引言
锆在元素周期表中处于第40位,属于Ⅳ-B族,是一种十分活跃的金属,其表面呈银白色,密度为6.51g/cm3,熔点为1852℃。锆具有很高的活性,但是在常温下它的化学性质却很稳定。这是因为纯锆的表面原子与氧作用生成一层紧密排布的ZrO2薄膜,对其内部起到了保护作用,而且这层氧化膜还使得锆及其合金具备了优良的耐腐蚀性能。除此之外,它还具有许多优异的特性,如密度较小,属于轻金属;具备良好的强度和塑性匹配以及较小的弹性模量,力学性能优于常见的钢材;热中子吸收截面小;热膨胀系数低;对人体无害、生物兼容性好;还具有储氢等特殊功能。因此,锆及其合金被广泛应用于如阀门、耐蚀反应塔、热电偶套管、坩埚、导管、耐酸耐热泵、搅拌器、喷嘴等化工设备中[1-22]。锆的物理性能和力学性能如表l所示[3]。
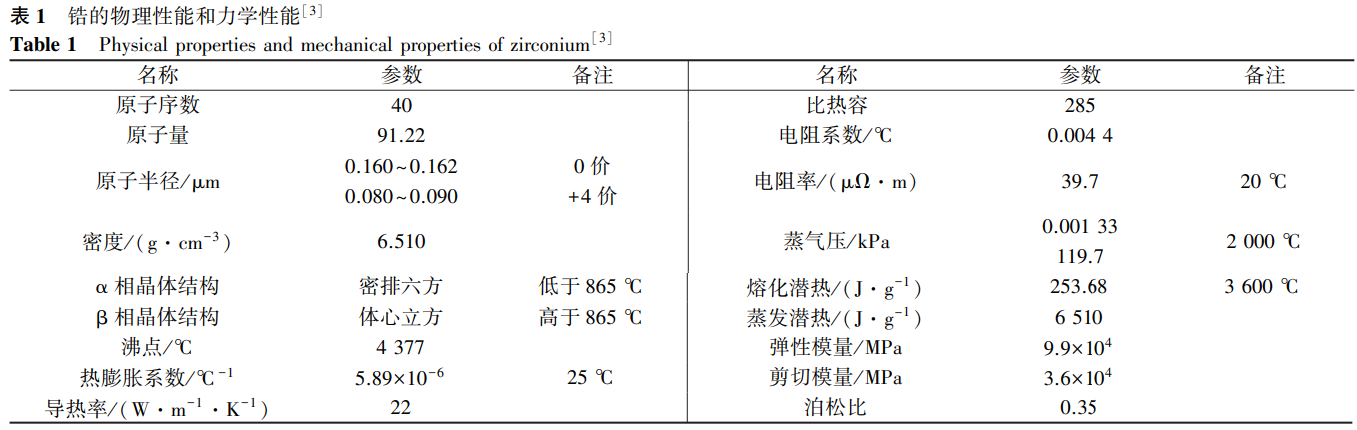
锆及锆合金在核工业领域的应用程度非常高,它常被制成优秀的核反应堆结构材料、核燃料包壳材料和强耐蚀结构材料等。目前,锆材大部分用于水冷核反应堆,因此其第二大应用领域为化学处理工业。另外,锆及锆合金铸件还可用于兵器、生物医学、农业、冶金、石油化工、造纸等工业[3]。
图1展示了几种锆及锆合金铸件。
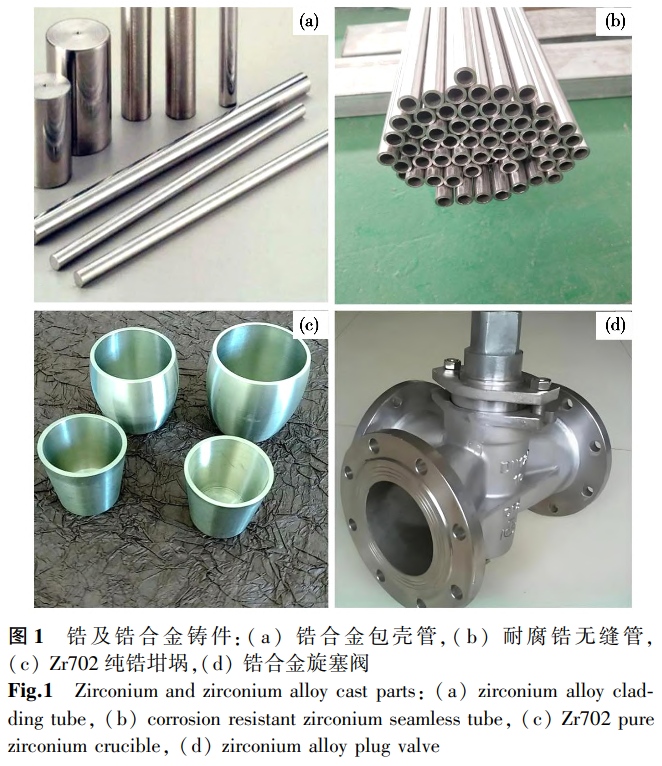
1、锆及锆合金的研究历程
德国化学家马丁.海因里希.克拉普罗斯于1789年首次发现了锆元素。1824年,瑞典化学家乔斯.雅各布.布雷泽利乌斯通过在铁管中混合加热钾和氟化锆,在实验室中分离出这种金属。直到1925年,荷兰化学家A.E.vanArkel和J.H.deBoer才发明了一种碘化物工艺来热分解四碘化锆,并生产出更纯的金属锆。这种韧性金属被称为碘化金属或晶体棒,具有良好的延展性,可以冷加工。当时,大多数生产的金属用于电子工业的吸气和真空管部件,但工艺昂贵,供应有限。到1948年,只有几吨被用于工业生产中。20世纪40年代末,美国率先研究了锆在水冷反应堆中的应用,之后俄罗斯、法国、德国等国自20世纪50年代起先后研发出一系列锆合金。1951年,美国科研人员通过利用Sn元素吸收锆合金中的有害元素,研发出了Zr-2.5Sn合金,即Zr-1合金,然后调整元素组成研制出具有优良综合性能的Zr-2合金,并用作世界第一艘核潜艇的核燃料包壳材料,后来又加以改进研制出Zr-4合金,一直沿用至今[4]。