前言
在核燃料元件制造中,端塞焊是最关键的工艺之一,因为燃料芯块是在这个过程中被密封在包壳管内,从而形成完整的、保证反应堆安全的第一道屏障。端塞焊工艺属于压力焊中的电阻对焊,它将端塞与包壳管装配成对接接头(图1),使其端面紧密接触并通过电流,利用电流流经工件接触面及邻近区域产生的电阻热将其加热到塑性状态,同时迅速施加顶锻力,接头部分在压力和热量联合作用下,通过再结晶、扩散作用而达到原子间的连接,形成金属结合。
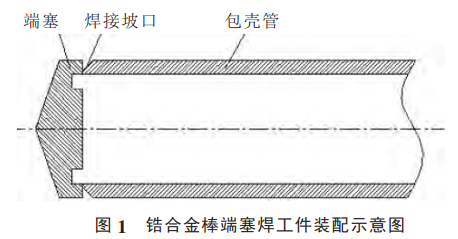
通过对产生焊接缺陷的锆合金棒进行分类统计,存在“电弧痕”的锆合金棒占比约50%。锆合金棒端塞焊后,在其焊缝或其附近区域出现被电弧灼烧过的痕迹,称之为“电弧痕”,其形貌如图2所示。“电弧痕”是否能对焊缝内部质量造成影响,是否是内部质量不良而在外观体现出的特征信号,这些并不明确。本文对产生“电弧痕”的锆合金棒进行各种性能试验,对“电弧痕”与焊缝内在质量的关系进行研究,以期采取措施,提高产品质量。
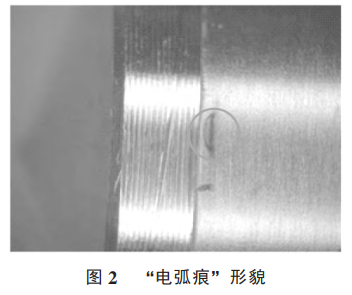
1、试验方法
将100根直径为准10mm存在“电弧痕”的Zr-4合金棒作为试验样品,然后根据“电弧痕”的长度和在锆合金棒上出现的位置对其进行定性分类。对样品进行外观检查、内在质量检查(金相解剖)、强度检查(拉伸和爆破试验)以及抗腐蚀性检查(腐蚀试验),以确定“电弧痕”对焊接质量的影响程度。
1.1样品定性分类
将长度>2mm的电弧痕定义为“较大电弧痕”,长度在1~2mm之间的定义为“中等电弧痕”,长度<1mm的定义为“较小电弧痕”。然后根据电弧痕是否与焊缝相连对试验样品进行分类试验,具体分类情况与数量见表1,电弧痕的宏观照片分别如图3~图8所示。
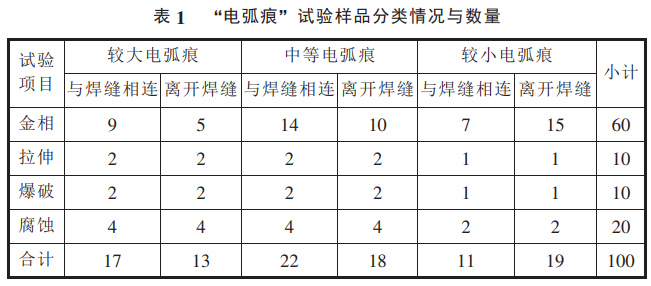
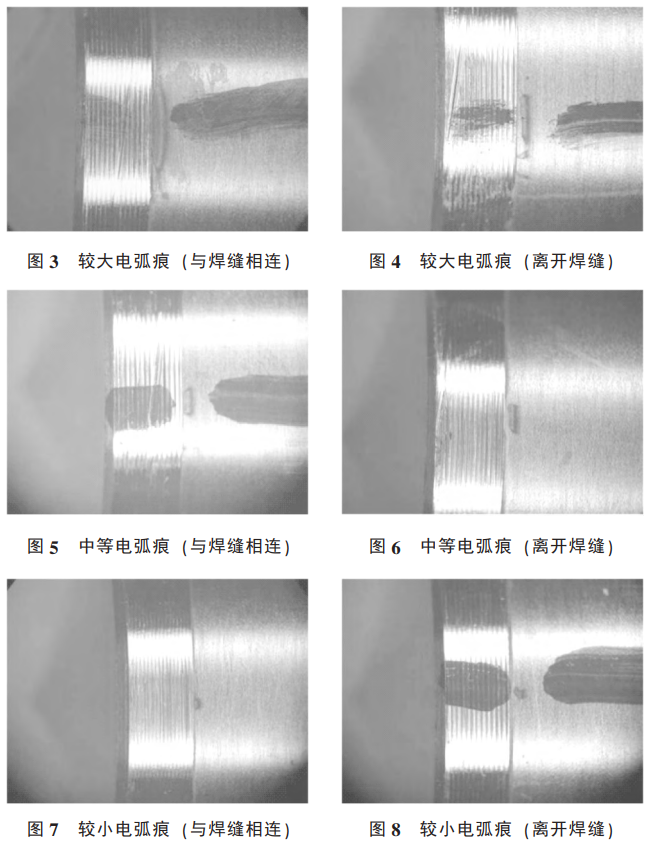
