引言
大型环锻件[1]作为一种大型无缝环件,是大型机械设备[2]的重要组成部分,被广泛应用于航空机匣、风电法兰、轴承外圈及齿轮环、核反应堆加强圈等关键部位,这种大型零件工作环境恶劣,常要求具有耐高温、耐腐蚀、高强韧性等优良性能[3(] 如图1)。随着环锻行业的发展,钛环锻件种类越来越多,尺寸也趋于大型化,逐渐满足了行业发展的需求。近年来,随着环件轧制水平的提高,大型矩形截面环锻件的研制已经达到了国际水平,2018 年首都航天机械有限公司在国内成功轧制出φ9m 薄壁铝合金大型环件[4],2019 年由中科院金属研究所与伊莱特重工研制出φ15.6m 奥氏体不锈钢超大型环锻件,解决了众多行业领域“卡脖子”的难题[5]。
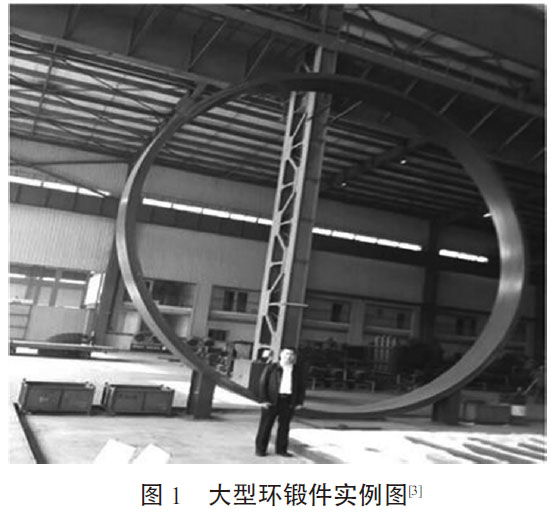
但是,当下大型异形截面环件仍存在难成形的问题,诸多学者为解决大型异形截面环件难成形的问题,对其制坯工艺进行了大量的研究。本文以解决大型异形截面环件难成形和成形精度低的问题为前提,阐述了国内外学者对环件轧制有限元模拟、大型异形截面环件制坯优化和轧制方法方面的理论分析及研究成果,并介绍了大型环件常见内、外部缺陷,以期为大型环锻件的成形成性一体化发展提供经验。
1、 环件轧制有限元模拟
环件轧制是一个热力耦合的非线性过程,仅采用理论分析的方法来指导实际生产势必会造成资源的浪费和成本的提高。20 世纪90 年代末,有限元软件在我国兴起,以CAE 为代表的有限元模拟软件在模拟精确度、用户界面、后处理等方面逐渐完善,为环件的有限元模拟奠定了基础。
近年来,诸多学者通过有限元软件归纳出环轧理论和环件塑性变形规律,为现实中环锻件的生产提供了宝贵的经验。潘剡等[6]与张家港海陆环形锻件有限公司合作,对φ9m 超大型环件设计了轧制工艺参数和新的芯辊进给方式,对其进行径轴向轧制(Radial- Axial Ring Rolling,RARR)有限元模拟并在RAM9000 数控轧制机上成功轧制出成形精度和组织性能满足要求的超大型钛法兰环件。Han 等人[7]提出了一种能实现环件的壁厚减少、内直径扩大、高度减少的RARR 新工艺,该工艺驱动辊起约束作用,并通过ABAQUS 对矩形截面毛坯进行约束轧制模拟,最终能够有效控制环件成形的尺寸精度。Zhou[8]针对大型L 形环件建立了异形锥辊径轴向轧制数学模型,通过Deform-3D 有限元软件进行仿真模拟,将模拟的有限元结果与数学预测的外径、外径增长率、驱动辊转速等参数进行了比较,模拟参数与预测参数吻合较好。田笑[9]对2Al4 铝合金薄壁异形环件宏观力学性能及微观组织模拟,研究表明环件在170~400℃范围内,温度越高环件晶粒分布越均匀,并从环件的金属流动方面进行轧制孔型优化,提出了环件近净成形工艺。Liang 等[10]针对异形截面环件直径达到要求值时轮廓不能填充的问题,提出了拉拔系数的影响,即主动变形区对被动变形区的牵拉作用,建立了外凹槽截面环件热力耦合模型,进行了环件毛坯尺寸设计的数学公式,运用响应面法(Response surface method,RSM)建立了拉拔系数与其影响因子之间的关系,拟合出具体的环件毛坯尺寸计算公式。Meng 等[11]利用ANSYS 有限元软件对大型环件镦粗过程中棒料高径比、液压机镦粗力对应变、鼓形、切向应力的影响,通过实验对比基本吻合,为大型环件镦粗工艺提供了基本的指导。
