测。在一般情况下,电导率愈高,抗应力腐蚀性能愈好[78]。
2.7 其他检测
在航空航天领域,为了确保铝合金等金属大型锻件在使用过程中没有任何安全隐患,对锻件质量的要求极高,在更多情况下需要根据锻件的使用环境进行特定的质量检测,比如整体锻件的疲劳寿命检测,包括高周疲劳试验和低周疲劳试验。根据锻件在使用过程中的受力情况、重要程度和工作条件,需要检测的质量指标通常还有高温瞬时断裂强度、高温持久强度、持久塑性及高温蠕变强度等。
3 、能耗检测
工业节能不仅是“十四五”工业绿色发展规划及“双碳”目标的要求,更是工业企业提升综合实力的必由之路。能效管控是工业企业节能的一个重要研究方向,针对锻造生产高能耗的特点,亟需厘清生产制造过程中能量流转、损耗的机理。目前大多数能耗管控的研究注重于冷加工过程和金属冶炼过程,由于锻造过程火次多、工艺流程长、生产环境高温重载,涉及锻造生产单工序或多工序能耗管控方面的相关研究较少。下面就笔者的理解将工业能耗检测分为工厂层、装备层和产品层 3 个层次,以期为企业节能提供一些探索的思路。
3.1 工厂层能耗检测
针对航空航天行业锻造生产制造企业往往具备多个车间同时进行生产工作的特点,工厂层次的能耗检测应当采用分布式的能源管理系统。对单个车间分别采集多源能源数据,采集的瞬时能源数据同步上传到工业互联网进行数据的融合处理,最终在服务器端显示能源数据报表、图标等功能,实现能耗分析、能源数据统计、查询、信息共享[79],工业互联网结构如图 12 所示。对于锻造企业,生产过程各个工序的能耗情况不一样,但所消耗的能源类型一致,采用能源计量仪表技术,给各车间配置用电计量仪表、用天然气计量仪表、用水计量仪表等数据采集仪表,对工厂各车间所耗用的能源和载能工质进行计量,及时准确地获取各类能耗数据。通过对各车间的能耗数据进行分析,明确生产制造过程各个工序的能效情况,重点剖析能效较低工序的能源耗用情况,精准找到能耗最高的薄弱点进行原因分析,并针对性地提出能源管控的措施,进一步有效降低该车间的能耗,从而提高整个工厂的能效。
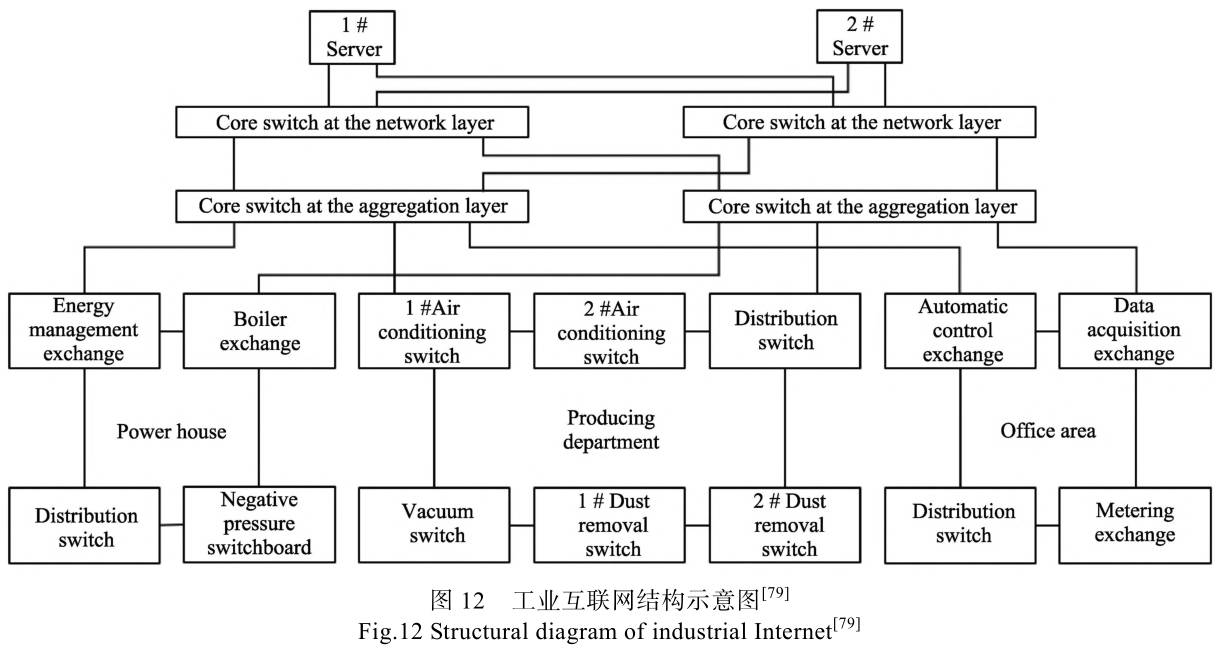
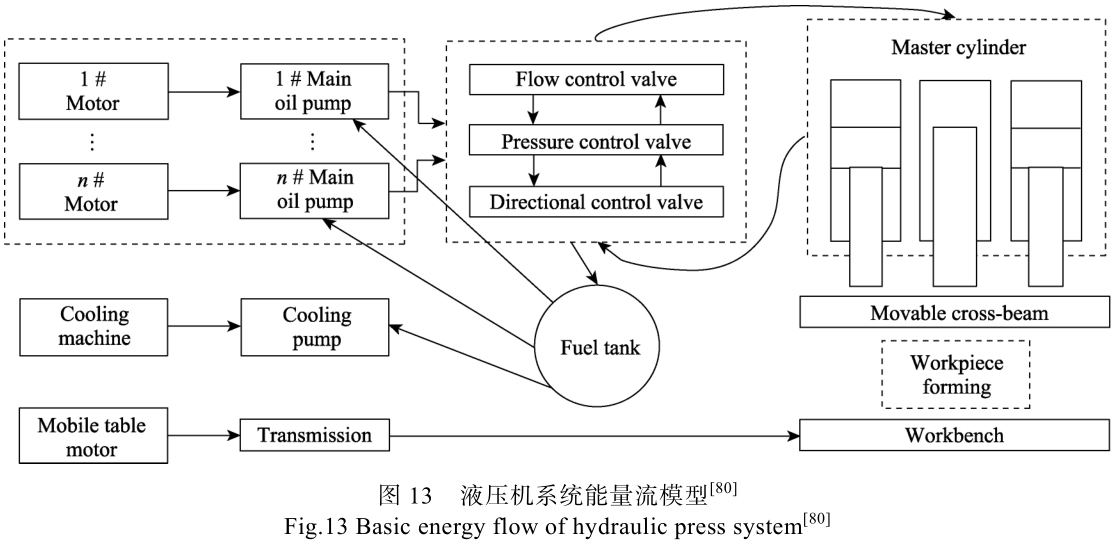
3.2 装备层能耗检测
工序是锻件成形的基本环节,工序质量是保障锻件质量的基础,每个工序都需要依靠该工序专用的生产制造装备,故考虑装备的能耗管控不仅有利于提高生产制造过程的能效,还有助于保障工序质量,从而保证锻件的质量。将各工序锻造装备当作能源数据采集对象,配置不同种类的计量仪表用以采集锻造装备的耗电量、耗天然气量以及耗水量等,通过能源分析系统得出在生产锻件时装备的功率和能效,找寻锻造装备能耗与锻件质量之间存在的关系,能够进一步明晰与装备关联性更强的质量形成机制,为通过改善工艺路径生产质量更好的锻件奠定了基础,最终实现降低锻件废品率、提高锻件生产制造能效的目的。
