引言
钛合金以其独特的机械性能、卓越的耐腐蚀能力和轻质特性在当今的材料领域中独树一帜。 然而,随着对钛合金的需求不断增加,传统的制备方法面临着诸多挑战,包括成本、复杂性和资源利用效率[1]。 粉末冶金技术应运而生,为制备钛合金提供了一个更为高效、灵活且经济的选择。 通过此方法,可以在微观层面上精确地控制钛合金的结构和性能,使其更好地满足各种应用的需求。 在此背景下,粉末冶金钛合金制备工艺及其性能变化成为一个关键的研究领域[2]。
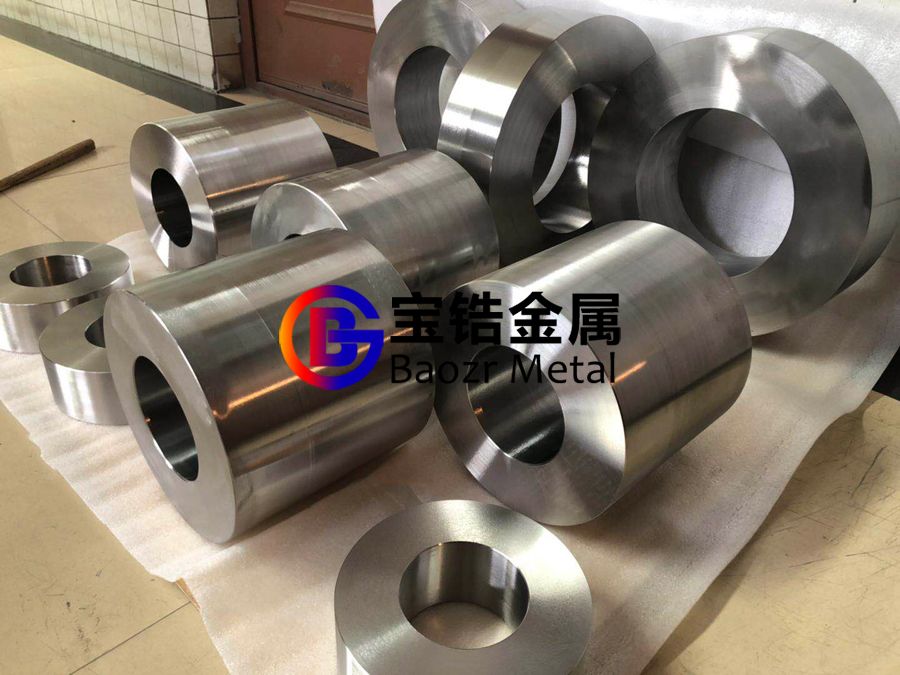
1、 粉末冶金钛合金制备工艺的性能分析
1.1 密度
密度在粉末冶金钛合金的性能中起到关键作用,直接反映了烧结后的材料孔隙度。 孔隙度高意味着材料内部存在更多的空隙,可能会导致材料的机械性能下降。 低密度的钛合金可能会表现出较低的抗拉强度和耐疲劳性。
密度还与材料的导热性、导电性和热膨胀系数等性能有关。 以上性能在一些特定的应用中,如航空航天和高温环境下的工作部件尤为重要。 从微观角度看,密度与烧结时粉末颗粒间的连接方式和强度密切相关。 良好的颗粒连接可以确保钛合金具有高的密度和均匀的微观结构,从而得到更好的综合性能。 密度也反映了烧结过程中可能存在的缺陷,如孔洞、夹杂和裂纹。 这些缺陷可能成为材料失效的起点,影响其使用寿命和可靠性。 因此,对于粉末冶金钛合金来说,密度高且均匀是制备工艺中的关键。
1.2 力学性能
在粉末冶金制备钛合金时,力学性能主要受烧结温度、压制密度、粉末类型及其粒度分布等因素影响。 烧结温度与颗粒之间的冶金学连接有关,适当的烧结温度可以确保钛合金粉末之间形成均匀且持久的连接,从而提高其抗拉强度和延伸率。 同时,过高的烧结温度可能导致过多的晶粒生长,进而影响到合金的屈服强度和硬度。 压制过程中的密度直接决定了烧结体的孔隙率,孔隙率与材料的抗弯、抗压和抗冲击性能密切相关。 较高的孔隙率可能使材料容易产生裂纹或断裂。 粉末类型和粒度分布决定了合金的显微结构,进而会影响到硬度、韧性和蠕变性能。例如,细小且均匀的粉末颗粒能够形成更为紧密的显微结构,从而增强材料的抗疲劳性。 只有全面深入地理解和控制各种影响力学性能的因素,才能确保制得的钛合金具有优异的综合性能。
1.3 耐腐蚀性能