有限元模拟为环件轧制提供了可靠的实验数据,促进了环件轧制理论的建立,为后期大型、复杂截面环锻件的发展奠定了基础。在实际生产过程中,企业或实验者可预先在环件生产前进行有限元分析,借此优化实际生产方法或参数。随着研究的深入,学者们发现在异形截面环件成形过程中,环件制坯与轧制同样重要,对环件成形都有重要的影响,随后促使大量学者对制坯工艺进行研究。
2 、大型异形截面环锻件制坯工艺
目前,大型矩形截面环锻件轧制技术已比较成熟,大型异形截面环锻件成形工艺仍有待优化,诸多研究表明并非所有的轮廓都能由矩形截面的毛坯形成,但是毛坯的预轧制会对环件的成形带来一定的成效。而且,大型异形截面环锻件生产是高成本、高能耗的复杂过程,对环轧过程中制坯工艺的优化有利于节省能源和减少成本的消耗,对响应国家节能减排的号召有重要的推动作用。
传统的大型异形截面环件轧制工艺流程为镦粗→冲孔→环轧→机加工,工艺流程如图2。受现存成形技术制约,在大型异形截面环件成形过程中可能会出现鱼尾、填充不满、余量过多等缺陷,大大降低了成形精度,提高了生产成本。经长期试验及理论研究发现优化毛坯可解决上述问题,武汉理工大学胡博奎[12]设计了三种不同形状的环坯轧制双列圆锥滚子轴承,经成形实验获得了高精度的轴承外圈锻件,验证了预锻、终锻制坯的可行性和外单锥度型毛坯的轧制优越性。何松等[13]针对锥台复合截面环件提出了“等壁厚型”和“变壁厚型”两种环坯设计方法,通过添加尺寸修正系数η 规范了最优环轧制坯范围,实验和模拟都获得了截面填充效果好、成形精度高的锥台复合截面环件。陈孝庆[14]针对大型内台阶环锻件设计了梯形截面和矩形截面两种毛坯,并对两种不同截面的环坯设计了不同形状的芯辊,研究发现梯形截面毛坯在轧制过程中温度和应变分布较为均匀。
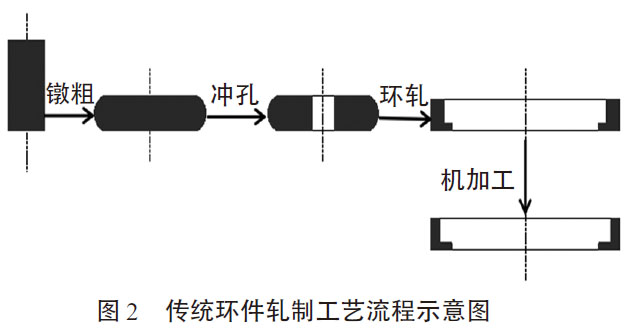
王清等[15]通过胎膜制坯+ 异形环件轧制成形工艺获得了2m 级大型高温合金机匣,在保证了组织和性能优良的基础上,提高了材料的利用率。邓加东等[16]针对大型外台阶环件提出近净成形工艺,如图3,通过研究模锻坯料的内、外斜度对环件金属流动和填充能力的影响,确定出最佳参数方案,经实验验证内台阶环件成形效果良好,在减少环件坯料的同时提高了环件最终截面的填充效果。
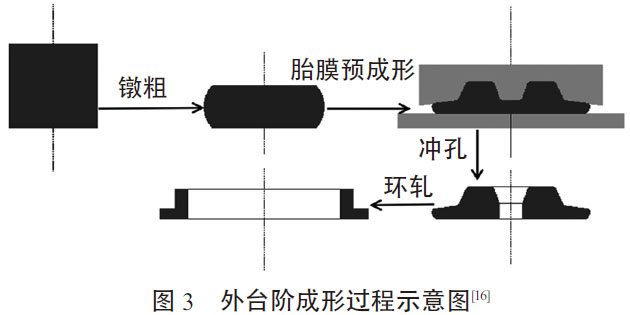
3 、环件轧制方法研究
选择合适的钛环件轧制方法可以有效的提高环件轧制的成形精度与组织性能,在节省轧制成本的同时获得合格的环件。在目前的研究中,常用的环件轧制方法有马架扩孔、径向轧制、径轴向轧制和胀形工艺。
3.1 马架扩孔成形