为了解决Sn元素含量较高导致锆合金耐腐蚀能力无法进一步提高的问题,随着冶炼技术的提高,人们通过控制Sn元素含量并提高其中的铁和铬的含量对Zr-4合金进行了改进。此外,Zr-Nb系合金也得到了世界各国的关注,如加拿大开发了Zr-2.5Nb合金[5],前苏联研制了E110等系列锆镍合金[6]。近年来,随着工业化的发展和技术水平的提高,各种高性能新型锆合金也不断被研发出来,如美国的Zirlo合金[7]、日本的抗腐蚀新合金(NDA)[8]、前苏联的E635合金[9]、法国的M5合金[10]等。新型锆合金的研发历程如图2所示[11]。
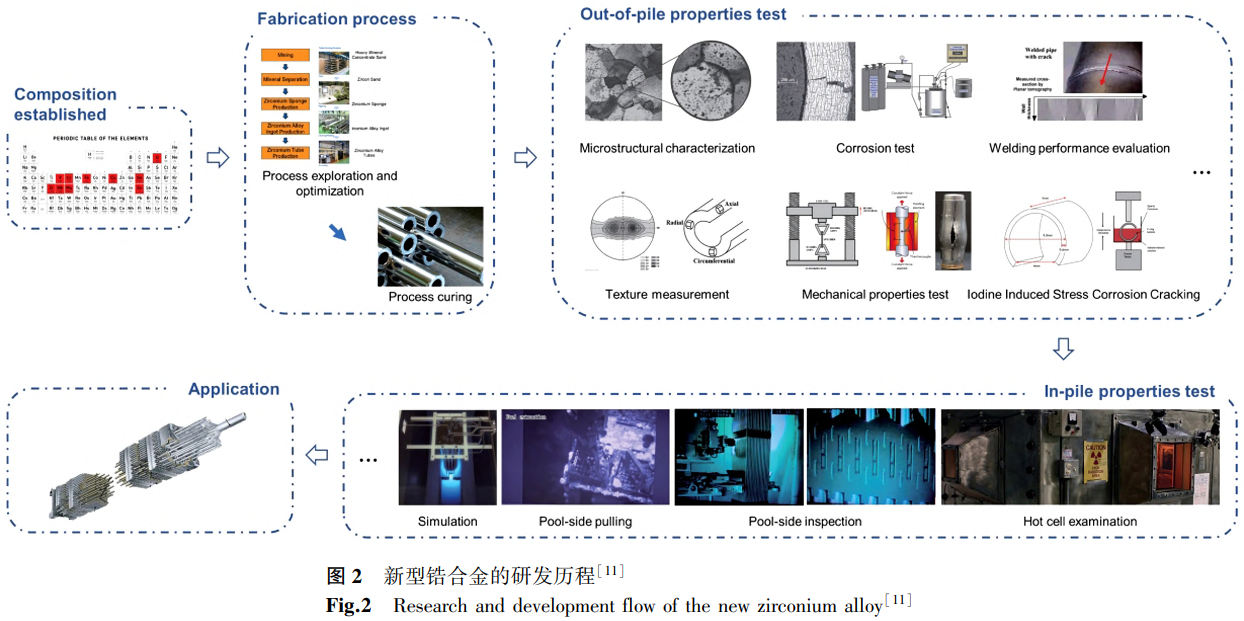
我国对锆合金的研究起步于20世纪60年代,起初只是为了满足国家核工业发展的需求,直到20世纪90年代至21世纪初,才开发出更多性能优良、功能各异并具有自主产权的铸造锆合金,而且逐步形成商业化,具备了一定的规模。
近年来,国内建立了众多具备锆合金铸件生产能力的企业,如国核宝钛锆业、中核晶环锆业、洛阳精铸钛业、中国广核集团、沈阳铸造研究所、东方锆业等。华龙一号是我国自主研发的先进百万千瓦级压水堆核电技术,在2021年建成并投入使用,其中的燃料包壳管使用的是我国自主研制的N36锆合金,标志着我国的核用锆合金制造技术已经跻身世界前列[12-13]。图3为N36锆合金包壳管。
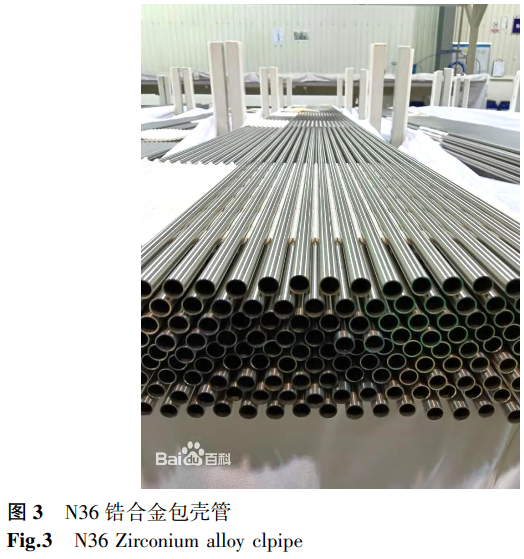
虽然我国锆及锆合金的研究与生产已经在一定程度上实现了自主化,但是在更高端领域的研究仍受到国外的牵制与封锁,因此我国应在已有成果的基础上加大力度发展具有自主知识产权的新型锆合金。
2、锆及锆合金铸造工艺及成型技术
锆及锆合金铸造的成功与否和铸件质量的好坏关键在于熔炼技术和造型工艺的选择。在工业生产中,锆及锆合金的熔炼技术与造型工艺主要包括以下几种。
2.1 锆及锆合金的熔炼技术
锆与钛同为元素周期表第Ⅳ-B族元素,其活性甚至比钛更高,在高温下容易与多数物质发生反应。而且,高温状态下的锆还具有极强的吸气能力,因此锆及锆合金必须在真空或者惰性气体气氛中才能够进行熔炼以及浇铸。目前,真空自耗电极电弧凝壳熔炼技术和真空感应凝壳熔炼技术是锆和锆合金工业生产的主要方法。