在对装备能耗进行分析时,可以将能耗分为 2类:加工能耗与基本能耗。加工能耗会因工艺和锻件的变化而产生较大的变化,随着加工时间变化呈非线性变化;基本能耗一般与装备的开机运行时间有关,不因工艺和锻件的变化而产生较大变化,与加工时间近似于线性关系,通常包括润滑系统能耗、控制系统能耗等[80],图 13 为液压机系统能量流模型。同时,在工序与工序之间、装备与装备之间存在各种各样的生产调度扰动因素,如未及时将锻件从加热炉中取出、锻件夹取操作失误等,可以采用 5M1E 分析法(人、机、料、法、环、测),从人员、机器、材料、方法、环境和测量 6 个维度来系统地控制扰动因素对锻件质量产生的影响,从而使能耗分析更加细致准确、更具有针对性,实现精准降低某一生产工序或某一锻造装备的能耗。
3.3 产品层能耗检测
当前,航空航天领域大型锻件的生产模式以单件小批量为主,其生产周期是单个锻件在各个工艺阶段生产周期的总和。在锻件的生产周期中,各种物料沿生产周期的轨迹流动,形成物质流;各种能源沿着转换、使用、回收、耗散的路径流动,形成能量流。物质流和能量流既独立又相互联系、彼此制约,能量流推动物质的流动和转变,而物质流在转变过程中又产生新的能量流[81],工序能量流如图 14 所示。锻造过程中物质流的主体是金属材料的流动,天然气、煤等燃料的流动为材料的控形控性过程提供必要的能量。
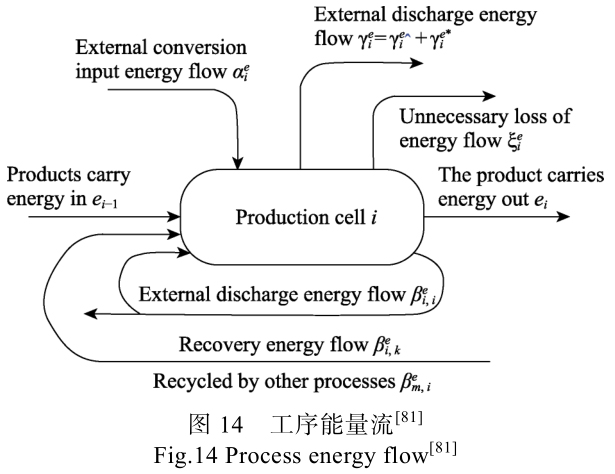
㶲(Exergy)作为一种衡量能源品质的指标,可以看作是在某种给定环境和约束条件下,一个过程或系统能够释放出的最大有用功或有效能。在进行锻压工序时,电能和天然气的能量一部分通过装置和燃烧转化为热能以及机械能,在这一过程中导致锻件形状改变、性能提高的能量转化成为锻件所拥有的能量,即㶲流,另一部分能量耗散在环境里提高了装备周边的温度。从本质上来说,通过改变工艺参数、装备参数使锻件达到质量及性能要求,是在调控各个工序中材料所获得能量的多少,因此厘清锻件生产周期中各工序的质量与能耗的关联机制是实现协同调控锻件质量能耗的一大重点,是企业在保证产品质量的同时节能降耗的必经之路。
因锻造生产过程复杂、自动化程度不高,为了更准确地明晰能量在生产周期中的流动,除检测计量仪表的能量数据、各工序的工艺参数及装备参数外,还需检测许多可控性低的扰动因素,如转运时间、环境温度等。再者,将材料本身视作一定量的能源,同时考虑锯料等材料切削工序的材料浪费,可以获知更为全面的锻件生产周期能源流动和能效,精确把握锻件生产周期中能耗较高的过程或工序,有针对性地实施最为适合的节能办法,从而加强锻造生产线上的能源管理、降低生产锻件的能耗、提高企业生产的一次良品率和能效。
