TC6钛合金的名义成分为Ti-6Al-2.5Mo-1.5Cr-0.5Fe-0.3Si,是一种良好的马氏体型a-b两相钛合金,含有a稳定元素Al、同晶型b稳定元素Mo和共析型b稳定元素Cr、Fe和Si,b稳定系数Kb=0.6。该合金的使用状态一般为退火状态,也可进行适当的强化热处理。TC6合金的室温强度和在450℃下热强性能高于TC4合金。该合金还具有较好的热加工工艺性能,可以进行焊接和各种方式的机械加工。

TC6钛合金主要用来制造航空发动机的压气机盘和叶片等零件,能在400℃以下长时间工作6000h以上和在450℃工作2000h以下。该合金还可作为中强合金用来制造飞机的隔框、接头等承力结构件及不同用途的紧固件。生产的半成品主要有棒材、锻件及模锻件等。
相近牌号 有 BT3-1(俄罗斯)。
1、范围
1.1 主题内容
本规范规定了飞机结构用TC6钛合金自有锻件和模锻件(以下简称镶件)的分类、技术要求、试验方法、验收规则、质量保证规定和交货准备等。
1.2 适用范围
本规范适用于截面厚度不大于200mm的TC6钛合金锻件。
1.3 分类
1.3.1 根据零件的受力情况、重要程度和工作条件及材料和冶金工艺因素的不同,锻件分为
Ⅰ、Ⅱ、Ⅲ三类:
I类锻件需逐件进行力学性能试验;
Ⅱ类锻件选择性进行力学性能试验;
Ⅲ类件只进行硬度试验。
1.3.2 锻件的类别根据需方要求确定,并注明在图样上。
2、引用文件
GB/T228 金属拉伸试验方法
GB/T229 金属夏比形缺口冲击试验方法
GB/T231 金属布氏硬度试验方法
GB/T3620.2 钛及钛合金加工产品化学成分及成分允许偏差
GB/T4161 金属材料平面应变断裂韧度Kie试验方法
GB/T4338 金属高温拉伸试验方法
GB/T4698 海绵钛、钛及钛合金化学分析方法
GB/T5168 两相钛合金高低倍组织检验方法
GB/T6395 金属高温拉伸持久试验方法
GB/T6397-1986 金属拉伸试验试样
GB/T8180 钛及钛合金加工产品包装、标志、运输和贮存
HB5432-1989 飞机用TC4钛合金锻件