马架扩孔是使环件直径增大、壁厚减薄、轴向略增长的工艺,在工作时环件受三向压应力状态,使得裂纹难以在环件内部产生,故有较好的成形质量[17]。其成形原理如图4 所示。砧板连续下压环件,环件被芯轴所支撑住,同时环件在砧板每压下一次后,转动一定的角度,该过程往复循环,以此实现环件直径壁厚减薄、轴向略增长。刘红艳等[18] 将马架设置为可分离式,设计了可以调节宽度和高度的马架,增加了马架的适用性。王晓娟等[19]将马架和芯轴进行改进,解决了工作时不稳定而发生晃动的问题。曹繁、蓝箭等[20]针对传统的马架扩孔需要人力操控芯轴及环件转动的问题,设计了新的结构,实现了马架扩孔自动进给,提高了其自动化程度。
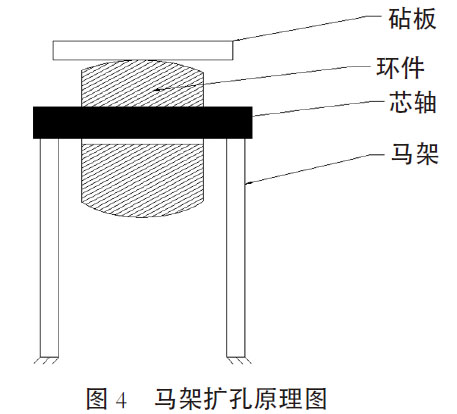
虽然诸多学者对马架扩孔装置进行了研究和改进,但是大型环件因体积大、成形直径大,选用马架扩孔成形还是会有所受限,马架扩孔作为一种传统的环件辗扩工艺,对于小型环件的辗扩有一定的优势,但是对于大型环件的辗扩,与径轴向轧制工艺相比在成本、精度和效率方面都有不足之处,目前马架扩孔常用于大型环件制坯过程中,在制坯方面成效颇丰。
3.2 径向轧制和径轴向轧制
径向轧制是环件预制坯运用辗环机,使环件直径增大、截面轮廓成形的塑性成形工艺[21],其成形原理如图5。径向轧制设备由径向轧辊和导向辊组成,径向轧辊包括驱动辊和芯辊,其中驱动辊主动旋转并通过摩擦力带动环件旋转,芯辊做径向进给运动,并在环件摩擦力的作用下被动旋转;导向辊用于环件外轮廓的整圆,在工作时抱住环件,随着环件直径扩大的方向移动,起辅助作用。
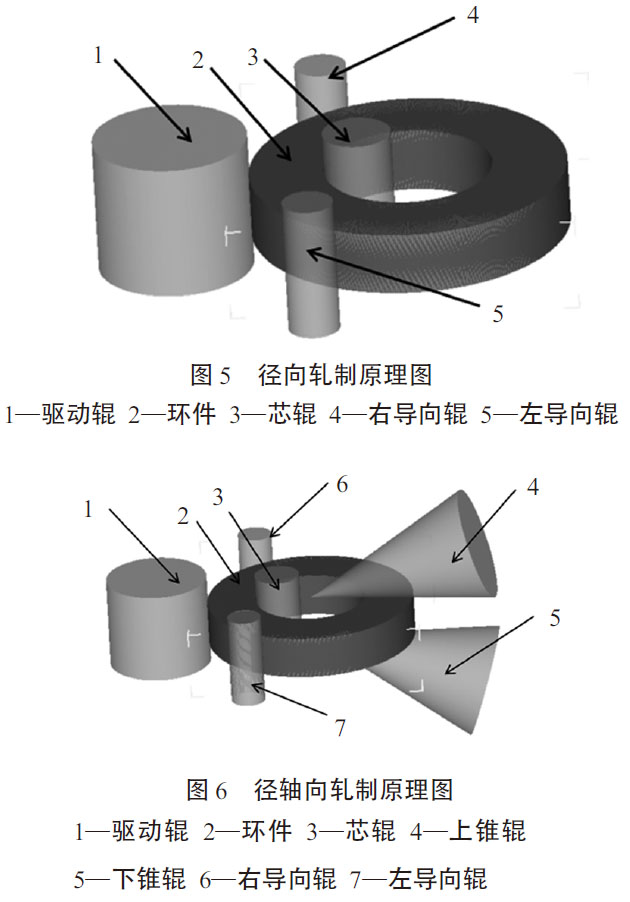
与径向轧制相比,径轴向轧制多了一对锥辊,即上、下锥辊,其工作原理如图6,上、下锥辊绕自身轴线旋转,同时,上锥辊边向后退边向轴向进给,上、下锥辊用于消除环件的轴向宽展,在如此往复循环的过程中,实现了环件的直径增大、壁厚减薄、高度减小、轮廓成形。
径轴向轧制是当前使用最广泛的大型环件轧制工艺,早期,华林教授[22]根据运动学条件和静力学条件推导出环件轧制的咬入条件和锻透条件,并给出各轧辊运动参数的取值范围和计算方法,为国内环锻件的研究奠定了理论基础。耿剑等[23]对环锻件径轴向轧制力和轧制力矩进行推导,并发现在环坯高度相同的情况下,环坯壁厚和芯辊尺寸越大,轧制过程中需要的径向轧制力越大。
刘东[24]根据轧制曲线建立环件径轴向轧制过程中径、轴向进给量之间的关系,通过建立运动学方程精确描述径轴向轧制过程中的运动规律。郭良刚等[25]根据环件径轴向轧制体积不变原理提出了一种对矩形截面环件毛坯尺寸设计的方法,该设计方法基于环件轧制比k 和变形量分配比tanα,并给出具体的适用范围。
3.3 胀形工艺
胀形工艺是指环件在胀形力的作用下,环件整体沿周向拉伸、直径扩大,壁厚沿径向压缩、减薄并发生塑性变形[26],其原理如图7 所示。胀形工艺具有卸载后回弹小、变形区材料不易转移、不会失稳等优点。胀形工艺又可分为软模胀形和刚性模胀形两类,胀形工艺常用做工业生产中的成形工艺和强化工艺[27],软膜胀形常使用液体、气体或弹性体提供径向胀形力来达到胀形的目的,成形精度高;刚性模胀形采用分块式模提供径向胀形力,适用于成形精度稍低的成形。
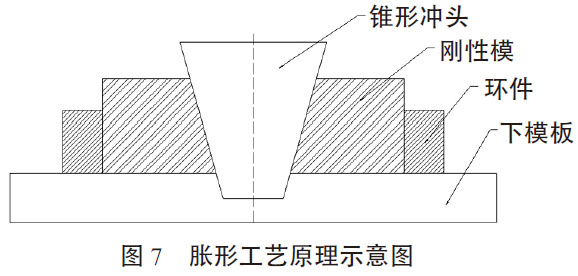