4 、结论
大型锻件作为高端装备的关键承力构件,所采用的金属材料以铝合金和高强钢居多,其质量直接关系着装备的使用性能及服役安全;为满足我国“双碳”目标的要求,改善航空航天生产制造领域能耗管控粗放的行业现状,实现质量能耗协同管控,推动锻造工业向高质低耗发展是必然趋势。本文以铝合金等金属锻件为对象,回顾、归纳、分析和探索了航空航天大型锻件精密锻造过程缺陷形成、质量检测与能耗监测的内容。
1)分析了大型锻件在生产制造过程中的缺陷,将锻件缺陷根据生产过程归纳为原材料产生的缺陷、备料产生的缺陷、加热时产生的缺陷、锻压过程中产生的缺陷和锻后热处理中产生的缺陷 5 类,并分别阐述了缺陷的特点、产生原因及影响机制。
2)针对铝合金等金属锻件质量检测指标的不同,分为外观质量、力学性能、晶粒度/平均晶粒尺寸、断裂韧性、残余应力、抗腐蚀能力及其他性能,对不同指标的检测方法进行了分类归纳总结,并指出当前航空航天领域大型锻件生产过程常见的质量检测方法。
锻件的结构大型多样,工艺条件多变,质量形成机制复杂,故需要完备、便携、不破坏锻件的质量检测方法。对于外观质量,为节省人力时间,实现完整精确的自动化检测,非接触式测量是国内外研究的重点,包括激光测量和计算机视觉;对于其他质量,除常规通过拉伸压缩试验等基础试验检测力学性能外,还采用 TEM、EDS、XRD、EBSD 等检测方法分析锻件微观组织结构,由于航空航天领域常采用单件小批量的生产模式,其质量检测自然是更倾向于无损检测,X 射线、超声检测等易操作、耗时短的无损检测方法无疑是现在研究的热点。
3)按照工厂层、装备层和产品层 3 个层次分别提出生产制造过程能耗检测的方法,有针对性地阐明不同层次节能降耗的理论依据,在考虑不同层次生产扰动因素的同时,在工厂层引入分布式工业互联网布局,在装备层引入 5M1E㶲分析法,在产品层引入流,便于精准定位高能耗的环节,提出准确有效的方案,解决能耗突出环节的问题,为航空航天锻造行业提供了高效低耗转型发展的新思路。
参考文献:
[1]柳晶, 江明明. 锻造生产过程中的节能问题研究[J].机械设计与制造工程, 2016, 45(4): 88-91.
LIU J, JIANG M M. The Research on the Energy Saving for Forging Production Process[J]. Machine Design and Manufacturing Engineering, 2016, 45(4): 88-91.