11-CL-058A 11号工程用TC6钛合金棒材和锻坯技术条件
3、要求
3.1 材料
3.1.1 用于制造锻件的铸锭应采用真空电弧炉熔炼,熔炼次数应不少于两次,最后一次熔炼稳定阶段的炉内压强应不大于5Pa。
3.1.2 自耗电极禁止使用钨极氩弧焊焊接。
3.1.3 原材料应符合11-CL-058A的技术要求。
3.2 化学成分
3.2.1 锻件的化学成分应符合11-CL-058A的规定。
3.2.2 订购方从产品上取样进行化学成分复验分析时,其成分允许偏差应符合GB/T3620.2的规定。
3.3 供应状态
锻件在热处理状态下经吹砂酸洗后供应。具体热处理状态应在合同中注明。
3.4 力学性能
3.4.1 锻件退货状态的室涅力学性能和高温力学性能应分别符合表1和表2的规定。锻件固溶时效状态的室温力学性能应符合表1的规定。订购方要求测定固溶时效力学性能时,应在合同中注明。锻件推荐的热处理制度应符合表3的规定。
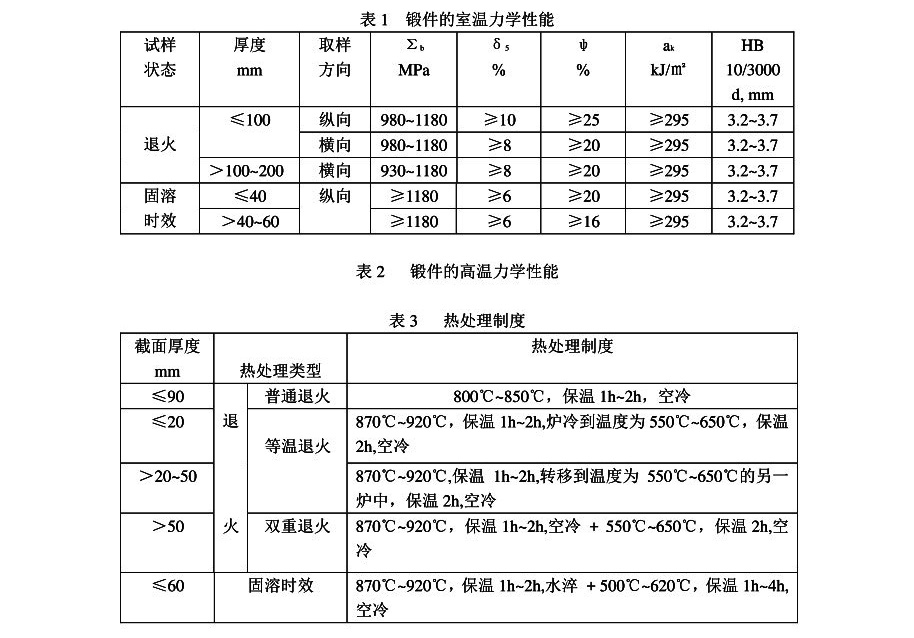
3.4.3 断裂韧度
锻件的室温断裂韧度(T-L方向) 应不小于42MPa√m。需方有要求时, 在合同中注明,暂不作为报废依据。
3.5 超声波探伤
3.5.1 超声波探伤检验分AAA、AA和A三个级别,检验结果应符合表4的规定。
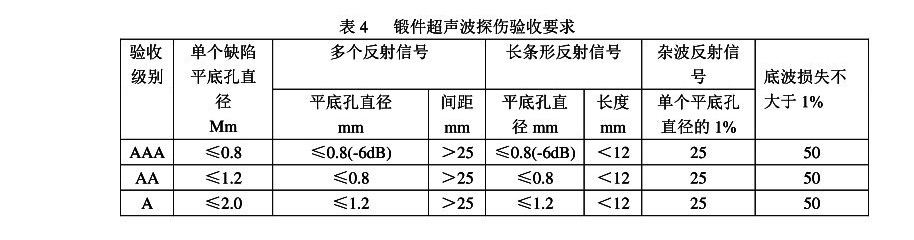
3.5.2 检验级别、部位和方法应在锻件图或超声检验图表上注明。
3.6 金相组织
3.6.1 低倍组织
3.6.1.1 低倍上不允许有缩孔、气孔、分层、偏析、裂纹、金属或非金属夹杂及其它肉眼可见的冶金缺陷。
3.6.1.2 低倍晶粒度按图1的10级评级图评定。1级~5级为合格。当出现6级时,以高倍组织和力学性能为准。
3.6.1.3 锻件的金属流线应符合锻件图的规定,不允许有穿流和严重涡流。锻件未注明的流线方向,一般沿外形分布。
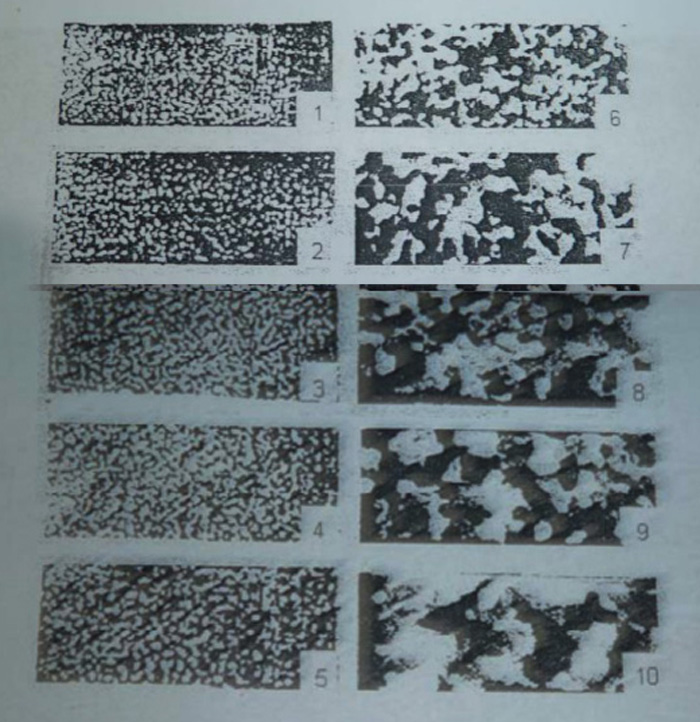
3.6.2 显微组织