2.1.1 真空自耗电极电弧凝壳熔炼技术
真空自耗电极电弧凝壳熔炼技术的原理为使用被熔炼金属制成的自耗电极作阴极、结晶器座作阳极,利用自耗电极和结晶器座两极间的电弧放电产生的高温将电极熔化,熔化后在真空或惰性气体中重新熔炼,在坩埚中形成熔池,铸锭在结晶器中逐渐凝固[14]。真空自耗电极电弧凝壳熔炼技术在熔炼时能够有效去除氢等气体,降低高蒸气压微量元素的含量,还能降低宏观偏析和微观偏析。综上,该技术具备众多优点,是锆及锆合金熔炼使用最广泛的方法。
2.1.2 真空感应凝壳熔炼技术
真空感应凝壳熔炼技术是一种在真空或保护气体气氛下,在分片式水冷铜容器内利用感应线圈产生的磁场加热金属进行熔炼的方法。该方法还可以利用磁场对金属液进行搅拌,保证温度均匀。分片式的设计也减少了热量的损失。
这种技术由于启用较晚,发展缓慢,目前还未被大范围地使用,只有少数企业或厂家在使用真空感应熔炼炉。
2.2 锆及锆合金的造型工艺
铸型材料的选择也是锆及锆合金铸造成型的重要一环,锆的活跃性导致其能与市面上许多耐火材料发生界面反应,因此选择合适的铸型材料和面层材料是锆及锆合金铸造是否成功的关键因素之一。在实验室研究和工业生产制备中,锆及锆合金的铸造方式根据造型工艺不同主要分为硬模铸造、砂型铸造和熔模铸造三种类型。
2.2.1 硬模铸造
硬模铸造主要包括金属型铸造和石墨型铸造,它是将液体金属浇入金属铸型或石墨铸型,经过降温凝固后获得金属铸件的铸造方法。其优点为模具加工简单、铸型可以反复使用多次、生产效率高等,缺点为只适用于结构简单的铸件。
目前可用作铸型材料的金属主要包括铸铁、铸钢、铸铜以及部分难熔金属,其主要物理性能见表2[15]。
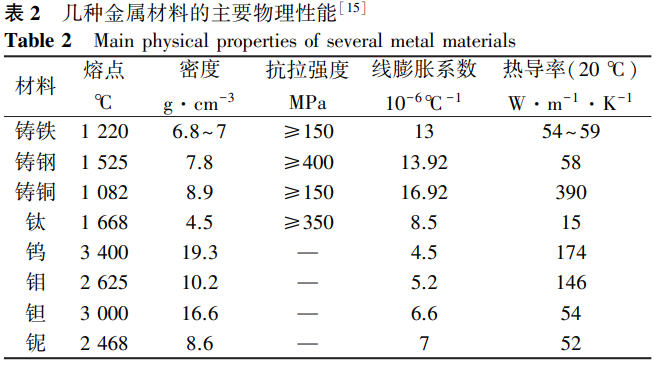
对比锆及锆合金的物理性能可以看出,其熔点要高于铸铁、铸钢、铸铜这些金属,但它们仍能用作锆及锆合金的铸型材料。主要是因为与锆相比,这些金属的热导率都很高,在金属锆熔液与铸型材料接触时,最外层热量率先被传走,而内层的热量还未传递到铸型上面,这使得铸型不会一次性接收过高的温度而被熔化;此外,锆熔体因其热导率较低,在与铸型接触后会在型面迅速形成一层固态薄层,大大减少其与铸型的热作用。