[2]臧金鑫, 陈军洲, 韩凯, 等. 航空铝合金研究进展与发展趋势[J]. 中国材料进展, 2022, 41(10): 769-777.
ZANG J X, CHEN J Z, HAN K, et al. Research Progress and Development Tendency of Aeronautical Aluminum Alloys[J]. Materials China, 2022, 41(10): 769-777.
[3]李蓬川, 张睿. 基于数值模拟的飞机超高强度钢前起外筒模锻件制造[J]. 锻压技术, 2021, 46(9): 277-283.
LI P C, ZHANG R. Manufacture of Die Forgings for Aircraft Ultra-High Strength Steel Front-Lifting Outer Cylinder Based on Numerical Simulation[J]. Forging &Stamping Technology, 2021, 46(9): 277-283.
[4]赵明杰, 邓磊, 孙朝远, 等. 300M 高强钢大型构件全流程锻造变形机理及工艺研究进展[J]. 科学通报,2022, 67(11): 1036-1053.
ZHAO M J, DENG L, SUN O, et al. Advances on the Deformation Mechanism and Forging Technology of 300M High-Strength Steel Heavy Components in the Whole Forging Process[J]. Chinese Science Bulletin,2022, 67(11): 1036-1053.
[5]MAO X C, YI Y P, HUANG S Q, et al. Effects of Warm Saddle Forging Deformation on the Reduction of Sec-ond-Phase Particles and Control of the Three-Dimen-sional Mechanical Properties of 2219 Aluminum Alloy Rings[J]. Materials Science and Engineering: A, 2021,804: 140737.
[6]王富强, 杨立新, 王晓巍, 等. 某型机 7B04 铝合金接头锻造工艺优化[J]. 锻压技术, 2021, 46(10): 38-43.
WANG F Q, YANG L X, WANG X W, et al. Forging Process Optimization of 7 B04 Aluminum Alloy Joint in a Aircraft[J]. Forging & Stamping Technology, 2021,46(10): 38-43.
[7]XU J W, XU W C, LI J W, et al. Preform Design and Microstructure-Property Analysis for Isothermal Extru-sion of Complex Box-Shaped Components[J]. The In-ternational Journal of Advanced Manufacturing Tech-nology, 2021, 114(7): 2339-2356.
[8]ZHAO N, MA H J, SUN Q, et al. Microstructural Evo-lutions and Mechanical Properties of 6082 Aluminum Alloy Part Produced by A Solution-Forging Integrated Process[J]. Journal of Materials Processing Technology,2022, 308: 117715.
[9]ZHAO M J, HUANG L, LI C M, et al. Flow StressCharacteristics and Constitutive Modeling of Typical Ultrahigh-Strength Steel under High Temperature and Large Strain[J]. Steel Research International, 2023,94(3): 2200648.
[10] 陈功振. 热锻件缺陷分析及对策研究[J]. 机械工人(热加工), 2003(12): 47-49.
CHEN G Z. Defect Analysis and Countermeasure Re-search of Hot Forging[J]. MW Metal Forming, 2003(12):47-49.
[11] RATHI M G, JAKHADE N A. An Overview of Forging Processes with Their Defects[J]. International Journal of Scientific and Research Publications, 2014, 4(6): 1-7.
[12] 曹伟, 孙福勋. 热锻件常见缺陷及防止方法[J]. 现代制造技术与装备, 2012(3): 49-51.
CAO W, SUN F X. Hot Forging Common Defects and Prevention Methods[J]. Modern Manufacturing Tech-nology and Equipment, 2012(3): 49-51.
[13] 刘静安, 潘伟津, 罗立新, 等. 铝合金锻件主要缺陷的特征及产生原因[J]. 轻合金加工技术, 2014, 42(1):54-56.
LIU J A AN W J, LUO L X, et al. Main Features and Cause of the Defects of Aluminum Alloy Forging[J].Light Alloy Fabrication Technology, 2014, 42(1): 54-56.
[14] 冯扬明, 黎家行, 刘畅, 等. 铝合金锻件的主要缺陷分析与质量控制[C]// 2019 年中国铝加工产业年度大会暨中国(邹平)铝加工产业发展高峰论坛论文集. 邹平: 2019, 4.
FENG Y M, LI J X, LIU C, et al. Main Defect Analysis and Quality Control of Aluminum Alloy Forgings[C]//2019 China Aluminum Processing Industry Annual Conference and China (Zouping) Aluminum Processing Industry Development Summit Forum Proceedings.Zouping: 2019, 4.
[15] 冯扬明, 黎家行, 何梅琼, 等. 铝合金锻件的主要缺陷分析与质量控制[J]. 铝加工, 2021(4): 11-14.