钛合金的耐腐蚀性能主要来源于其在空气和水中迅速形成的致密、稳定的氧化膜,该氧化膜能够有效地隔绝材料与外部环境的接触,从而防止进一步的腐蚀。 在粉末冶金制备过程中,钛合金的耐腐蚀性能可能受到多种因素的影响。 烧结温度和时间对合金表面的氧化膜厚度和稳定性有直接影响。 适当的烧结条件可以确保形成均匀且连续的氧化膜。 粉末的纯度和孔隙率也会对耐腐蚀性能产生影响。 含有过多杂质的粉末可能导致在合金中形成微观缺陷,这些缺陷可能成为腐蚀的起始点。 而过高的孔隙率会增加腐蚀介质与材料内部的接触面积,从而加速腐蚀过程[3]。 合金的成分和微观组织也会对其耐腐蚀性能产生影响。 不同的合金元素及其分布状态可以改变钛合金的化学稳定性和电化学行为,从而影响其在特定环境中的耐腐蚀性。
1.4 生物相容性
粉末冶金钛合金由于其优异的生物相容性被认为是植入体材料的理想选择。 这种生物相容性的主要原因是钛合金表面能够形成稳定、连续的氧化钛膜,这一膜层对于分隔组织与材料、防止有害物质释放至体内发挥了关键作用。 而在粉末冶金制备过程中,钛合金的生物相容性可能受到多种因素的影响。 粉末的纯度和烧结条件对材料的微观结构和表面性质起决定性作用,这些因素直接关联到合金与生物组织之间的相互作用。 合金中的其他元素,如钒和铝,虽然可以增强钛合金的机械性能,但过量可能影响其生物相容性。 因此,选择合适的合金元素和其含量是至关重要的。 同时,孔隙率和孔径大小也会对生物相容性产生影响。 适当的孔隙结构可以促进组织的生长和附着,从而提高植入体与周围组织的结合强度。
2、粉末冶金钛合金的制备工艺
2.1 电解法
电解法是粉末冶金制备钛合金粉末的一种重要方法。此工艺的主要步骤如下:在一个特定的电解槽中添加适量的电解液,电解液通常选择为钛的盐溶液或其他有助于钛离子迁移的溶液。 电解槽中设置有阳极和阴极,其中阳极材料多为不溶性的导电材料如钛网或铂网,而阴极选择为可溶性的钛板。 当开始电解时,钛板(阴极) 上的钛会被氧化,形成钛离子。 钛离子在电场的作用下向阳极迁移,当钛离子到达阳极后,会被还原生成钛粉。 在此过程中,为确保粉末颗粒的形成与生长,需要精确控制电流密度、电解液的浓度、温度以及电解时间等参数。 电解过程结束后,需取出阳极,并对其上附着的钛粉进行收集。 随后,这些新生成的钛粉需要经过洗涤、干燥和筛分,以去除可能的杂质和调整粉末的颗粒大小。 对于需要特定颗粒形状或尺寸的应用,还需要进一步的机械或化学处理,以确保粉末的均匀性和质量。 电解法为制备高纯度、具有特定颗粒大小和形态的钛合金粉末提供了一种有效途径,但其效率和成果均取决于电解条件的精确控制。