目前胀形工艺常被用来对终轧后的环件残余应力均化处理和整圆,环件在胀形力的作用下可以获得更好的组织和应力分布[28]。肖石霞[29]针对大型风电轴承环常出现椭圆、直径不扩大、壁厚不均匀等缺陷,提出了径向轧制与胀形工艺相结合的方法,环件轧制前期使用径向轧制,轧制到一定程度改用胀形工艺,终轧后的环件成形精度好、内应力低。江道等[30]通过环件胀形工艺对2A70 铝合金环件成形实验和微观探究,胀形后的环件拉伸强度提高明显,促使第二相质点间距缩小,提高了铝合金的强度。西北工业大学魏志坚等[31]研究了胀形技术对TC4 合金辗轧环锻件残余应力及分布的影响,通过实验发现胀形工艺可有效调控环件的残余应力。魏辉[32]基于Deform- 3D 对2216 铝合金5m 级异形截面机匣锻件胀形工艺模拟,通过实验验证了胀形工艺可改善环件的应变均匀性,进一步说明了工艺的有效性。
4 、大型环锻件轧制缺陷研究
由于大型环件轧制的不均匀性,导致环件内部金属流动不规则,从而造成了各种缺陷的产生,比如大型异形截面环锻件常存在上下表面宽展、孔型填充不满等缺陷;另一方面,由于轧制过程的不稳定,环件整体可能会出现折叠、翘曲、失稳等现象导致轧制失败。面对航天、航空、风电、核电等行业对大型环锻件的需求日益剧增,如何改善大型环锻件的制造工艺和方法,改善大锻件的金属流动、成形精度,减少缺陷的产生、缩短工艺流程,仍是当下研究的需要。针对大型环件缺陷的产生,将从环件内、外部缺陷两个方面进行探究。
4.1 环件外部缺陷
孔型填充不满是最常见的环件外部缺陷之一,以孔型填充不满为例,对环件外部缺陷进行介绍。孔型填充不满分为两种:第一种为轧制过程中孔型始终未能充满;第二种为在轧制中某一时刻孔型填充完全,随着轧制的进行造成孔型处金属尺寸逐渐减小而与孔型逐渐分离[33]。孔型填充不满常出现在大型异形截面环锻件轧制中,该缺陷产生原因常为毛坯和轧辊尺寸设计不合理,导致环件孔型处径、轴向金属流动不均匀,如图8。徐戊矫等[34]通过中心复合实验和电场法设计了锥形法兰环件的毛坯,并建立了环件截面填充率的模 型,发现在异形截面环件填充过程中,先选择难成形的区域填充再选择易成形的区域填充的填充顺序更有利于环件的孔型填充,同时芯辊进给速度的增加有利于改善环件截面填充率。王斌[35]针对斜I 截面环件在直径达到要求时孔型填充不满的问题,优化了坯料尺寸和模具型腔,实验发现在金属填充型腔阶段,环件的金属流动主要发生在环件径向,故坯料和模具的设计应有利于环件的径向金属流动。
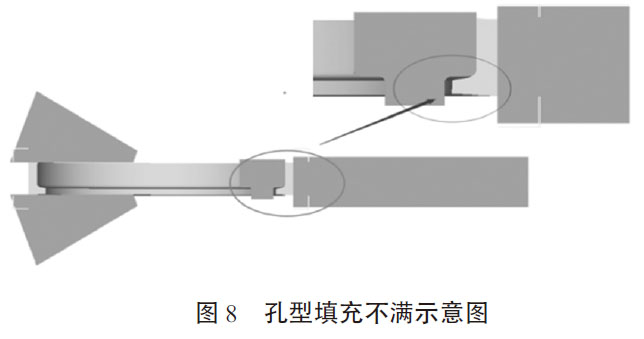
4.2 环件内部缺陷
大型环锻件在轧制完成以后需要进行热处理来提高环件的最终组织性能,然而加热温度及保温时间不当通常会引起环件内部晶粒粗大和组织偏析等内部缺陷,合理的热处理工艺制定将有助于减少内部缺陷的产生,改善环件的最终性能。黄建武[36]针对2219 铝合金环件在传统热处理工艺中存在晶粒组织粗大的问题,提出了环件深冷变形工艺,通过该工艺可以极大的抑制动态回复,得到细小的等轴晶粒,显著增强了环件的强度和塑性,降低了环件的各向异性。尉潇健等[37]采用840℃水淬+590℃回火的方法对42CrMo 离心铸 坯辗扩成形后的环件进行调质处理,经调质处理后环件的残余应力得到释放,塑性大幅提高,力学性能大幅改善。胡向东[38]针对GH141 高温合金终轧后环件进行1080℃退火处理,发现随着退火时间和固溶时间增加,环件的晶粒尺寸基本不发生变化。陈克宇[39]为提高环件的力学性能,对42Cr-Mo4 大型异形环件进行热处理工艺设计,成形后的环件具有细小的晶粒和较低的内应力,经调质处理后晶粒度达到了8.5 级。