FENG Y M, LI J X, HE M Q, et al. Main Defect Analy-sis and Quality Control of Aluminum Alloy Forgings[J].Aluminium Fabrication, 2021(4): 11-14.
[16] SHAN D B, ZHANG Y Q, WANG Y, et al. Defect Analysis of Complex-Shape Aluminum Alloy Forging[J].Transactions of Nonferrous Metals Society of China,2006, 16(A03): 1574-1579.
[17] 孟阳, 张国进. 消除大型锻件内白点缺陷的工艺方法浅析[J]. 锻压装备与制造技术, 2021, 56(6): 114-117.
MENG Y, ZHANG G J. Analysis on the Process Method of Eliminating White Spot Defects in Large Forgings[J].China Metalforming Equipment & Manufacturing Technology, 2021, 56(6): 114-117.
[18] WEN X L, GAO J P, LA Y G. Common Defect Analysis for Large Section Special Steel Forging[J]. Materials Science Forum, 2017, 898: 1208-1214.
[19] 梁士宝. 浅谈锻造加热不当产生的缺陷[J]. 现代企业教育, 2012(6): 20.
LIANG S B. Discussion on Defects Caused by Improper Forging Heating[J]. Modern Enterprise Education, 2012(6): 20.
[20] VARFOLOMEEV I, MOROZ S, SIEGELE D, et al.Study on Fatigue Crack Initiation and Propagation fromForging Defects[J]. Procedia Structural Integrity, 2017,7: 359-367.
[21] DENG L, WANG X Y, JIN J S, et al. Precision Forging Technology for Aluminum Alloy[J]. Frontiers of Me-chanical Engineering, 2018, 13(1): 25-36.
[22] GAO P F, YAN X G, FEI M Y, et al. Formation Mecha-nisms and Rules of Typical Types of Folding Defects during Die Forging[J]. The International Journal of Ad-vanced Manufacturing Technology, 2019, 104(1): 1603-1612.
[23] HAWRYLUK M, JAKUBIK J. Analysis of Forging De-fects for Selected Industrial Die Forging Processes[J].Engineering Failure Analysis, 2016, 59: 396-409.
[24] 赵学起. 基于压力曲线分析的一万吨水压机模锻过程质量控制系统研究[D]. 长沙: 中南大学, 2008.
ZHAO X Q. Research on Quality Control System of DieForging Process of 10, 000-Ton Hydraulic Press Based on Pressure Curve Analysis[D]. Changsha: Central South University, 2008.
[25] 冉林果, 唐玉婷. 铝合金精密模锻件折叠缺陷分析及改善措施[J]. 铝加工, 2022(3): 17-20.
RAN L G, TANG Y T. Analysis and Improvement Measures of Folding Defect of Aluminum Alloy Preci-sion Die Forging[J]. Aluminium Fabrication, 2022(3):17-20.
[26] 徐春雷, 冉金鹏, 杨小朋, 等. 基于工程机械常见铸锻件的热处理缺陷分析[J]. 热处理技术与装备, 2021,42(2): 45-48.
XU C L, RAN J P, YANG X P, et al. Analysis of Heat Treatment Defects Based on Common Casts and For-gings of Construction Machinery[J]. Heat Treatment Technology and Equipment, 2021, 42(2): 45-48.
[27] 中国机械工程学会锻压学会. 锻压手册-第 1 卷-锻造[M]. 北京: 机械工业出版社, 2002: 771-772.
Chinese Mechanical Engineering Society Forging Soci-ety. Forging Manual-Volume 1-Forging[M]. Beijing:China Machine Press, 2002: 771-772.
[28] 聂绍珉, 李树奎. 大锻件热态在线尺寸测量研究综述[J]. 金属加工(热加工), 2008(11): 22-25.
NIE S M, LI S K. Summary of Research on Hot On-Line Dimension Measurement of Heavy Forgings[J]. MWMetal Forming, 2008(11): 22-25.
[29] 李朝弟. 大锻件尺寸测量及形状检测技术研究[D].大连: 大连理工大学, 2010.
LI Z D. Research on Dimension Measurement and Shape Detection Technology for Large Forging[D]. Da-lian: Dalian University of Technology, 2010.
[30] WEN X, WANG J P, ZHANG G Y, et al. Three-Dimen-sional Morphology and Size Measurement of High-Temperature Metal Components Based on Machine Vi-sion Technology: A Review[J]. Sensors, 2021, 21(14):4680.
[31] ZHANG Y C, HAN J X, FU X B, et al. Measurement and Control Technology of the Size for Large Hot For-gings[J]. Measurement, 2014, 49: 52-59.
[32] 李建丽, 辛倩倩, 田丽, 等. 大型锻件在线尺寸测量方法综述[J]. 新型工业化, 2014, 4(1): 59-64.