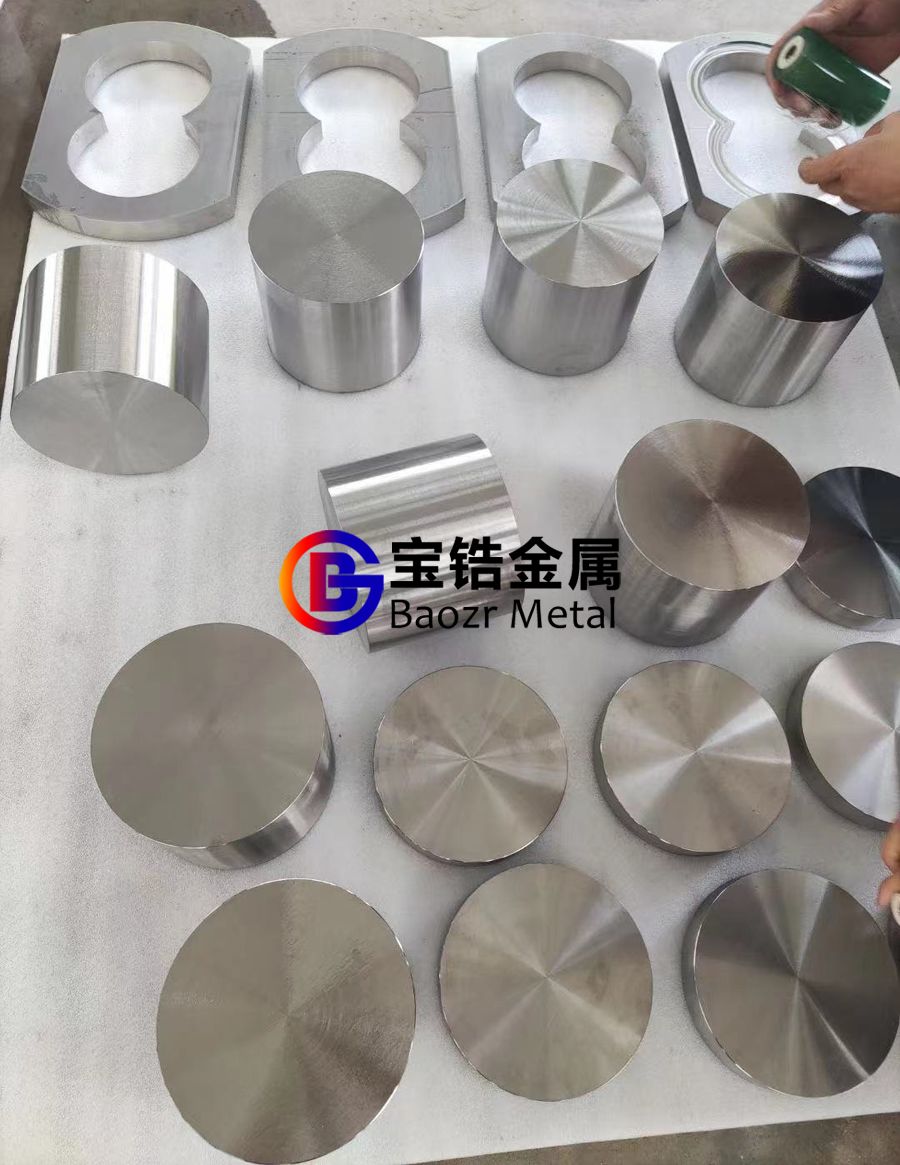
2.2 气氛还原法
气氛还原法是制备钛合金粉末的一种方法,主要通过在特定的气氛条件下将钛的化合物还原为钛金属或钛合金粉末。 此工艺的基本流程如下:首先,选择适当的钛化合物作为原料,常用的有钛酸盐、钛氧化物等。 该化合物需要经过预处理,如干燥、研磨,以得到均匀的颗粒分布和适当的粒度。 其次,将预处理后的钛化合物与还原剂混合均匀。 常用的还原剂包括氢气、氮气、氨气或其他能够与钛化合物反应生成钛金属的气体。 再次,混合物在设定的温度范围内在反应炉中进行加热。 在这一步骤中,选择的还原气体会与钛化合物反应,生成钛金属或钛合金粉末,并释放出相应的气体。 为保证反应的完整和均匀,需对反应温度、持续时间及气氛压力进行精确控制。 完成反应后,将产生的粉末从反应炉中取出,并进行冷却。 此时得到的钛合金粉末可能含有未反应的化合物和其他杂质。最后,钛合金粉末需要经过后处理,如洗涤、干燥、筛分和研磨,以得到纯净且具有所需颗粒大小分布的钛合金粉末。
2.3 机械合成法
机械合成法是利用机械力对金属粉末进行强烈研磨和混合,从而实现不同金属之间的合成。 在此方法中,先将所需的钛以及其他金属粉末,如铝、钒等,按照预定的配比称量。 再将这些金属粉末放入高能球磨机中,球磨机内部填充有硬质磨球,如钨钢球,用于提供足够的撞击和摩擦力以促进金属粉末之间的混合和扩散。 当机器启动后,金属粉末在磨球的连续撞击和摩擦作用下,其晶粒尺寸会逐渐减小,同时各种金属原子开始扩散、交换位置,从而形成合金。 整个研磨过程中,需要对研磨时间、速度和球与粉的比例进行控制,以确保获得均匀的合金组成。 研磨结束后,从球磨机中取出粉末,并进行筛分,以分离出超细的合金粉末。 超细粉末在高温下可以进一步进行烧结,得到致密的钛合金材料。 同时,钛合金粉末还需要进行其他后处理,如冷等静压、热压或热等静压,以提高致密性和改善微观结构。 最后,为确保得到的合金粉末具有一致的化学组成和物理性质,还需要对粉末进行化学分析和物性测试。
2.4 气体原子化法