针对环件成形的外部缺陷问题,合理的设计毛坯尺寸、轧辊形状和轧辊进给参数是避免外部缺陷产生的保障;针对环件内部缺陷问题,合理的热处理工艺是保障环件最终组织性能的关键。环件外部无缺陷使得环件具有良好的成形质量,环件内部无缺陷使得环件具有良好的性能,在保证了环件内部、外部均无缺陷的前提下进行工艺研制,即成形成性一体化工艺[40],是当下环锻件发展的风向标。
5、 结论和展望
5.1 结论
本文阐述了近年来国内外学者在环件轧制有限元模拟、大型异形截面环锻件制坯优化和环件轧制方法方面的理论分析及研究成果,并对大型环锻件的常见缺陷进行探讨,并得出以下结论:
(1)环件轧制有限元模拟促进了环件轧制理论的建立,为实际生产提供了可靠的参数和生产方法,并为将来更大型、更复杂截面环锻件的发展奠定了基础。
(2)制坯优化促进了大型异形截面环锻件的成形精度提高和能源消耗的减少,保证了大型异形截面填充位置具有较好的金属流动。
(3)探讨了马架扩孔、径向轧制、径轴向轧制和胀形工艺四种成形方法的成形原理和适用范围。马架扩孔适用于小型、精度不高的环件轧制,也常用于大型环件制坯中;径轴向轧制是在径向轧制上的改进,是当今大型环锻件轧制最常用的方法,其具有良好的塑性成形优势;胀形工艺常用于环件轧制完成后的整圆和残余应力均化处理。
(4)环件满足锻透条件和咬入条件的前提下,选择较大的芯辊进给速度、设计合理的毛坯尺寸和热处理工艺是避免缺陷产生的保障。
5.2 展望
环件轧制逐渐趋向于成形精密化、直径增大化、截面复杂化,环件成形工艺的创新、成形精度的提高、节能节材为国内外广大学者所关注。对于未来大型环锻件的发展给出以下几点要求:
(1)随着国家航空、航天、风电、核电等领域的发展和国内环锻件市场高端进口量需求的增加,国内对于更复杂的大型异形截面环锻件的理论模型建立和工艺开发有待进一步完善。
(2)运用有限元分析软件模拟生产过程,对大型环锻件的发展起到了重要作用,未来对于有限元软件环件轧制的微观组织模拟是下一步开发的重点。
(3)环件成形与成性一体化调控是当下研究的热点,大型环件的控稳、控形、控性一体化建设,对于大型钛环锻件的发展具有重要的意义。
参考文献:
[1] 赵顺治,林涛,郭卫民,等. 大型环件径轴向轧制成形仿真及试验研究[J]. 中国铸造装备与技术, 2021,56(03):45- 52.
[2] Kim K H, Suk H G, Huh M Y. Development of the profilering rolling process for large slewing rings of alloy steels[J].Journal of Materials Processing Technology, 2007,187:730- 733.