显微组织按图2的10类评级图进行评定,1类~8类为合格,9类~10类为不合格。等轴初生a相尺寸应不超过0.125mm;条状初生a相长度应不超过0.25mm。
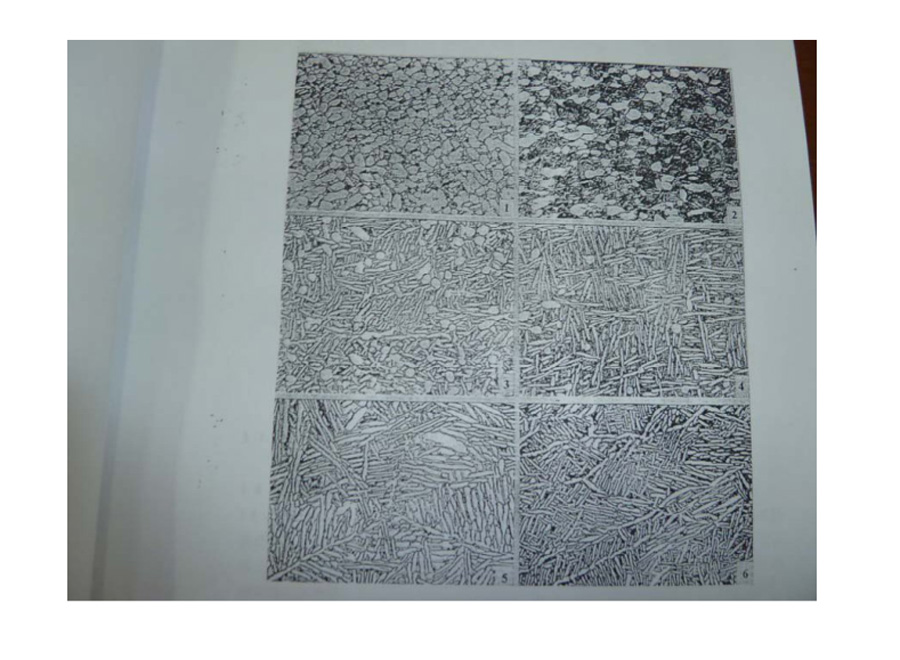
3.7 尺寸和外形
锻件的形状、尺寸和允许公差应符合供需双方签订的图样规定。
3.8 表面质量
3.8.1 锻件加工表面上的裂纹、氧化皮等缺陷必须清除。压伤、压坑等局部缺陷,如果其深度不超过机加工余量的1/2,则允许不清除。在所有清除和允许不清除缺陷的部分,均须保证锻件留有1/2的名义加工余量,需方有要求时,还应保证锻件留有后续加工过程中所需的附加工艺余量。
3.8.2 锻件非加工表面上不允许有a层存在。折叠、划痕等缺陷需全部清除。在所有清除的部位,必需保证锻件的单面极限尺寸。缺陷的清除应圆滑过渡,非加工表面上的清除宽度不得小于深度的10倍。
3.9 头部管理和锭节管理
3.9.1 头部管理
锻件若使用靠近冒口的第一根棒材制造时,则在该根棒材靠近冒口的那个锻件上作出标志“T”,并在合格证中予以注明。
3.9.2 锭节管理
Ⅰ、Ⅱ类锻件还应进行锭节号管理。
3.10 其他要求
3.10.1 经科研、试制确定的主导工艺不能随意更改,主导工艺的更改需征得需方同意后方可实施。重大工艺的更改,需要重新组织鉴定。
3.10.2 承制方有责任保存产品质量跟踪所必须的重要文件。
4、质量保证规定
4.1 检验责任
除合同或订单中另有规定外,承制方应负责完成本规范规定的所有检验。必要时上级鉴
定机构有权对规范所述的任一检验项目进行检查。
4.1.1 合格责任
所有产品必须符合本规范第4章得所有要求。若合同中包括本规范未规定的检验要求,承制方还应保证所提交验收的产品符合合同要求。
4.1.2 复验和仲裁
订购方对收到的产品应进行复验。如复验结果与本规范的规定不符时,由双方共同判定。意见不统一时,可由双方同意的第三者仲裁。
4.2 质量一致性检验
4.2.1 组批
锻件应成批提交验收,每批锻件应由同一批的棒材、在同一生产周期制造的、同一热处理炉批和同一图号(锻件代号)的锻件组成.