LI J L, XIN Q Q, TIAN L, et al. A Review of Online Measurement Method for Large Forgings[J]. The Jour-nal of New Industrialization, 2014, 4(1): 59-64.
[33] ZHANG Y C, KONG T, FU X B, et al. The Dynamic Position Compensation Method of the Online Laser De-tection System for the Ring Workpiece[J]. Measurement,2019, 135: 555-564.
[34] SUN G M, HE G Y, ZHANG D W, et al. Body Diagonal Error Measurement and Evaluation of a Multiaxis Ma-chine Tool Using a Multibeam Laser Interferometer[J].The International Journal of Advanced Manufacturing Technology, 2020, 107(11): 4545-4559.
[35] ZHANG Y G, WANG Y D, LIU Y J, et al. A Concentric-ity Measurement Method for Large Forgings Based on Laser Ranging Principle[J]. Measurement, 2019, 147:106838.
[36] FRANGEZ V, SALIDO-MONZÚ D, WIESER A. As-sessment and Improvement of Distance Measurement Accuracy for Time-of-Flight Cameras[J]. IEEE Transac-tions on Instrumentation and Measurement, 2022, 71:1003511.
[37] WANG B G. A Novel Method for Measuring the Length of Hot Large Forgings Based on Machine Vision Sys-tem[J]. The International Journal of Advanced Manu-facturing Technology, 2022, 120(11): 7523-7531.
[38] BOKHABRINE Y, SEULIN R, LEW YAN VOON L F C,et al. 3D Characterization of Hot Metallic Shells during Industrial Forging[J]. Machine Vision and Applications,2012, 23(3): 417-425.
[39] 徐要刚. 热态大锻件尺度的在线测量技术研究[D].上海: 上海交通大学, 2009.
XU Y G. Research on On-Line Measurement Technol-ogy of Hot Forging Dimension[D]. Shanghai: Shanghai Jiao Tong University, 2009.
[40] HURNÍK J, ZATOČILOVÁ A, KONEČNÁ T, et al.Multi-View Camera System for Measurement of Heavy Forgings[J]. The International Journal of Advanced Manufacturing Technology, 2022, 121(11): 7295-7310.
[41] DANG A T, HSU Q C, TRUONG T T. A Simple Method for Dimensional Measurement of Ring-Shaped Objects Using Image Processing Technique[J]. The InternationalJournal of Advanced Manufacturing Technology, 2021,115(11): 3657-3678.
[42] WANG B G. A Study on Length Measurement Method of Hot Large Forgings Based on Binocular Vision Sys-tem[J]. Measurement, 2022, 199: 111586.
[43] ZHANG Y, LIU W, LU Y K, et al. Accurate Profile Measurement Method for Industrial Stereo-Vision Sys-tems[J]. Sensor Review, 2020, 40(4): 445-453.
[44] CHEN Y Z, ZHOU F Q, ZHOU M X, et al. Pose Meas-urement Approach Based on Two-Stage Binocular Vi-sion for Docking Large Components[J]. Measurement Science and Technology, 2020, 31(12): 125002.
[45] FAN R, WANG L, BOCUS M J, et al. Computer Stereo Vision for Autonomous Driving[J]. arXiv preprint arXiv:2012.03194, 2020.
[46] OKAMOTO A, WASA Y, KAGAWA Y. Development of Shape Measurement System for Hot Large Forgings[J].R and D: Research and Development Kobe Steel Engi-neering Reports, 2007, 57(3): 29-33.
[47] 余慧敏, 马续创. 国内外板带材表面质量检测方法研究进展[J]. 重型机械, 2014(5): 5-9.
YU H M, MA X C. Research Progress of Surface Fin-ishing Test Methods of Board Strip at Domestic and Overseas[J]. Heavy Machinery, 2014(5): 5-9.
[48] WANG A M, ZHANG Z H, QIAO R T. A Visual Meas-urement Method of the Three-Dimensional Coordinates of the Center of Forgings with Asymmetric Flash for the Intelligent Hammer Die Forging[J]. Measurement, 2023,210: 112581.
[49] SOPHIAN A, TIAN G Y, FAN M B. Pulsed Eddy Cur-rent Non-Destructive Testing and Evaluation: A Re-view[J]. Chinese Journal of Mechanical Engineering,2017, 30(3): 500-514.
[50] 霍育林, 夏琴香, 黎明, 等. 轴类大锻件锻造工艺研究现状与质量检测方法[C]// 2008 泛珠三角锻压年会论文集, 安顺: 2008, 98-100.
HUO Y L, XIA Q X, LI M, et al. Current Research on Techniques of Heavy Axis Forgings and the Quality Detection Method[C]// Proceedings of 2008 Pan-Pearl River Delta Forging Annual Conference, Anshun: 2008,98-100.