[3] 华林,钱东升,邓加东,等. 超大型环件轧制理论与技术[J].锻压技术, 2018,43(07):17- 31.
[4] 阳代军,张文学,徐坤和,等. 9m 级超大直径2219 铝合金整体环轧制工艺及质量分析[J]. 热加工工艺, 2019,48 (05):189- 193.
[5] 佚名.中国轧制世界单体最重、直径最大奥氏体不锈钢环锻件[J].经济导刊,2019(04):8.
[6] 潘剡,钱东升,华林,等. Φ9m 超大型环件径轴向轧制成形仿真模拟与实验[J].塑性工程学报, 2012,19(03):19- 24.
[7] Han X, Lin H , Zhou G , et al. FE simulation and experimentalresearch on cylindrical ring rolling[J]. Journal of MaterialsProcessing Technology, 2014,214(6):1245- 1258.
[8] Zhou P ,Zhang L, Gu S, et al. Mathematic modeling and FEsimulation of radial- axial ring rolling large L- section ring byshape axial roll [J]. The International Journal of AdvancedManufacturing Technology, 2014, 72(5):729- 738.
[9] 田笑,张恒,王恒强,等. 铝合金薄壁异形截面辗扩成形宏微观模拟[J].机械工程学报, 2021,57(12):1- 13.
[10] Liang L ,Guo L ,Liu Z,et al. On a precision forming criterion for groove- section profiled ring rolling process[J]. Journal of Materials Processing Technology, 2021, 296:117207.
[11] Meng J, Wang Q,Cai D M. Numerical Simulation on UpsettingProcess of Large Forgings [J]. Applied Mechanics andMaterials, 2013, 423:931- 934.
[12] 胡博奎,毛华杰,邓加东. 双列圆锥滚子轴承外圈成形工艺优化[J].热加工工艺, 2020,49(7):93- 97.
[13] 何松,华林,兰箭,等. 锥台复合截面环件精密轧制毛坯的优化设计方法[J].锻压技术, 2017, 08(42):59- 66.
[14] 陈孝庆,孟瑞斌,唐甲浪,等. 内台阶型环件径轴向辗轧技术[J].锻压技术, 2018,43(4): 94- 99.
[15] 王清,罗鸿飞,佟健,等. 2m 级大尺寸高温合金机匣精密成形工艺研究[J].精密成形工程, 2021, 13(01):121- 126.