气体原子化法是一种广泛应用于制备金属和合金粉末的技术。 在这一方法中,首先需要将钛合金熔融成液态,通常是在一个炉膛内,使用电弧或感应加热的方式进行。 当合金达到完全熔融状态后,通过专用的喷嘴以高速喷出。 与此同时,高纯度的惰性气体,如氩或氮,会被引入喷嘴附近,与高速流动的熔融金属接触。 在此过程中,气体的快速流动将熔融金属分散成无数细小的液滴。 液滴在迅速冷却和固化的过程中形成粉末颗粒。 为了控制得到的粉末的颗粒大小和形态,可以调整喷嘴的设计、熔融金属的喷射速度以及气体的流速和温度。 得到的钛合金粉末颗粒由于快速固化,通常具有很好的冷工硬化性和细小的晶粒尺寸。 收集粉末是下一步。 为了实现这一目的,原子化室的底部设置有一个收集器,用于捕获生成的粉末颗粒。 一旦收集完成,钛合金粉末通常需要经过筛分,以获得特定的颗粒大小分布。 此外,还可能进行其他的处理步骤,如去除可能存在的氧化物或其他杂质,确保粉末的高纯度和优良性能。
3、粉末冶金钛合金制备工艺的优化策略
3.1 电解优化法
电解优化法在钛合金粉末的制备中可以实现高纯度、细小粒径的钛合金粉末生产。 为了进一步提升电解过程的效率和粉末品质,可以进行细致的优化[4]。 首先,适当选择和调整电解液的组成可以提高电解效率,减少杂质的生成,并优化粉末的颗粒形状和尺寸。 例如,采用有机酸或特定的盐作为电解液中的添加剂,可以有效地调节电解过程中的电流密度和粉末生成速率。 其次,电极材料和结构的选择也将影响电解效果。 使用高导电性和化学稳定性的电极材料,如钛合金或其他耐腐蚀材料,可以确保电解过程的稳定进行。 同时,电极的表面形态,如微孔结构或特定的表面涂层,也可能增强电解反应的活性区域,进而提高粉末生成的均匀性和效率。 再次,控制电解参数是另一个关键环节。 电流密度、电压和电解时间的适当控制可以有效地调整粉末的生成速率、颗粒大小和形态。 例如,低电流密度可能促进细小颗粒的生成,而高电流密度可能导致粗大颗粒或团聚。 最后,电解过程中的搅拌和循环是不可忽视的环节。 通过强化电解液的搅拌和循环,可以确保电解液中物质的均匀分布,减少局部过热或饱和,从而获得均匀的钛合金粉末。
3.2 气氛还原优化法