谢华生等[16]发明了一种在金属铸型的内表面涂耐高温涂料的方法,耐高温涂料是由55%~70%(质量分数,下同)耐火粉料、30%~45%粘结剂、0.1%~1%表面活性剂和0.1%~1%消泡剂制成,其中耐火粉料由Y2O3和ZrO2粉中至少一种组成,该方法简便高效,其生产的铸型具备10~15次的使用寿命,生产效率较高。
相较于石墨型铸造,金属型铸造的成本更高且寿命更短,因此锆及锆合金的硬模铸造工艺还是以石墨铸型为主。实际生产中对于石墨的要求是高纯度(99.0%)、完全石墨化的人造石墨电极块。对于大型铸件,由于充型时间长、冷却速度慢,表面冷隔和流痕等缺陷出现的几率较高。为了解决这些问题,刘升迁[17]提出了一种用于铸造大型锆及锆合金零部件的方法,具体步骤包括准备石墨模具、配制陶瓷涂层、涂刷涂层到模芯表面、固化和真空除气,最终在真空自耗电极电弧熔炼炉中熔化并浇铸材料。这种方法适用于500kg以上的大型锆及锆合金铸件,可实现表面平整、无瑕且污染层厚度小的铸造。刘健[18]也公开了一种锆或锆合金铸件的铸造方法,其主要原理为对锆或锆合金进行两次熔炼,第一次熔炼浇铸出海绵锆和锆合金的铸锭,第二次熔炼铸锭浇铸锆或锆合金的铸件。相较于现有方法,该方法能够节约时间和成本,制备质量更大的铸件,还能保证型的强度。
2.2.2 砂型铸造
砂型铸造是一种应用广泛的铸造方式,是青铜、黄铜、铸钢、铸铁等金属的主要铸造方式。砂型铸造同样也适用于锆及锆合金铸造,工艺流程也与上述金属相似,唯一的不同是为了防止锆金属液与型砂发生反应,避免型砂脱落影响铸件品质,在造型造芯完成后需要在型壳和型芯表面涂覆一层氧化物涂层。在造型完成后还需将砂型进行高温煅烧去除多余气体,可以保证浇铸后的锆合金铸件不容易产生气孔。虽然这种砂型铸造方法可塑性高,适用度广,而且因其导热慢有效减少了铸件表面冷隔等缺陷的出现,但其铸造出的铸件精度远远不如硬模铸造和熔模铸造,在工业生产中的使用频率并不高,相关学术研究也很少。