[16] 邓加东,丁佐军,许亮,等. 大型外台阶环件近净轧制成形工艺:创新塑性加工技术,推动智能制造发展- - 第十五届全国塑性工程学会年会暨第七届全球华人塑性加工技术交流会 学术会议论文集[C].山东济南, 2017.
[17] 程瑞敏. 大型环件成形过程的数值模拟[D].河北: 燕山大学,2009.
[18] 石毅,刘红艳,刘晓娟,等. 一种间距可变式扩孔马架:中国,CN204524127U[P].2015- 08- 05.
[19] 张发廷,王晓娟. 推土机大齿圈锻件自由锻造工艺研究[J].锻压技术, 2010,35(03):22- 23.
[20] 曹繁,兰箭. 马架扩孔自动进给装置系列化参数化设计[J].锻压技术, 2020,45(09):148- 154.
[21] 郝用兴. 环件径向轧制动力学研究[D]. 武汉: 武汉理工大学, 2010.
[22] 华林.环件轧制理论和技术[M].北京:机械工业出版社, 2001.
[23] 耿剑,刘东,王凯,等.环件双向辗轧过程的力学分析与实验验证:2008 泛珠三角锻压年会[C].重庆,2008.
[24] 刘东,万自永,付明杰,等.径/ 轴双向轧制过程中环件的运动学分析[J].中国机械工程, 2008(04):91- 94.
[25] 郭良刚, 杨合, 金坚诚. 环件径轴向轧制毛坯尺寸设计方法[J].机械工程学报, 2010, 46(024):1- 9.
[26] Bono M,Limon R,Le Boulch D. Bulge formation during internalpressure testing of viscoplastic tubes,.InternationalJournal of Mechanical Sciences [J]. International Journal ofMechanical sciences,2018,144: 765- 774
[27] 王同海,孙胜. 管材胀形工艺分类及其变形力学特征[J].锻压技术, 1999,24(04):30- 32.
[28] Hai linHe,Youping Yi,Shiquan Huang. An improved processfor grain refinement of large 2219 Al alloy rings and itsinfluence on mechanical properties [J]. Journal of MaterialsScience&Technology,2019,35(01):55- 63.
[29] 肖石霞,郭扬. 大型风电轴承环成形方法探索[J].重型机械,2015(03):12- 15.
[30] 江道,易幼平,黄始全. 2A70 铝合金环件胀形强化微观机制的试验研究[J].热加工工艺, 2017,46(20):75- 78.
[31] 魏志坚,李金山,杨艳慧,等. 胀形对TC4 合金环锻件残余应力及分布的影响[J]. 稀有金属材料与工程, 2019,48(08):2537- 2543.
[32] 魏辉,兰箭. 铝合金异形截面大型环件胀形工艺及优化[J].锻压技术, 2020,45(08):94- 98.
[33] 华林,王华昌,赵仲治. 台阶截面环件轧制缺陷和对策[J].热加工工艺, 1995(05):20- 22.
[34] 徐戊矫,陈菲,谢丹,等. 基于截面填充的异形环件轧制毛坯及进给设计方法:创新塑性加工技术,推动智能制造发展- - 第十五届全国塑性工程学会年会暨第七届全球华人塑 性加工技术交流会学术会议论文集[C].山东济南, 2017.
[35] 王斌, 朱兴林,刘东,等. 斜I 截面异型环件轧制过程数值模拟[J].热加工工艺, 2013(07):141- 144.
[36] 黄建武,易幼平,黄始全,等. 深冷变形对2219 铝合金环件晶粒组织及性能的影响[J]. 材料导报, 2020,34 (14):14129- 14133.
[37] 尉潇健,齐会萍,李永堂,等. 离心铸造辗扩成形42CrMo 钢环件热处理后的组织与性能[J]. 金属热处理, 2016,41(12):25- 28.
[38] 胡向东,朱帅,甄小辉,等. GH141 高温合金矩形环件热处理工艺研究[J].热加工工艺, 2019,48(14):146- 149.
[39] 陈克宇.大型异形环件轧制过程及组织性能研究[D].江苏:江苏大学, 2019.
[40] 秦芳诚,齐会萍,李永堂,等. 铝合金环形零件形/ 性一体化制造技术[J].材料导报, 2021,35(09): 9049- 9058.
相关链接