气氛还原法在制备钛合金粉末中的应用相对成熟,但为了满足更高的品质要求和更高的生产效率,仍需要从以下几步进行持续的优化。 第一,应选用适当的还原气体。惰性气体如氩或氮可以防止粉末氧化,而氢气可以提供更强的还原能力,但用量和纯度需要仔细控制,以防止过度还原或引入不必要的杂质。 第二,对于还原炉的设计,确保均匀的气氛流动和有效的热传递是关键。 炉内的气氛流速和流向应当能够确保整个反应区域内的均匀气氛,并且能够迅速带走反应产生的副产物,如水蒸气。 同时,炉的隔热设计也应进行优化,以确保炉内的温度稳定并降低能源消耗。 第三,应做好还原反应的温度和时间控制。 不同的温度和时间条件会对粉末的晶粒大小、形态和纯度产生显著影响。 通常较高的反应温度和较长的反应时间有助于提高还原效率,但也可能导致粉末的颗粒增大或结构变粗。 第四,应重视原料粉末的初步处理。 例如,通过物理或化学方法对原料粉末进行预处理,如球磨或表面活化,可以提高其与还原气体的接触效率,从而提高整体的还原效果。 第五,在整个优化过程中,实时监控和数据分析也是必不可少的环节。 通过高精度的传感器和数据处理系统,可以实时监测炉内的温度、气氛成分和压力等关键参数,并据此进行快速调整,以确保最佳的还原效果。
3.3 机械合成优化法
在机械合成法中,为提高钛合金粉末的质量和产量,对传统工艺进行适应性调整是至关重要的。 在球磨过程中,球材选择、球粉比、转速以及磨球的大小都会影响最终的粉末性能。 第一,适当选择硬质合金或陶瓷为球材可以减少金属污染,而调整球粉比可以影响粉末的细化效果和产率。 对转速的控制不仅关系到粉末的细化程度,还涉及到能量的输入和效率。 对于磨料选择,适当增加小直径的磨球可以提高碰撞次数,使钛合金粉末更容易细化,结合大直径的磨球则可以提高球磨的处理量。 第二,润滑剂或工艺控制剂的添加是一个值得探索的方向,适量的添加不仅可以减少粉末的热量累积,防止粉末过度氧化,还可以避免粉末在磨罐内的黏附。 第三,考虑到磨粉过程中可能产生的温度上升,冷却系统的设计不容忽视。 一个有效的冷却系统可以避免过高的温度对粉末产生不良影响,如晶粒长大或相变。 第四,磨粉时间对于粉末的细化和均匀性同样至关重要,过短的时间可能导致粉末的细化不足,而过长则可能导致过度细化和能源浪费。 因此,通过对机械合成法中各个环节的细致调控,不仅能够获得高质量的钛合金粉末,还可以提高生产效率和经济效益。
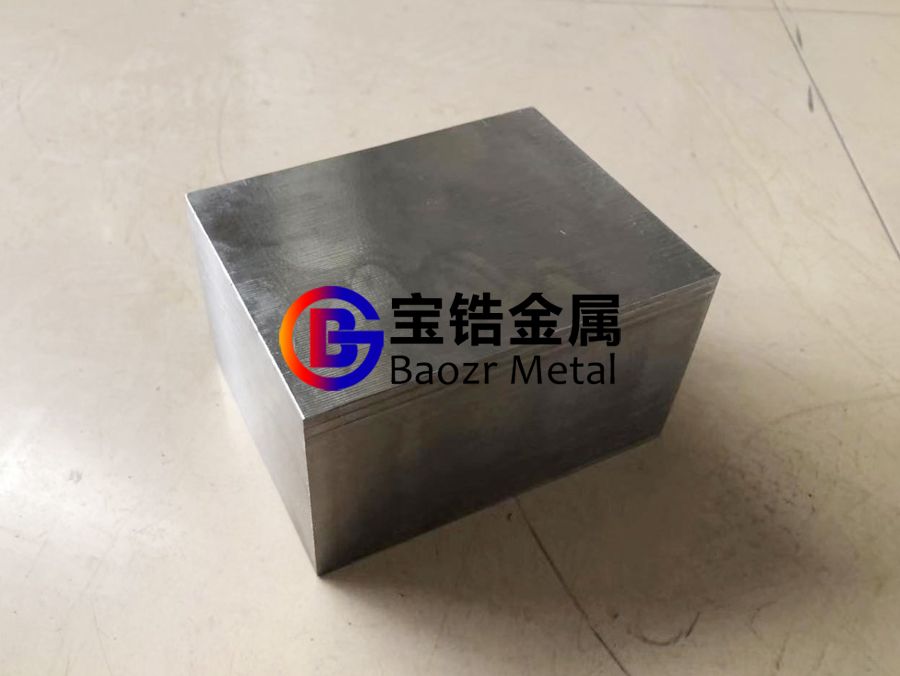
3.4 气体原子化优化法