黄湘云等[19]公开了钛、锆、镍及其合金铸件砂型铸造工艺,其方法为利用铝矾土、硅酸盐粉等制备型砂,然后根据铸造工艺图纸制作模具,耐火涂料按照30%~40%的粘结剂、60%~75%的氧化钇或氧化锆或钨粉、0.5%~1%的润湿剂和0.1%~0.5%的消泡剂进行配制,将铸型预热至60~100℃后在其与金属液直接接触的表面喷涂耐火材料,然后进行高温煅烧,最终放入真空电极自耗凝壳炉内熔炼浇铸。该方法能够大规模生产出各种大小的铸件,铸件表面平整光滑,经检测不存在流痕、冷隔、裂纹等缺陷,铸件内部也未发现缩孔、夹杂等缺陷。
2.2.3 熔模铸造
熔模铸造又被称为精密铸造、失蜡铸造,因可以铸造出结构复杂的铸件,且成型后的铸件具有极高的尺寸精度和表面光洁度,非常适合锆及锆合金铸件的制备。由于在浇铸时型腔内耐火材料直接与金属液接触,锆及锆合金熔体不与型壳材料发生反应是保证铸件质量的关键因素之一。因此,选择合适的耐火材料在一定程度上决定了铸件的最终品质。
熔模铸造耐火材料的选择主要看其是否耐高温、是否与锆及锆合金熔体发生反应、是否容易加工,还要考虑其成本、工艺难易程度等条件。目前,可用于锆及锆合金熔模精密铸造的耐火材料主要有石墨、难熔金属、难熔化合物、氧化物等[20]。
石墨是一种热稳定性较高的材料,在高温下通常不易与锆及锆合金发生反应,但其热导率高,作为面层材料容易发生激冷,易使铸件表面产生微裂纹、冷隔等缺陷。在熔模铸造时,将石墨粉与硅溶胶、合成树脂等有机或无机粘结剂混合烧制成型壳,该型壳比硬模铸造中的石墨铸型退让性好、导热性差[21-23]。另外,C元素会影响合金的耐腐蚀性能,因此一般不使用石墨作为锆合金熔模铸造的型壳材料。
难熔金属Mo、Ta、Nb、W等具有较高熔点和高稳定性,可用于制作锆及锆合金熔模铸造的型壳面层。目前只有金属钨被用于生产面层材料,使用钨粉混以粘结剂涂于陶瓷壳表面,然后在还原性气体或惰性气体下烧结,完成型壳的制备。
这种型壳强度高,稳定性好,但是成本很高,一般生产中不会使用。
难熔化合物主要有碳化物、硼化物、氮化物、硫化物等,这些材料生产成本偏高,大部分需要人工合成,而且用作锆合金熔模铸造的型壳材料时效果也不如其他材料,因此一般只在实验研究中才会使用。
氧化物是熔模铸造使用最广泛的面层耐火材料,尤其是作为锆及锆合金熔模铸造的型壳材料,具有很大的优势。首先,氧化物在烧结中不会被氧化,节约了使用真空或保护性气氛的成本,而且不会吸附气体;其次,氧化物的保温性好,能够有效降低金属液的冷却速度,保证充型得更好。在锆合金的工业生产中,Y2O3和ZrO2是使用最多的铸型材料,其他工业中使用较多的氧化物材料大多不适合作为锆这类活泼金属的铸型材料。