将分类后的试验样品先使用丙酮进行擦拭,然后在电弧痕出现的附近用箭头进行标识,并在样品上写明样品编号。最后按电弧痕分类和试验项目将样品分别装入样品袋,在样品袋上写明样品名称、编号和检测项目,送往检测中心进行各项试验。
1.2金相试样的制备与检验
接头金相试样取样的主要原则是:保证取样过程不能有任何变形、受热和使接头内部缺陷扩展和失真的情况,这是确保金相分析结果准确、可靠的重要条件[1]。制备与检验的主要流程为:内表面宏观取样→切割锯切割→磨制→化学抛光→金相试样检验。最后用金相显微镜观察接头各部分金相组织的变化情况以及内部缺陷情况,将获得的照片和数据进行记录和统计。
1.3拉伸试验
使用100kN万能材料试验机在室温下进行试验,制造专用工装夹持端塞和包壳管。
1.4爆破试验
使用200MPa爆破试验机在室温下进行试验,压力介质为去离子水。
1.5腐蚀试验
在(360±10)℃,(19±1)MPa的高压釜中进行72h的水腐试验。
2、试验结果与分析
2.1微观金相检测结果
锆合金棒端塞焊接头解剖后经过微观金相检测,所有金相样品均未发现未焊透、裂纹、夹杂等内部缺陷,金相检测全部合格,其金相照片如图9所示。
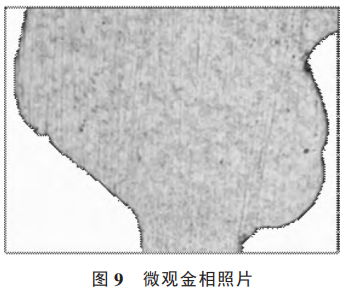
2.2拉伸试验检测结果
锆合金棒拉伸试验合格判定的标准为:在端塞焊缝区发生断裂判为不合格,在其他部位发生断裂判为合格。试验结果显示:所有试验样品均在非焊缝区发生了断裂,拉伸试验全部合格,经过拉伸试验后样品的宏观形貌如图10所示。
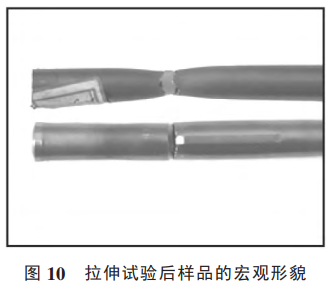
2.3爆破试验检测结果
锆合金棒爆破试验合格判定的标准为:在端塞焊缝区发生破裂判为不合格,在其他部位发生破裂判为合格。试验结果显示:所有试验样品均在非焊缝区产生了破裂,爆破试验全部合格,经过爆破试验后样品的宏观形貌如图11所示。