[51] 邓敏. 探究金属材料力学性能检测试样的取样与制备[J]. 山西冶金, 2023, 46(1): 102-104.
DENG M. Sampling and Preparation of Test Specimens for Mechanical Properties of Metal Materials[J]. Shanxi Metallurgy, 2023, 46(1): 102-104.
[52] 张琪. 基于 PSO-LSSVM 的铝带坯晶粒度软测量模型的研究与优化[D]. 长沙: 中南大学, 2010: 3.
ZHANG Q. Research and Optimization of Soft Sensing Model for Grain Size of Aluminum Strip Based on PSO-LSSVM[D]. Changsha: Central South University,2010: 3.
[53] HASSANZADEH-TABRIZI S A. Precise Calculation of Crystallite Size of Nanomaterials: A Review[J]. Journal of Alloys and Compounds, 2023, 968: 171914.
[54] MONGKOLSUTTIRAT K, BUAJARERN J. Uncer-tainty Evaluation of Crystallite Size Measurements of Nanoparticle Using X-Ray Diffraction Analysis (XRD)[J]. Journal of Physics: Conference Series, 2021, 1719(1): 012054.
[55] 王思军. 电磁环境下 2024-T3 铝合金的动态断裂韧性测量与表征[D]. 武汉: 华中科技大学, 2017.
WANG S J. Measurement and Characterization of Dy-namic Fracture Toughness of 2024-T3 Aluminum Alloy in Electromagnetic Environment[D]. Wuhan: Huazhong University of Science and Technology, 2017.
[56] 蒋慧玲. 基于泛形理论的断裂韧性测试方法研究[D].西安: 西安理工大学, 2022: 2-4.
JIANG H L. Research on Fracture Toughness Testing Method Based on Conformal Theory[D]. Xi’an: Xi’an University of Technology, 2022: 2-4.
[57] 王思军, 李宁, 郗学奎. 2024-T3 铝合金的动态断裂韧性[J]. 精密成形工程, 2017, 9(4): 72-78.
WANG S J, LI N, XI X K. Dynamic Fractural Tough-ness of 2024-T3 Aluminum Alloy[J]. Journal of Net-shape Forming Engineering, 2017, 9(4): 72-78.
[58] 李鹤飞, 张鹏, 张哲峰. 高强钢断裂韧性与疲劳裂纹扩展评价方法研究进展[J]. 机械工程学报, 2023, 59(16): 18-31.
LI H F, ZHANG P, ZHANG Z F. Research Progress on Evaluation Methods of Fracture Toughness and Fatigue Crack Growth in High-strength Steel[J]. Journal of Me-chanical Engineering, 2023, 59(16): 18-31.
[59] AST J, GHIDELLI M, DURST K, et al. A Review of Experimental Approaches to Fracture Toughness Evaluation at the Micro-Scale[J]. Materials & Design,2019, 173: 107762.
[60] FATIMAH S, RAGADHITA R, AL HUSAENI D F, et al.How to Calculate Crystallite Size from X-Ray Diffrac-tion (XRD) Using Scherrer Method[J]. ASEAN Journal of Science and Engineering, 2021, 2(1): 65-76.
[61] SAXENA A K, BRINCKMANN S, VÖLKER B, et al.Experimental Conditions Affecting the Measured Frac-ture Toughness at the Microscale: Notch Geometry and Crack Extension Measurement[J]. Materials & Design,2020, 191: 108582.
[62] PARASURAMAN P, SONAR T, RAJAKUMAR S. Mi-crostructure, Tensile Properties and Fracture Toughness of Friction Stir Welded AA7075-T651 Aluminium Alloy Joints[J]. Materials Testing, 2022, 64(12): 1843-1850.
[63] 董嘉智. 航空铝合金变形残余应力动态分析测试研究[D]. 沈阳: 沈阳航空航天大学, 2022.
DONG J Z. Research on Dynamic Analysis and Testing of Deformation Residual Stress of Aviation Aluminum Alloy[D]. Shenyang: Shenyang Aerospace University,2022.
[64] 丁稳稳, 高晓龙, 刘晶. 残余应力检测方法研究现状[J]. 宝鸡文理学院学报(自然科学版), 2022, 42(1):103-108.
DING W W, GAO X L, LIU J. Research Status of Re-sidual Stress Detection Methods[J]. Journal of Baoji University of Arts and Sciences (Natural Science Edi-tion), 2022, 42(1): 103-108.
[65] GUO J, FU H Y, PAN B, et al. Recent Progress of Re-sidual Stress Measurement Methods: A Review[J]. Chi-nese Journal of Aeronautics, 2021, 34(2): 54-78.
[66] TABATABAEIAN A, GHASEMI A R, SHOKRIEH MM, et al. Residual Stress in Engineering Materials: A Review[J]. Advanced Engineering Materials, 2022, 24(3):2100786.