黄湘云等[24]公开了一种制备锆及锆合金的熔模精密铸造氧化物陶瓷型壳的方法,使用电熔Y2O3粉涂于陶瓷型壳面层,再经过脱蜡、烧结等过程制备出可用于浇铸的型壳,通过这种方法生产出的锆及锆合金铸件总体质量高、表面光洁度高、表面污染层厚度小于100μm,可用于生产壁厚小于3mm的复杂锆及锆合金铸件。张宁等[25]发明了一种用于制备钛锆合金铸件的精密铸造成型方法,使用粉末状W或W的化合物以及Y2O3粉料的混合物作为面层材料,型壳制成后在真空下进行离心浇铸或重力浇铸,该方法实现了钛锆基合金的近净成型,降低了加工成本和材料损耗,制备的铸件质量优异。
熔模铸造所制备的铸件尺寸精度高、表面光洁度好,几乎不再需要后续的加工,对于结构复杂、质量较小的铸件是最适合的铸造方法。但制作工艺复杂、蜡模的强度有限,导致其不适用于大型铸件的制备。对于大型锆及锆合金铸件,目前仍以石墨型铸造方法为主。
3、结语
(1)相比于其他常见金属,锆及锆合金的研究起步较晚、发展缓慢,至今只有70多年的发展历史。但是锆及锆合金又是当今不可或缺的一种材料,尤其是核工业领域,因此对锆及锆合金铸造工艺的研究仍任重而道远。
(2)目前用于锆及锆合金铸造的方法主要有硬模铸造、砂型铸造和熔模铸造三种。其中砂型铸造几乎不在工业生产中使用;硬模铸造主要应用在结构简单、对表面质量要求不高的大型铸件中,而且型壳一般使用的是机加工石墨型;熔模铸造适用于结构复杂、对尺寸精度要求高的中小型铸件,一般选择氧化物作为型壳面层材料。目前常用的耐火材料仍无法满足锆合金铸件的质量要求,还需进一步探索性能优异、与锆合金铸件匹配度较高且成本在合理范围内的新型耐火材料。BaZrO3是一种正在研发中的新型耐火材料,与Y2O3、ZrO2相比成本更低,具备独特的性能,在锆及锆合金铸造上具有很好的应用前景[20]。
(3)真空自耗电极电弧凝壳熔炼技术是目前主要使用的锆及锆合金熔炼方式,但其能耗较高、工艺复杂。真空感应凝壳熔炼技术与其相比成本更低,还能更好地控制金属液温度的均匀性,提高充型能力,有效提高锆及锆合金铸件质量。
参考文献
1 张孝全.稀有金属材料与工程,1983(2),84.