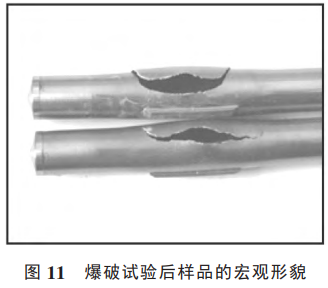
2.4腐蚀试验检测结果
锆合金棒腐蚀试验合格判定的标准为:焊缝区表面呈均匀、致密、连续的灰黑色氧化膜判为合格。
试验结果显示:所有试验样品均在焊缝区表面产生了均匀、致密、连续的灰黑色氧化膜,腐蚀试验全部合格。经过腐蚀试验后样品的宏观形貌如图12所示,图12中上面的样品是没有电弧痕的,下面的样品是有电弧痕的。从图12可看出,有电弧痕和无电弧痕的样品焊缝区外观形貌相同。
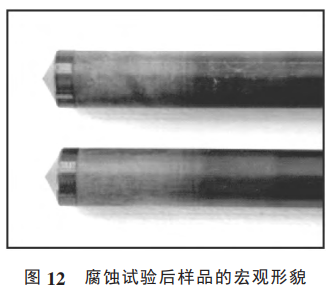
由以上各项试验检测结果可以看出,“电弧痕”没有对焊缝内部组织产生影响,也没有明显降低焊缝的强度,表面耐腐蚀性也满足要求。
2.5原因分析
本试验中焊接方法采用的是压力焊中的电阻对焊,电阻焊的热源是电阻热。由电工学可知,电流通过导体时,导体将吸热,其温度会升高,这是因为导体电阻吸收电能转换为热能的缘故,这种现象成为电流的热效应。同样,电阻焊时,当焊接电流通过两极间的金属区域焊接区时,由于焊接区具有电阻亦会吸热,并在焊件内部形成内部热源。根据焦耳定律,焊接区的总吸热量[2]:
Q=I2Rt,(1)
式中:I为焊接电流的有效值;R为焊接区总电阻的平均值;t为通过焊接电流的时间。
由于在电阻焊过程中,焊接电流和焊接区电阻并非保持不变,因此焊接热源总吸热量Q的确切表达式为:

式中:i为焊接电流的瞬时值,是时间的函数;r为焊接区总电阻的动态电阻值,是时间的函数;t为通过焊接电流的时间。
对于对焊,由于夹钳电极对焊件的夹紧力很大,所以电极与焊件间的接触电阻很小,可忽略不计。
焊接热源总吸热量Q还可以写成:

式中:rc为焊件间接触电阻的动态电阻值,是时间的函数;rw为焊件内部电阻的动态电阻值,是时间的函数。