4.2.2 检验规则及取样数量
研(试)制批产品质量一致性检验项目、取样数量应符合表5的规定。批生产检验项目、取样数量另行规定。
4.2.3 取样部位
力学性能、低倍试样的取样部位和数量根据需方要求确定,并注明在锻件图或取样图上。
显微组织试样应取自锻件变形量最大和最小两个部位的横向或拉断的拉伸试样上。氢分析试样取自成品锻件最小截面处距表面4mm之内,其他元素可取自锻件的相应部位。
头部管理的锻件,检验时必需包括靠近冒口的锻件。
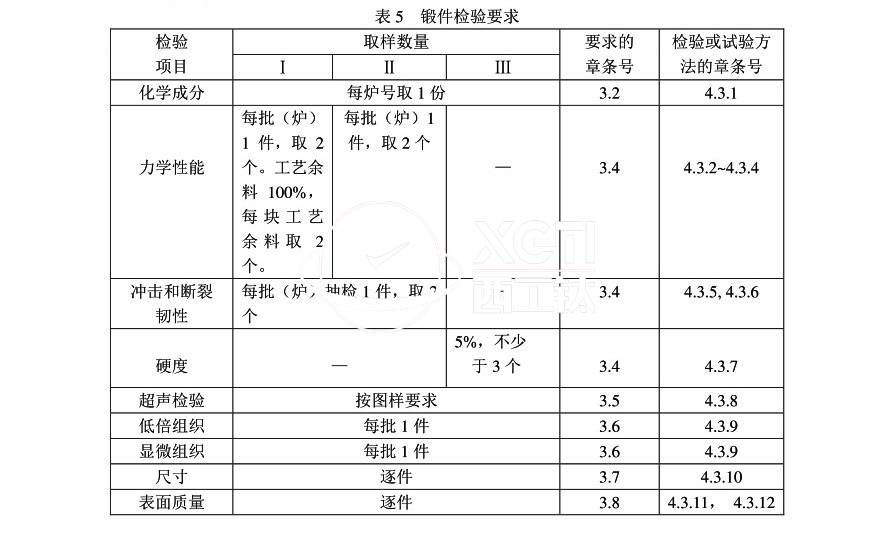
4.2.4 检验结果的判定
4.2.4.1 化学成分、高低倍组织不合格时,整批不合格。产品的超声检验、尺寸、表面状况及外观质量不合格时,单件不合格。
4.2.4.2 在力学性能检验中,如果有一个试样的试验结果不合格,则从原锻件取双倍试样进行该不合格项目的重复试验,若重复试验仍有一个试样的试验结果不合格,则该批锻件为不合格。
4.3 检验方法
4.3.1 化学成分仲裁分析方法按GB/T4698进行。
4.3.2 室温拉伸试验按GB/T228进行。室温拉伸试样应采用GB/T6397-1986中的试样R7.
4.3.3 高温拉伸试验按GB/T4338进行。
4.3.4 高温拉伸持久试验按GB6395进行。
4.3.5 金属冲击试验按GB/T229的U型缺口试样进行。
4.3.6 金属平面变断裂韧度Ki试验方法按GB/T4161进行。试样形式为紧凑拉伸试样。
4.3.7 硬度试验按GB/T231进行。
4.3.8 锻件的超声波探伤检查按HB5432-1989附录B进行。
4.3.9 低倍组织、显微组织的检验参照GB/T5168进行。高倍金相组织检查时的放大倍率一般选用500×,特殊情况可选用100×或200×。
4.3.10 尺寸检验用相应精度的量具进行。
4.3.11 表面状况检验用粗糙度检验用标块对比法进行。
4.3.12 外观质量用目视检查.
5、交货准备
5.1 包装、标志、运输和贮存
产品的包装、标志、运输和贮存按GB/T8180的规定执行。
5.2 产品质量证明书
每批产品应附有产品质量证明书,其上注明:
a.承制方名称;
b.订货方名称及合同号;
c.合金牌号、批号、锭节号;
d.热处理炉批号、热处理制度;
e.热处理炉批号、热处理制度;
f.锻件图号或代号;
g.锻件数量;
h.各项分析检验结果;
i.技术监督部门印记;
j.本规范编号;
k.包装日期。
5.3 产品标志
锻件应有以下标记:
a.合金牌号;
b.锻件图号或代号;
c.熔炼炉(批)号;
d.热处理炉批号(代号);
e.承制单位检印。
6、说明事项
6.1 订货文件内容
合同或订单上应写明:
a.本规范名称和编号;
b.产品名称、锻件号、合金牌号、锻件类别、供应状态、规格和数量;
c.化学成分中“其他杂质元素”的测定与否;
d.超声波探伤检查和显微组织检验要求;
e.产品质量跟踪重要文件保证期限的特殊要求;
f.高温力学性能测定与否;
g.其他需要说明的事项。
相关链接