2 胡娟,李刚,张天广,等.金属世界,2020(3),23.
3 李献军.钛工业进展,2011,28(1),38.
4 贾豫婕,林希衡,邹小伟,等.中国材料进展,2022,41(5),354.
5 WarrBD,DerHeidiV,MaguireA.In:ZirconiumintheNuclearIndus-try,EleventhInternationalSymposium.Pennsylvania:ASTM,1996.
6 ShcbaldovPV,PerregudMM.In:ZirconiumintheNuclearIndustry,TwelfthInternationalSymposium.Pennsylvania:AmericanSocietyforTestingandMaterials(ASTM),2000.
7 ComstockRJ,SchoenbergerG,SableG.In:ZirconiumintheNuclearIndustry,EleventhInternationalSymposium.Pennsylvania:ASTM,1996.
8 王旭峰,李中奎,周军,等.热加工工艺,2012,41(2),71.
9 陈鹤鸣,马春来.核反应堆材料腐蚀及其防护,原子能出版社,1984.
10MardonJP,CharquetD,SenevatJ.OpticalMaterials,2000,1354(125),505.
11刘建章.核结构材料,化学工业出版社,2007.
12http://www.mlsdtk.com/n6758881/n6758890/c6812243/content.html.
13http://finance.people.com.cn/n1/2021/0611/c1004-32128193.html.
14ЛАСТОГКИНРР,王华森.稀有金属材料与工程,1975(7),71.
15谢成木.钛及钛合金铸造,机械工业出版社,2004.
16谢华生,赵军,刘时兵,等.中国专利,CN201310269760.8,2015.
17刘升迁.中国专利,CN201310516296.8,2015.18刘健.中国专利,CN201410268653.8,2014.
19黄湘云,薛芃,李彩虹,等.中国专利,CN201210421852.9,2015.
20李宝同,陈光耀,康菊芸,等.钛工业进展,2017,34(1),6.
21TheodoreO.U.S.Patent,3257692,1966.
22lichME,MikhailovichKA,IvanovichIA,etal.U.S.Patent,3389743,1968.
23ZusmanRH,VoieLEL.U.S.Patent,3485288,1969.
24黄湘云,朱广.中国专利,CN201010529357.0,2013.
25张宁,纪志军,张健辉,等.中国专利,CN202211151771.1,2023.
包春玲,通信作者,中国机械总院集团沈阳铸造研究所有限公司研究员、硕士研究生导师。2003年沈阳工业大学材料加工工程专业本科毕业,2006年沈阳工业大学材料加工工程专业硕士毕业后到沈阳铸造研究所工作至今,2020年机械科学研究总院机械设计及理论专业博士毕业。目前主要从事钛合金、钛铝合金精密铸造成形等方面的研究工作。发表论文20余篇,包括钛合金、钛铝合金研究进展,镁合金管材挤压,钛合金、钛铝合金材料及工艺研究等。
相关链接