由此可知,电阻焊的热源是电阻热。产生电阻热的内在因素是电阻,外部因素是电流和时间,他们的变化对焊缝的成形起决定性作用。焊接时,由于焊件即包壳管的坡口清洁程度不够或几何尺寸达不到要求,导致他们与端塞之间即工件间的接触电阻rc发生了变化。另外,电极的氧化膜清理不够或几何尺寸随着磨损而变化导致焊接电流i发生了变化,而工件本身和焊接设定时间没有发生变化即t和rw没有影响。由此可以判定,接触电阻rc和焊接电流i是影响焊接热源的主要因素,即影响焊接成形质量的主要因素,二者可以单独作用也可以交互作用。
该锆合金棒制造多年,焊接工艺成熟稳定,均进行了工艺合格性鉴定。焊接工艺一经合格性鉴定,将保持相对稳定,不会随意改动工艺参数。由于套爪(电极)与包壳管坡口表面存在异物、包壳管坡口存在损伤或夹持包壳管的套爪接触部位发生磨损变形,导致电极和焊接件间不能够完全贴紧即产生了间隙,从而引起接触电阻rc发生了变化。焊接时热量分布不均匀,产生局部过热、过烧现象,这样在焊缝的外表面或其附近区域就形成了灼伤的电弧印记,即“电弧痕”。所以,套爪与包壳管坡口表面存在异物、包壳管坡口存在损伤及套爪磨损变形是导致锆合金棒端塞焊产生“电弧痕”的主要因素。
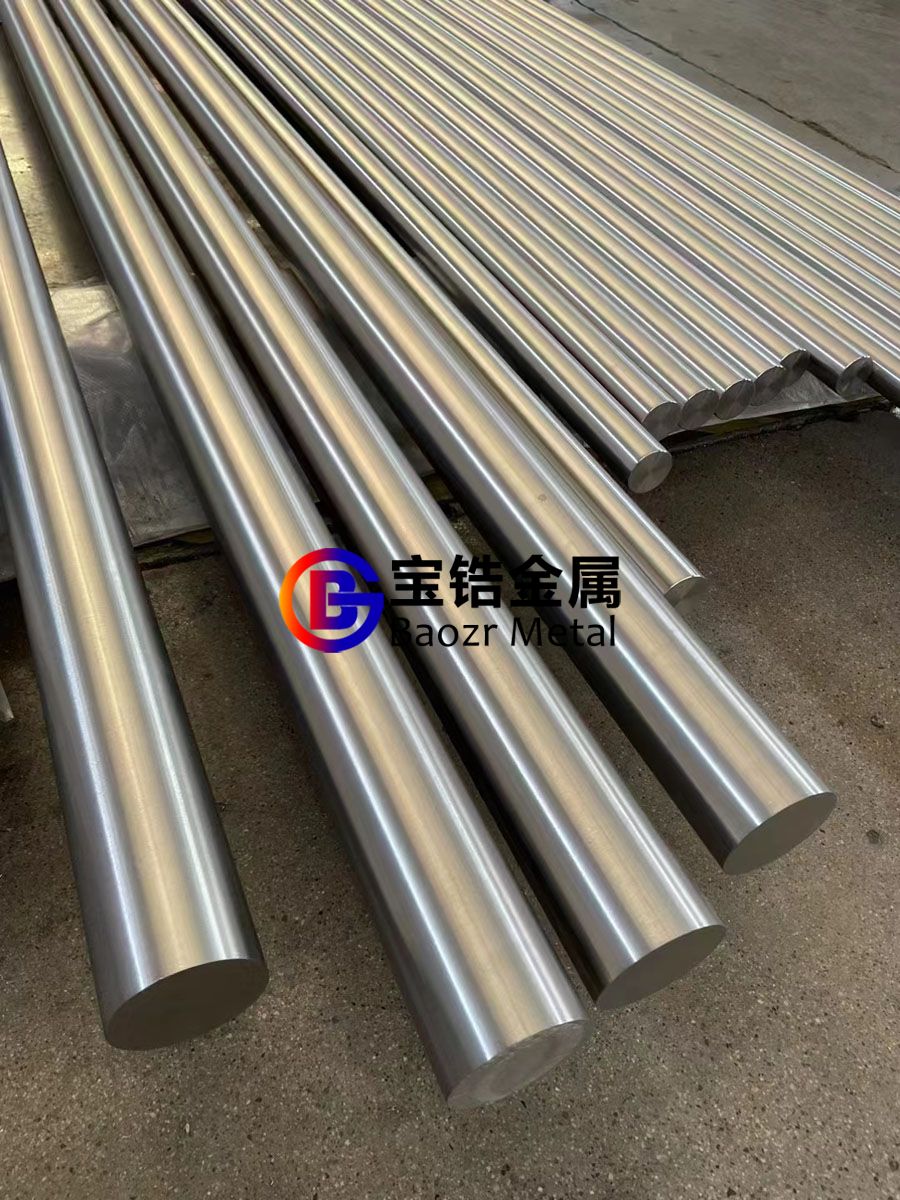
经试验和分析,为了防止“电弧痕”的产生,焊接人员应采取以下质量控制措施:①在施焊前仔细检查包壳管的坡口质量,是否存在异物和损伤,如发现异物,则返回到清洗工位进行重新清洗;如发现有损伤,需进行隔离报废,更换质量合格的包壳管进行焊接;②对套爪定期进行清理、更换。
3、结论
(1)“电弧痕”不是焊缝内部质量不良的外部表征,是焊接区外表面的损伤,对焊接质量尤其是焊缝强度和耐腐蚀性基本上没有影响。
(2)套爪与包壳管坡口表面存在异物、包壳管坡口存在损伤以及套爪磨损变形是产生“电弧痕”
的主要因素。
参考文献:
[1]赵熹华.焊接检验[M].北京:机械工业出版社,1993.
[2]赵熹华.压力焊[M].北京:机械工业出版社,1990.
作者简介:田红雨(1980—),男,内蒙古包头市人,硕士,工程师,从事核燃料元件焊接工艺研究与质量管理工作.
相关链接