气体原子化法作为一种先进的制备钛合金粉末的方法,优化其工艺可以提高粉末质量和降低成本。 首先,液态金属的流动性和温度对原子化效果有显著影响,通过精确控制喷嘴温度和液态金属注入速率,可以有效改善液滴的形态,从而获得更均匀、更细小的金属粉末颗粒。 其次,气体的种类、纯度和流量也是决定因素,采用高纯度气体并确保其稳定流动有助于减少粉末中的氧化物和夹杂物。同时,通过调整气体的流速和喷嘴与液滴的相对位置,可以影响液滴的冷却速率和形态。 再次,可对喷嘴的结构和形状进行改进。 根据流体动力学原理,喷嘴的结构将直接影响到液滴的形成,合理的喷嘴设计可以进一步优化液滴尺寸和分布,从而获得更为理想的粉末特性。 最后在收集粉末时,考虑到钛合金的活性,采取惰性气氛保护如氩气或氮气,可防止粉末在收集过程中的二次氧化。 总之,通过对气体原子化法中各个环节的精细调控,可以进一步提升钛合金粉末的性能和产量,为后续的粉末冶金制品制备提供更为优质的原材料[5-6]。
4、结语
综上所述,本文通过对粉末冶金钛合金制备工艺进行深入探讨,发现在该领域中的技术进步与创新对推动材料科学的发展起到了关键作用。 选择合适的制备方法,结合针对性的优化策略,能够在保证钛合金性能的同时,实现工艺的高效与经济。 未来随着技术的不断进步和应用需求的增长,钛合金的粉末冶金制备工艺将得到更多的研究和探索,为各种先进应用提供更为优质的材料支持。
【参考文献】
[1] 杨芳,李延丽,申承秀,等. 钛及钛合金粉末制备与成形工艺研究进展[J]. 粉末冶金技术,2023,41(4):330-337.
[2] 岳小童. 粉末冶金钛合金制备与研究[ J]. 居业,2023,15(4):215-218.
[3] 冯可华,杜宁,章若晨,等. 粉末冶金工艺钛合金材料对药型罩破甲性能的影响[J]. 兵器装备工程学报,2022,43(8):112-116.
[4] 郭学益,董朝望,夏阳,等. 镁还原高钛渣直接制备钛合金粉的工艺研究[J]. 稀有金属,2021,45(12):1464-1471.
[5] 曾克里,罗浩,朱杰,等. 丝材等离子雾化钛合金粉末研究进展[J]. 粉末冶金工业,2021,31(6):1-12.
[6] 郭佳明,梁精龙,沈海涛,等. 生物医用钛合金材料制备方法及应用进展[J]. 热加工工艺,2021,50(20):30-34.
相关链接