[67] LODH A, THOOL K, SAMAJDAR I. X-Ray Diffraction for the Determination of Residual Stress of Crystalline Material: An Overview[J]. Transactions of the Indian Institute of Metals, 2022, 75(4): 983-995.
[68] SARMAST A, SCHUBNELL J, PREUßNER J, et al.Residual Stress Analysis in Industrial Parts: A Compre-hensive Comparison of XRD Methods[J]. Journal of Materials Science, 2023, 58(44): 16905-16929.
[69] ZHAN Y, LI Y M, ZHANG E D, et al. Laser Ultrasonic Technology for Residual Stress Measurement of 7075 Aluminum Alloy Friction Stir Welding[J]. Applied Acous-tics, 2019, 145: 52-59.
[70] 徐春广, 王俊峰, 宋剑峰, 等. 油气管道焊接残余应力超声无损检测与原位调控技术[J]. 石油科学通报,2016, 1(3): 442-449.
XU C G, WANG J F, SONG J F, et al. Ultrasonic Non-destructive Testing and in Situ Regulation Technology of Residual Stress for Oil and Gas Pipelines[J]. Petro-leum Science Bulletin, 2016, 1(3): 442-449.
[71] 庞志开, 杨杰, 李光茂, 等. 金属腐蚀特性分析方法与检测技术[J]. 环境技术, 2022, 40(5): 81-85.
PANG Z K, YANG J, LI G M, et al. Analysis Method and Detection Technology of Metal Corrosion Charac-teristics[J]. Environmental Technology, 2022, 40(5): 81-85.
[72] 刘敬福, 周祥春, 曲迎东. Al-Zn-Mg 合金应力腐蚀断裂的研究进展[J]. 金属热处理, 2020, 45(9): 21-28.
LIU J F, ZHOU X C, QU Y D. Research Progress of Stress Corrosion Cracking (SCC) of Al-Zn-Mg Alloy[J].Heat Treatment of Metals, 2020, 45(9): 21-28.
[73] 王学慧. 不锈钢和铝合金在典型环境中的应力腐蚀特征与检测方法[D]. 天津: 天津大学, 2015: 2-16.
WANG X H. Stress Corrosion Characteristics and De-tection Methods of Stainless Steel and Aluminum Alloy in Typical Environment[D].Tianjin: Tianjin University,2015: 2-16.
[74] BERLANGA-LABARI C, BIEZMA-MORALEDA M V,RIVERO P J. Corrosion of Cast Aluminum Alloys: A Review[J]. Metals, 2020, 10(10): 1384.
[75] ADAMS F V, AKINWAMIDE S O, OBADELE B, et al.Comparison Study on the Corrosion Behavior of Alu-minum Alloys in Different Acidic Media[J]. Materials Today: Proceedings, 2021, 38: 1040-1043.
[76] KAUFMAN J. Corrosion of Aluminum and Aluminum Alloys[J]. ASM Handbook, 2019, 2B: 96-129.
[77] TZENG Y C, CHEN R Y, LEE S L. Nondestructive Tests on the Effect of Mg Content on the Corrosion and Mechanical Properties of 5000 Series Aluminum Al-loys[J]. Materials Chemistry and Physics, 2021, 259:124202.
[78] 林亮华, 陈君, 彭海健. 过时效态 Al-Zn-Mg-Cu 合金电导率与应力腐蚀的相关性[J]. 材料热处理学报,2022, 43(4): 73-80.
LIN L H, CHEN J, PENG H J. Relationship between Electrical Conductivity and Stress Corrosion of Over-Aged Al-Zn-Mg-Cu Alloy[J]. Transactions of Materials and Heat Treatment, 2022, 43(4): 73-80.
[79] 朱文林. 基于互联网技术的工厂能源管理系统设计与应用[J]. 中国新通信, 2023, 25(11): 43-45.
ZHU W L. Design and Application of Factory Energy Management System Based on Internet Technology[J].China New Telecommunications, 2023, 25(11): 43-45.
[80] 吴元浩. 大型液压机能耗监测系统研究[D]. 合肥: 合肥工业大学, 2022.
WU Y H. Research on Energy Consumption Monitoring System of Large Hydraulic Press[D]. Hefei: Hefei Uni-versity of Technology, 2022.
[81] 蔡九菊, 王建军, 张琦, 等. 钢铁企业物质流、能量流及其对 CO2 排放的影响[J]. 环境科学研究, 2008(1):196-200.
CAI J J, WANG J J, ZHANG Q, et al. Material Flows and Energy Flows in lron & Steel Factory and Their In-fluence on CO2 Emissions[J]. Research of Environ-mental Sciences, 2008(1): 196-200.
相关链接